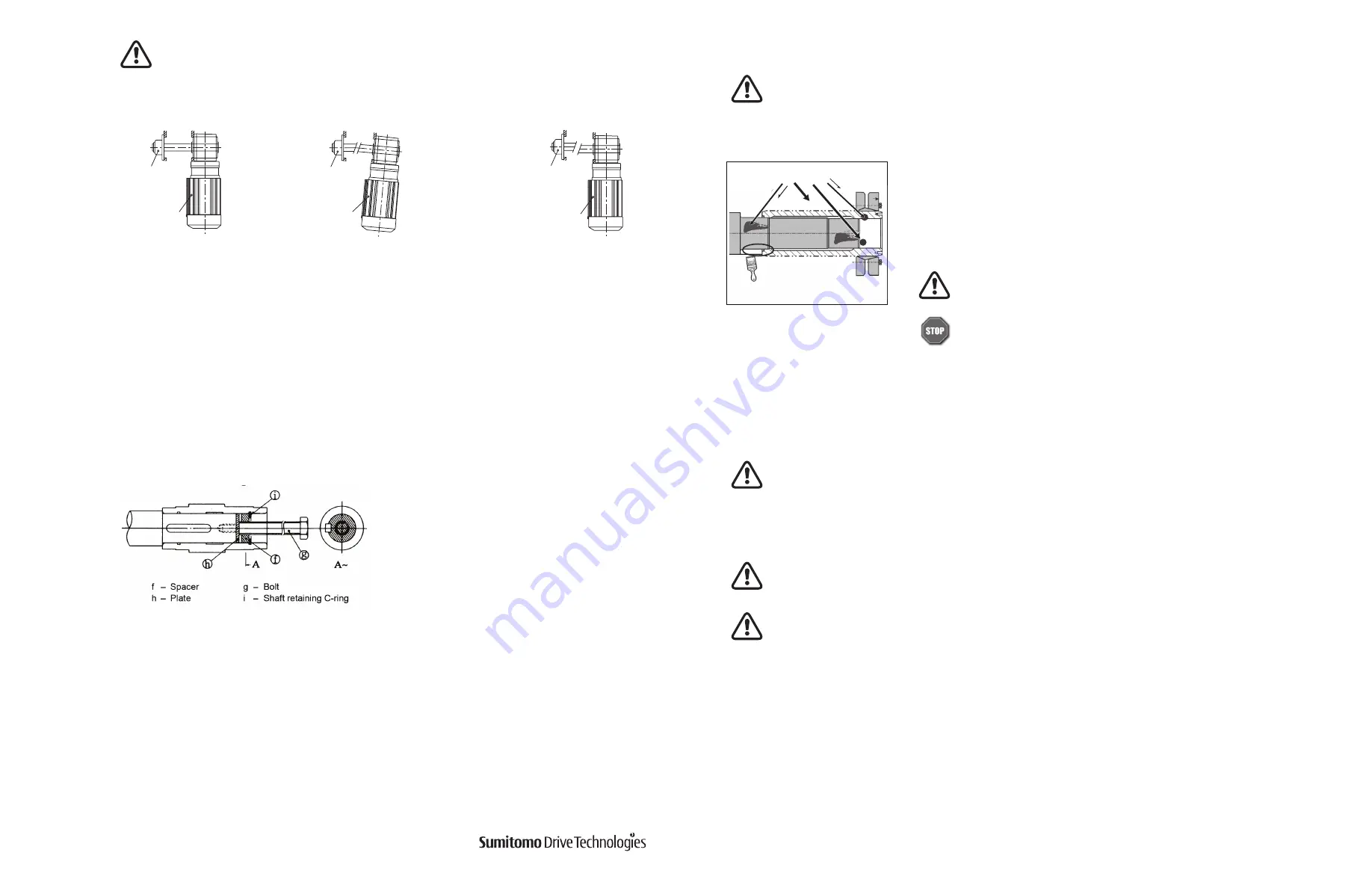
10
Hyponic®
Operating and Maintenance Manual
Hyponic® Operating and Maintenance Manual
11
www.SumitomoDrive.com
Note:
Customer should supply parts for setting, securing or removing the shaft.
Fig. 9
When installing the gearmotor when flange-mounted, ensure that the gearmotor and the
shaft of the driven machine are properly aligned so that the gearmotor is free from excessive
force
(Figure 8)
.
Fig. 8
Hyponic® hollow
shaft model
Bearing unit
Poor concentricity of driven
shaft and mounting flange
Incorrect
Hyponic® hollow
shaft model
Bearing unit
Poor perpendicularity of driven shaft
center and mounting flange surface
Incorrect
Hyponic® hollow
shaft model
Bearing unit
Correct
Shrink Disc
1
Clean and degrease contact surfaces; reducer shaft and bore, and the machine
driven shaft.
Apply Molykote 321 or an equivalent dry film lubricant to the driven shaft
projection opposite from the shrink disc.
2
Align the driven shaft with the reducer hollow bore and carefully slide unit onto the driven shaft.
If the fit is tight, strike on the reducer hollow bore with a mallet to assist in the assembly.
If using a soft non-metallic mallet during installation, strike
only
against the unit’s steel hollow bore.
Do not
strike the reducer housing or oil seal. Damage to the bearings, the housing, and/or the seals may occur.
Note:
If the fit is tight, use a jig such as the one shown in
Figure 5
to ease assembly.
Sumitomo does not supply a
mounting jig. This information is provided for reference only.
Never tighten locking screws before shaft installation. Inner ring may become permanently contracted even
at low tightening torques.
Ensure that all power switches are locked out before installing or removing shrink disc. Wear safety glasses
and protective clothing at all times
Before placing unit onto driven shaft,
do not apply grease, oil, or anti-seize grease
to the entire driven
shaft or to the bore of the shrink disc. Use of these friction-minimizing products will adversely affect the
ability of the unit to transmit torque.
3
Remove any wooden spacers that may have been used during shipping. Lightly lubricate the hub outside diameter
and shrink disc bore.
Degrease these areas
Apply Molykote 321
to this shaft area only
For food grade application, use food grade dry film lubricant.
Do not apply any friction minimizing compound to the driven shaft at
or near the shrink disc
d.
Removing the Shaft
Do not apply excessive force to the unit and shaft. Using a jig as shown in
Figure 9
will facilitate
removal of the shaft.