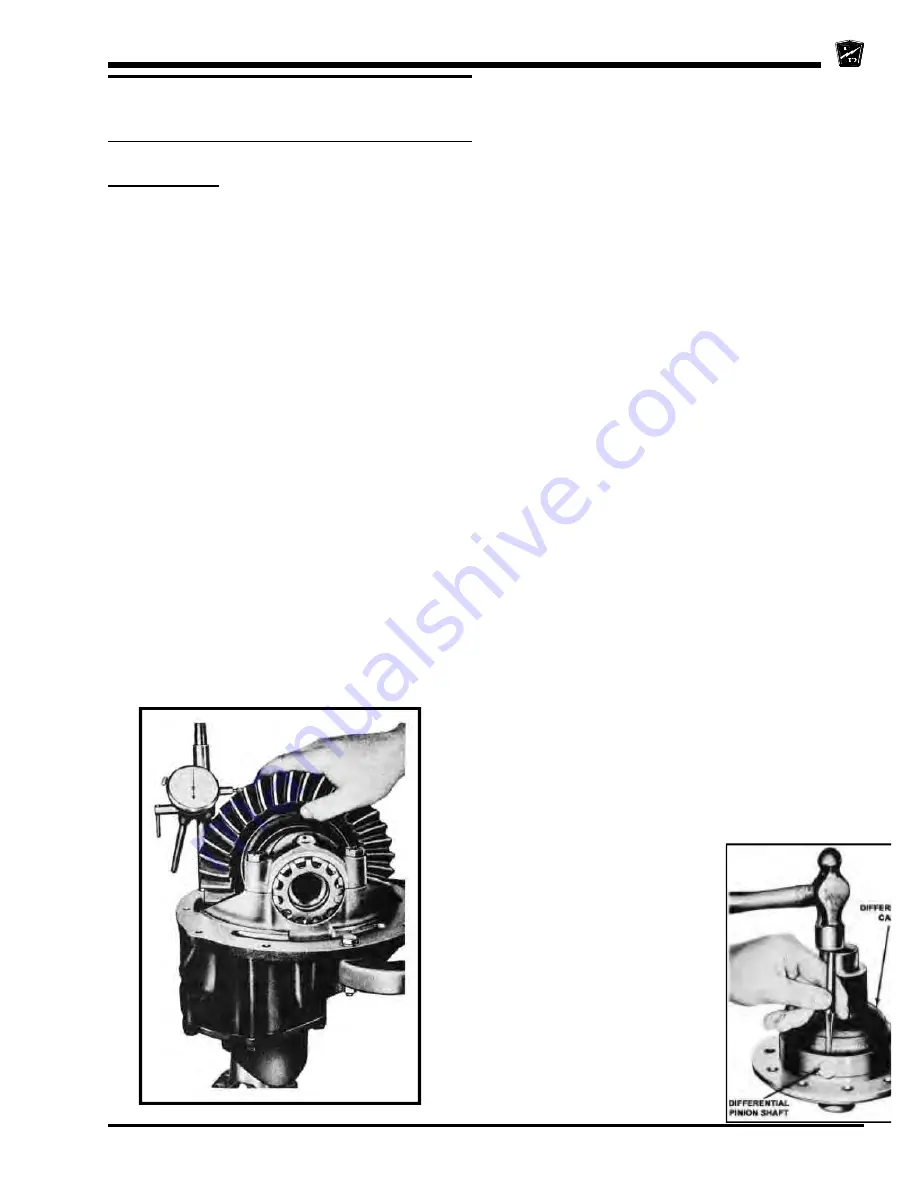
Maintenance, Service, and Repair
Transaxle - SS-534
Page 5
DIFFERENTIAL ASSEMBLY (3
RD
MEMBER)
Disassemble
NOTE: Bearings and races must be replaced as a
set. If any one bearing or race is worn, its
mate must also be replaced. It is
recommended to replace all bearings and
races in the 3rd member as a set.
1.
Drain the oil from the differential housing and chain
case. Refer to section
Change the Oil
for
information regarding draining the oil.
2.
Remove the transmission assembly from the
vehicle. Refer to
Transmission Assembly:
Remove and Install
for information regarding
removing the transmission.
3.
Remove both rear axle assemblies. Refer to section
Rear Axle: Remove and Install
for information
regarding removing the axles.
4.
Remove the chain case and backing plate from the
3rd member. Refer to section
Chain Case:
Disassemble
for information regarding removing
the chain case.
5.
Remove the nuts holding the 3rd member to the
axle housing and remove the 3rd member from the
housing.
6.
Install a spacer on the pinion shaft so that the pinion
nut can be installed and tightened.
Measuring backlash
7.
While rotating the pinion shaft, tighten the pinion
nut to 100 foot pounds (142 Nm).
8.
Measure and record the ring and pinion gear
backlash. This setting will be used during
reassembly.
9.
Remove the pinion housing and pinion gear from
the 3rd member.
NOTE: Do not lose the spacers and shims in the
pinion housing or the pinion housing shim(s).
10. If required, remove the rear tapered bearing from
the pinion shaft and discard.
NOTE: Do not remove the bearing unless it requires
replacement. Removing the rear bearing will
damage the bearing. Replacing this bearing
will require re-shimming of the pinion shaft.
11. If required, remove the bearing races from the pinion
housing.
12. Mark the differential bearing caps and 3rd member
housing so that they can be reassembled in their
original location. Refer to illustration at end of
section.
NOTE: The caps cannot be interchanged or replaced.
If the caps are lost or damaged then the entire
3rd member assembly must be replaced.
13. Remove the differential bearing caps, bearing
adjusting nuts and races.
14. Remove the differential assembly from the 3rd
member.
15. Mark the ring gear and differential housing so that
the ring gear can be reinstalled in the same
orientation.
16. Remove the bearings from the differential housing
and discard.
NOTE: Removing the bearings will damage the
bearings. Do not remove the bearings unless
they require replacement.
17. Remove the ring gear from the differential housing.
18. Remove the differential shaft
locking roll pin.
19. Split the 2-piece differential
housing.
20. Drive the differential pinion
shaft out of the housing with
a brass drift punch.
21. Remove the differential
gears, axle gears, and thrust
washers.
Содержание MX-026-00
Страница 1: ...F 5 1 4 2 0 1 8...
Страница 2: ......
Страница 6: ...TAYLOR DUNN...
Страница 12: ...TAYLOR DUNN...
Страница 32: ...TAYLOR DUNN...
Страница 52: ...TAYLOR DUNN...
Страница 62: ...TAYLOR DUNN...
Страница 72: ...TAYLOR DUNN...
Страница 81: ...Maintenance Service and Repair Transaxle SS 534 Page 9 EXPLODED VIEW...
Страница 86: ...TAYLOR DUNN...
Страница 94: ...TAYLOR DUNN...
Страница 148: ...TAYLOR DUNN...
Страница 157: ...4 1 1 2 6 9 4 4 1 1 2 6 9 5...
Страница 158: ...Illustrated Parts Parts Page 10 Axle Assembly Transaxle SS 536 SS 546 MX 600...
Страница 159: ......
Страница 162: ......
Страница 163: ......
Страница 164: ...Illustrated Parts Parts Page 16 Brakes Rear Axle SS 534 Brakes Rear Axle SS 536 SS 546 MX 600...
Страница 169: ...7 5 1 4 8 4 1...
Страница 170: ...7 5 1 4 8 4 2...
Страница 180: ...Illustrated Parts Parts Page 32 Steering Linkage Geared SS 536 SS 546 MX 600...