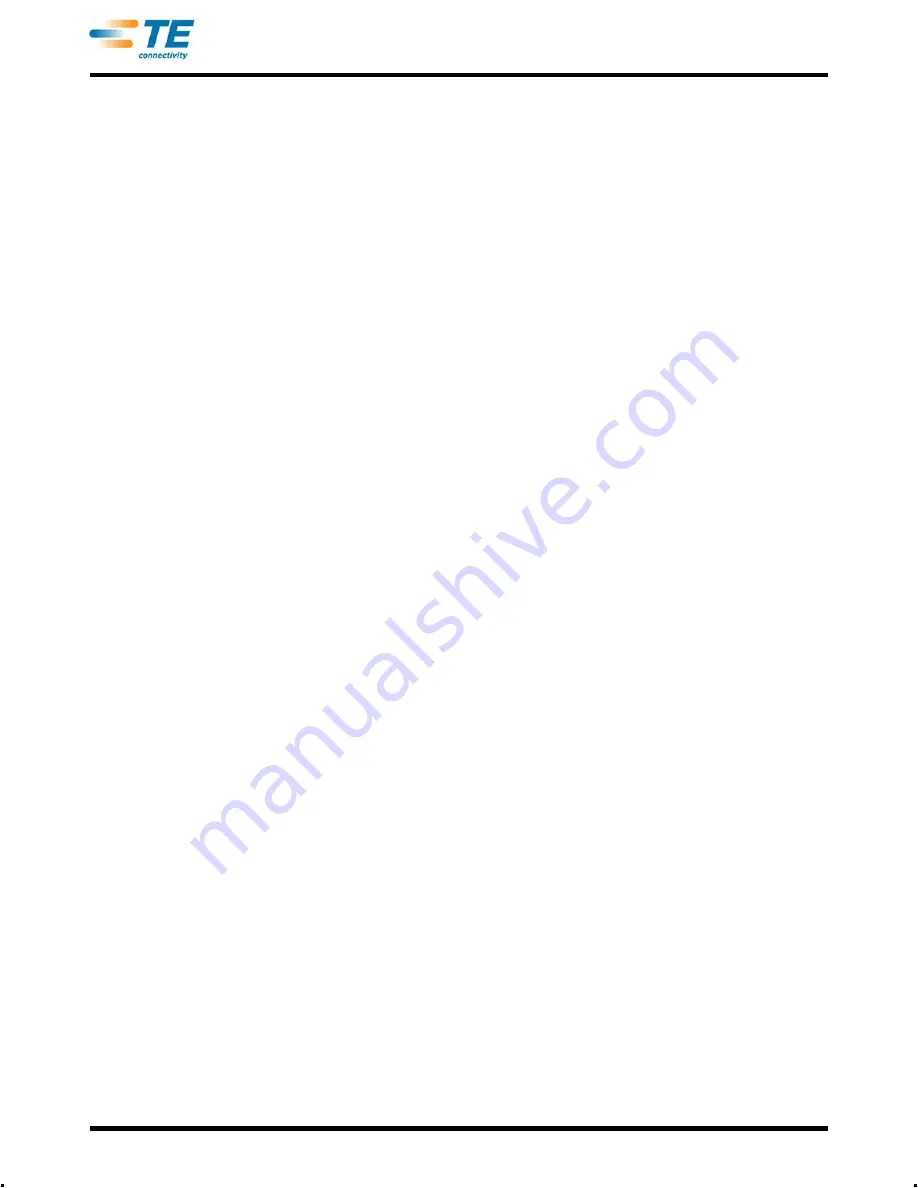
409-10100
8 of 59
Rev C
With the “Quick Headroom Check” (described in Paragraph 4.9), you will be able to have a better
understanding of how successful Crimp Quality Monitoring will be with the wire and terminal combination you
are running. A headroom of greater than 35% is the number you are looking for
.
B. Crimp Height
The crimp height is the measured height of the terminal on the wire. The CQM II uses a patented method to
analize data from the precision sensors in order to calculate the crimp height of the terminal.
The
maximum
value for a “good crimp” is the nominal plus the tolerance. The
minimum
value for a “good
crimp” is the nominal minus the tolerance.
C. Work Index
The work index is a value that is used to compare the relative position of a specified section of the crimp curve
that occurs while the wire and terminal combination is being compressed.
To establish the initial range for a good work index range, values are collected from “Learn” crimps that are
“Accepted as good,” to create a work index history.
A mean value and standard deviation are calculated from the values in the history. These values are used
to
establish a range of good work index values.
The work index is a dimensionless value.
Work index is a process monitoring analysis method that provides a history of its analysis that can be useful to
see how the crimping process may change over time.
D. Peak Force
The peak force is the maximum force reading that occurs during the crimp, minus the idle force reading.
The
peak force is a relative value. It has no specific units associated with it.
To establish the initial range for a good peak force range, values are collected from “Learn” crimps that are
“Accepted as good,” to create a peak force history.
A mean value and standard deviation are calculated from the values in the history. These values are used
to
establish a range of good peak force values.
The peak force is the maximum force reading that occurs during the crimp minus the idle force reading.
The peak force is a relative value. It has no specific units associated with it.
Peak Force a process monitoring analysis method that provides a history of its analysis that can be useful to
see how the crimping process may change over time.
E. Point-to-Point (P2P) Analysis
A series of points are established along the crimp curve in the P2P analysis. During the “Learn” process the
CQM II computes means and standard deviations for each point and updates the mean and standard
deviation for each point with every good crimp within an acceptable update range. During Production each
point is compared to its upper and lower control limits, and if no points are out of their limits the analysis
method considers the crimp to be a PASS crimp. A sensitivity value determines the amount of standard
deviations allowed at each point. There is also a Fixed Upper and Lower control limits that get established by
the first 30 PASS Crimps. Each point is checked both the fixed and non-fixed upper and lower control limits to
determine if the crimp is good.
F. Fast Fourier Transform (FFT) Analysis
The FFT analysis method converts the force profile into its component frequencies. It computes mean and
standard deviation for each of the lowest 32 frequencies from the learn crimps updates the mean and
standard deviation with each good crimp. The FFT display tab displays a graph of the tolerance limits and the
previous crimp computed frequency amplitudes. The tolerance limits are determined by the sensitivity
selected by the user (default is 2.0) times the computed standard deviations for each frequency. More than
five frequencies are outside the tolerance limits the crimp status is FAIL. Otherwise the crimp status is PASS.
G. Force Only Mode
In certain custom machine applications, the CQM II can operate with a force sensor
only
and no position
sensor. A trigger sensor is used to signal the crimp event. In this mode of
operation, the only analysis
Содержание Crimp Quality Monitor II
Страница 30: ...409 10100 30 of 59 Rev C...
Страница 41: ...409 10100 41 of 59 Rev C...