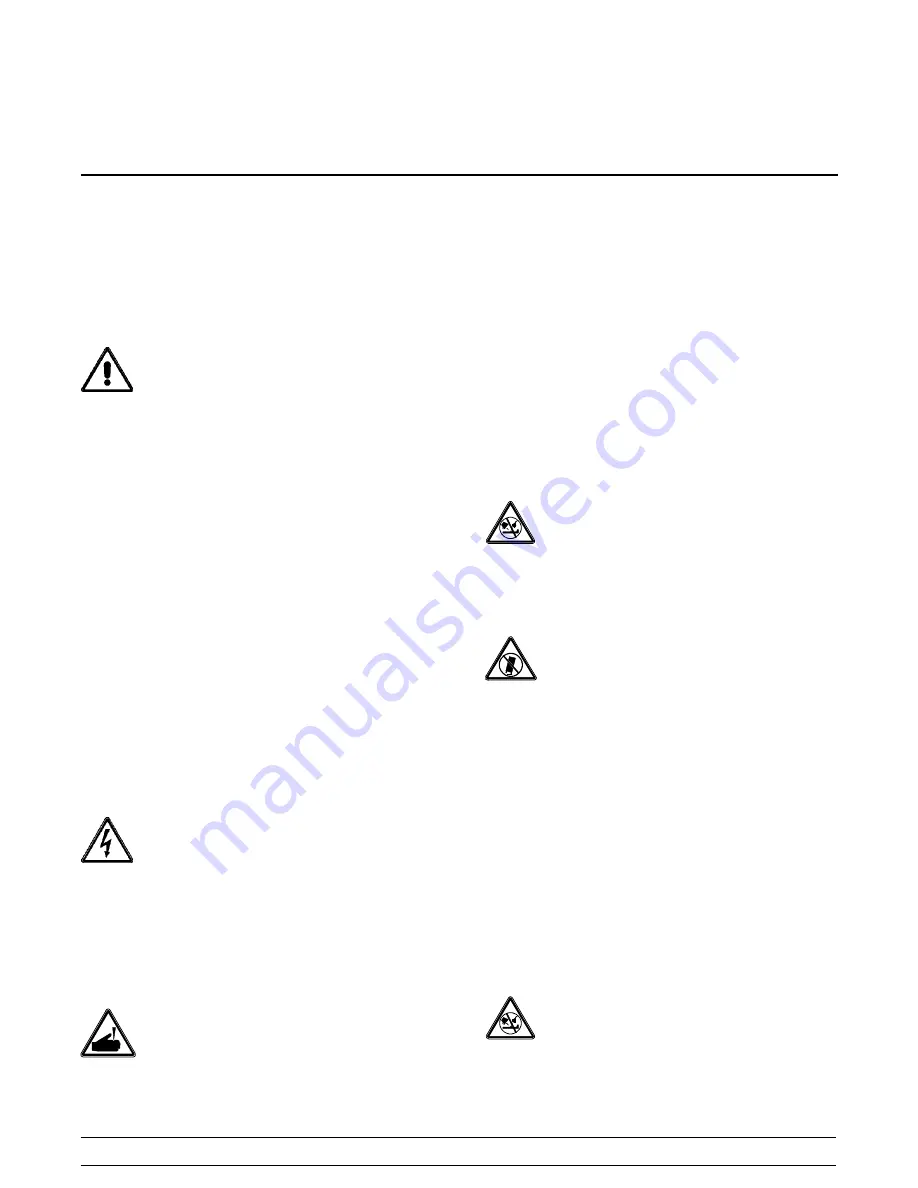
1
Model H60
To the Installer
131108
Section 1
To the Installer
The following information has been included in the
manual as safety and regulatory guidelines. For
complete installation instructions, please see the
Installation Checklist.
Installer Safety
In all areas of the world, equipment should be
installed in accordance with existing local codes.
Please contact your local authorities if you have any
questions.
Care should be taken to ensure that all basic safety
practices are followed during the installation and
servicing activities related to the installation and
service of Taylor equipment.
S
Only authorized Taylor service personnel
should perform installation and repairs on the
equipment.
S
Authorized service personnel should consult
OSHA Standard 29CFRI910.147 or the
applicable code of the local area for the
industry
standards
on
lockout/tagout
procedures before beginning any installation
or repairs.
S
Authorized service personnel must ensure
that the proper PPE is available and worn
when required during installation and service.
S
Authorized service personnel must remove all
metal jewelry, rings, and watches before
working on electrical equipment.
The main power supply(s) to the machine
must be disconnected prior to performing any repairs.
Failure to follow this instruction may result in personal
injury or death from electrical shock or hazardous
moving parts as well as poor performance or damage
to the equipment.
Note: All repairs must be performed by an
authorized Taylor Service Technician.
This unit has many sharp edges that can
cause severe injuries.
Site Preparation
Review the area where the unit will be installed before
uncrating the unit. Make sure that all possible hazards
to the user and the equipment have been addressed.
For Indoor Use Only:
This unit is designed to operate
indoors, under normal ambient temperatures of
70
_
-75
_
F (21
_
-24
_
C). The freezer has successfully
performed in high ambient temperatures of
104
_
(40
_
C) at reduced capacities.
This unit must
NOT
be installed in an area
where a water jet or hose can be used.
NEVER
use a
water jet or hose to rinse or clean the unit. Failure to
follow this instruction may result in electrocution.
This unit must be installed on a level surface
to avoid the hazard of tipping. Extreme care should be
taken in moving this equipment for any reason. Two or
more people are required to safely move this unit.
Failure to comply may result in personal injury or
equipment damage.
Uncrate the unit and inspect it for damage. Report any
damage to your Taylor Distributor.
This piece of equipment is made in the USA and has
USA sizes of hardware. All metric conversions are
approximate and vary in size.
This machine is designed for indoor use only.
DO NOT
install the machine in an area where
a water jet could be used. Failure to follow this
instruction may result in serious electrical shock.