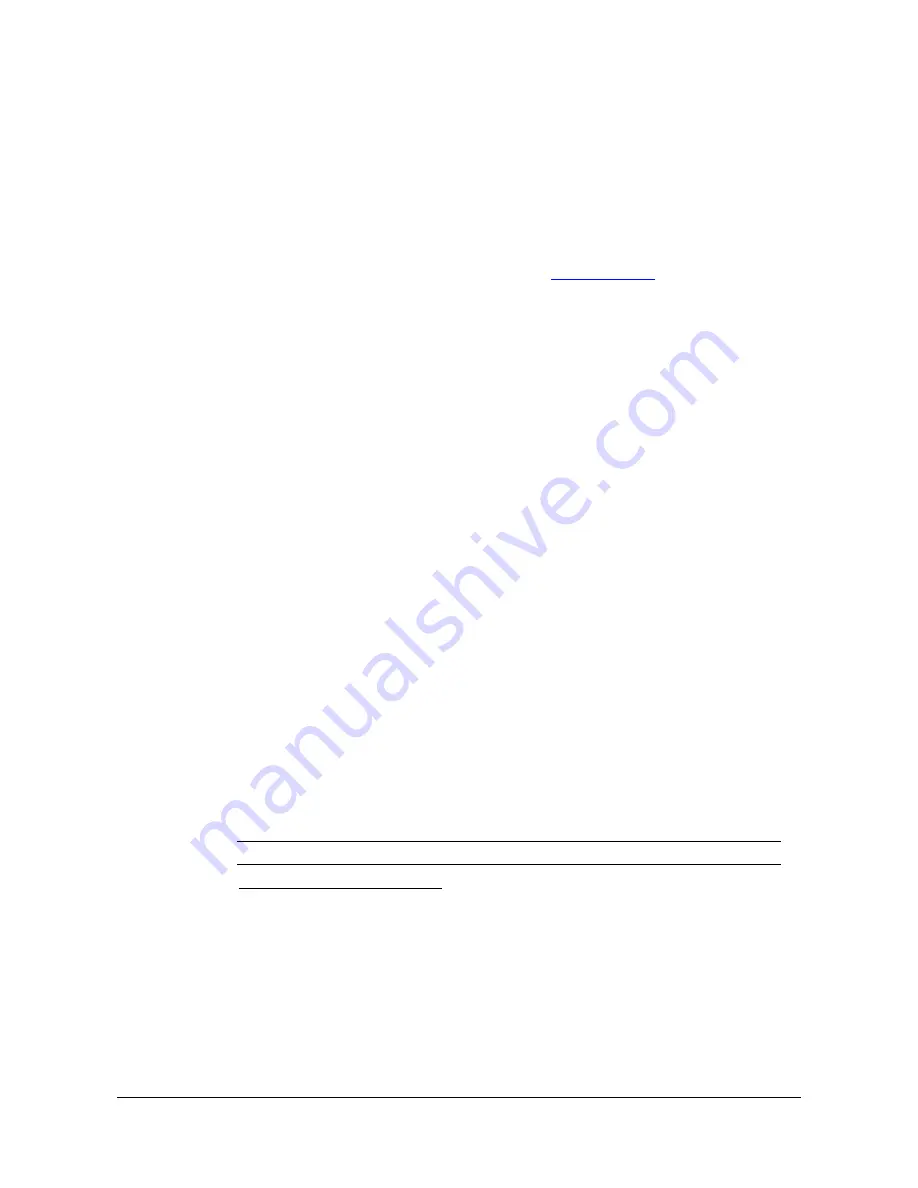
Specifications
0705
TTPM3 Printer/Encoder–Technical Manual
71
9.2 Document
stock
The TTPM3 printers are produced and calibrated for, and tested with the customer’s
ticket stock. To ensure accurate ticket issuing, we do require 100 tickets of the customer
ticket stock for each ordered printer.
9.2.1 Ticket
base
material
Type of paper
Ricoh 150UT 240
µ
, Mitsubishi TF 2475, and Tyco Sharkskin
are recommended. See
www.swecoin.se
for current
recommendation.
Material
Paper, 100 % chemical pulp, no ground wood permitted
Triplex
1
laminate
2
Plastic (polypropylene Sharkskin
TM
)
Stiffness
18–36 g/cm (in grain direction)
Thickness
Paper and laminate: 0.18–0.40
3
mm, 170–210 g/m²
Plastic (polypropylene Sharkskin
TM
): 0.18–0.25 mm
Factory setting: Set to the customer’s tickets. A minimum of 100
tickets per printer ordered must be sent to Swecoin when
ordering printers.
Curl
Deviation from flatness < 0.6 mm across the length, width, or
diagonal of the ticket
9.2.2 Coating
and
preprint
Thermal coating
Shall meet or exceed the ANSI 3.11 specification
Smoothness:
Max. 75 Sheffield units
Properties:
Same as fax grade 3
Top coating
The thermo-sensitive surface of the document stock can be
provided with a protective UV or moisture proofing top coating
Preprint
Tickets can be preprinted on one, or both sides.
Ink for thermo-sensitive side: Laser printer approved ink with-
out whiteners
Ink for magnetic stripe side: Offset ink
CAUTION!
– Never use abrasive inks as they reduce the life of the thermal print head.
1
Triplex is manufactured from three paper stocks. The middle is usually recycled paper, and the top and bottom are different papers.
2
Laminate with plastic core may destroy the printhead! DO NOT USE.
The perforation of the tickets may leave parts of the plastic core protruding through the surface of the ticket.
These plastic tongues may scratch the printhead, and also build up static electricity discharging through the printhead. This
may seriously limit the printhead life.
If plastic laminate still is used, care must be taken in the manufacturing process to avoid the plastic protrusion, and the printer
must be life-tested with the intended stock before taken into use.
3
0.18-0.32 mm for Frontload 1 and Frontload 2 versions of the printer