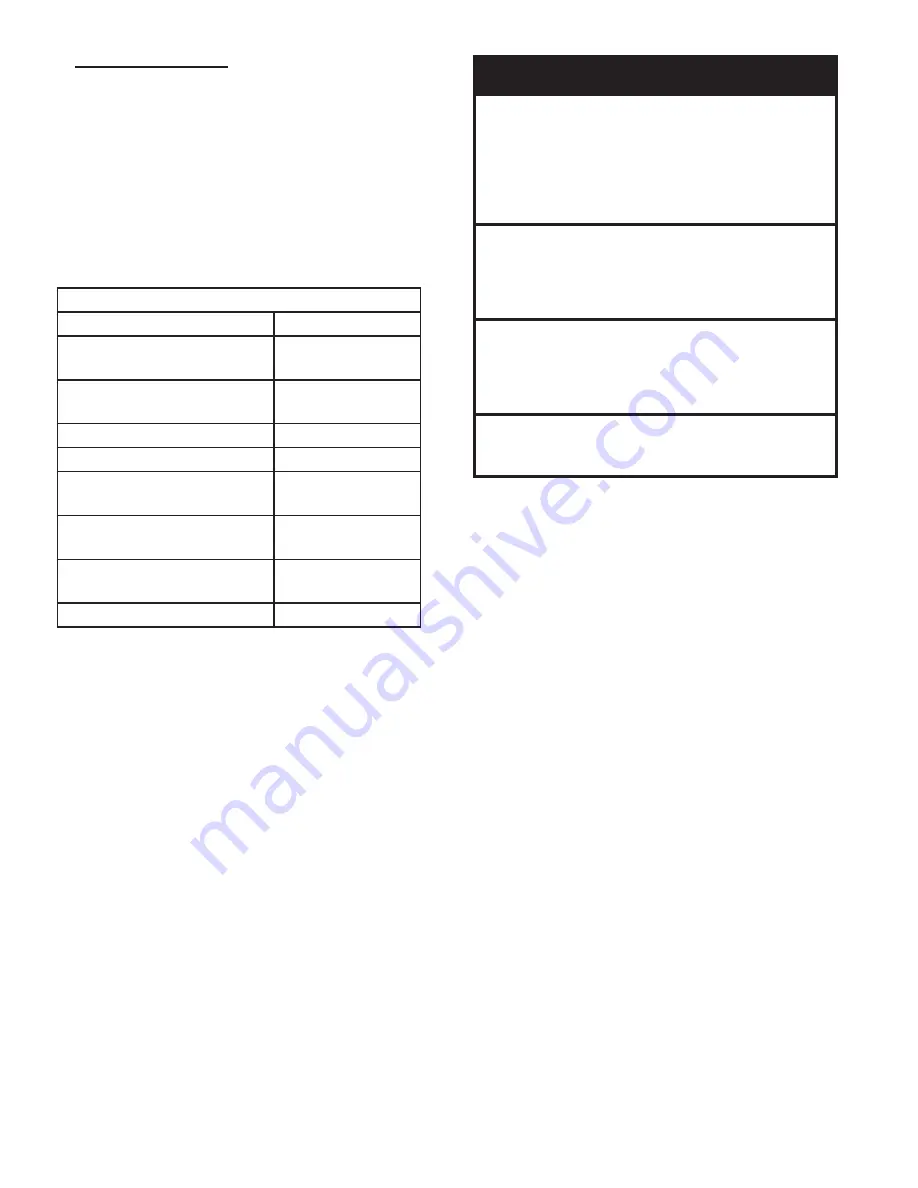
18
C. WATER TREATMENT
The quality of water used in the heating system is essential
for the successful operation and longevity of the system
components. A successful water treatment plan will help to
maintain efficiency, reduce the regularity of repair and/or
replacement, and extend the working life of the boiler
and other system equipment. If left untreated, poor water
quality could cause a number of problems including, but not
limited to, oxidation, scaling, corrosion, and fouling. See
Table 1 for examples of typical chemical agents found in
untreated water along with their potential effects.
Table 1: Chemical Agents and Effects
Compound
Effect
Calcium Carbonate
(CaCO
3
)
Soft Scale
Calcium Bicarbonate
(CaHCO
3
)
Soft Scale, CO
2
Calcium Sulphate (CaSO
4
) Hard Scale
Calcium Chloride (CaCl
2
)
Corrosion
Magnesium Carbonate
(MgCO
3
)
Soft Scale
Magnesium Bicarbonate
(MgHCO
3
)
Corrosion, Scale
Magnesium Sulphate
(MgSO
4
)
Corrosion
Silicon Dioxide (SiO
2
)
Hard Scale
Since the condition of water varies from location to
location, it is impossible to prescribe a one-size-fits-all
treatment plan for the system water. In order to develop
an effective water treatment plan, it will be necessary to
gain knowledge of the impurities dissolved in the water.
Once all the impurities are identified, the proper treatment
plan can be established. Therefore, it will be essential to
obtain the expertise of a qualified industrial water treatment
professional for establishing a treatment plan.
In addition, a periodic testing/sampling plan should
be developed. The intent of the plan should be to: (1)
ensure the protection of the boiler and system equipment,
(2) prevent an unforeseen system failure, (3) provide
information for use in addressing the water quality, and (4)
to confirm the proper concentration of chemicals in use.
CAUTION
The water shall have a maximum water hardness
of 8.5 grains or 150 ppm. The recommended
pH range is 8.8 to 9.2. However, other aspects
of water quality can affect boiler operation and
longevity. A qualified water treatment expert
should be consulted to develop a complete
water treatment plan.
Oxygen contamination of boiler water will cause
corrosion of iron and steel boiler components,
and can lead to boiler failure. Thermal Solutions
Standard Warranty does not cover problems
caused by oxygen contamination of boiler water.
Proper water treatment and boiler maintenance
is required to avoid scale build-up on the inside
of the boiler. Thermal Solutions Standard
Warranty does not cover problems caused by
scale build-up.
When using Glycol products, all Glycol
manufacturers' requirements, including rust
inhibitors, must be adhered. Max 50% Glycol.
Содержание EVO-1000
Страница 12: ...12 Figure 3 Sidewall Positive Pressure Venting Optional Figure 2 Sidewall Positive Pressure Venting...
Страница 13: ...13 Figure 4 Vertical Pressurized Venting...
Страница 15: ...15 Figure 5 Typical Negative Pressure Conventional Venting...
Страница 17: ...17 Figure 7 Vertical Air Intake Piping...
Страница 26: ...26 Figure 9a Standard UL FM CSD 1 Wiring Diagram on off EVO 500 2000...
Страница 27: ...27 Figure 9b Standard UL FM CSD 1 Wiring Diagram Modulation EVO 500 2000...
Страница 30: ...30 Figure 11 Modular System Horizontal Air Intake Piping...
Страница 31: ...31 Figure 12 Modular System Vertical Air Intake Piping...
Страница 32: ...32 Figure 13 Modular System Typical One Pipe Water Piping...
Страница 33: ...33 Figure 14 Modular System Typical Primary Secondary Water Piping...
Страница 34: ...34 Figure 15 Modular System Typical Primary Secondary without System Pump...
Страница 35: ...35 Figure 16 Modular System Typical Reverse Return Water Piping...
Страница 36: ...36 Figure 17 Modular System Reverse Return with System Pump Only...
Страница 37: ...37 Figure 18 Modular System Typical Primary Secondary with Reverse Return...
Страница 47: ...47 This Page Intentionally Left Blank...
Страница 48: ...48 Troubleshooting Guide B Troubleshooting Guide...
Страница 49: ...49 Troubleshooting Guide...
Страница 53: ...53 This Page Intentionally Left Blank...
Страница 54: ...54 Figure 19 Combustion Chamber Assembly...
Страница 56: ...56 Figure 20 Burner Assembly FRONT VIEW TOP VIEW...
Страница 58: ...58 Figure 21 UL FM CSD 1 Main Gas Train Assembly...
Страница 60: ...60 Figure 22a DB B DB B w POC Gas Train 500 750 Figure 22b DB B DB B w POC Gas Train 1000 2000...
Страница 62: ...62 Figure 23 Jacket Panels 4D 4J 4C 4B 4F 4I 4G 4E 4R 4K 4H 4J 4N 4M 4L 4Q 4A 4P 4P...
Страница 64: ...64 Figure 24a Control Panel Assembly On Off...
Страница 66: ...66 Figure 24b Control Panel Assembly Modulation...
Страница 68: ...68 Figure 25 Bishop Pilot Assembly...
Страница 72: ...72 NOTES...
Страница 73: ...73 NOTES...
Страница 74: ...74 NOTES...
Страница 75: ...75 NOTES...