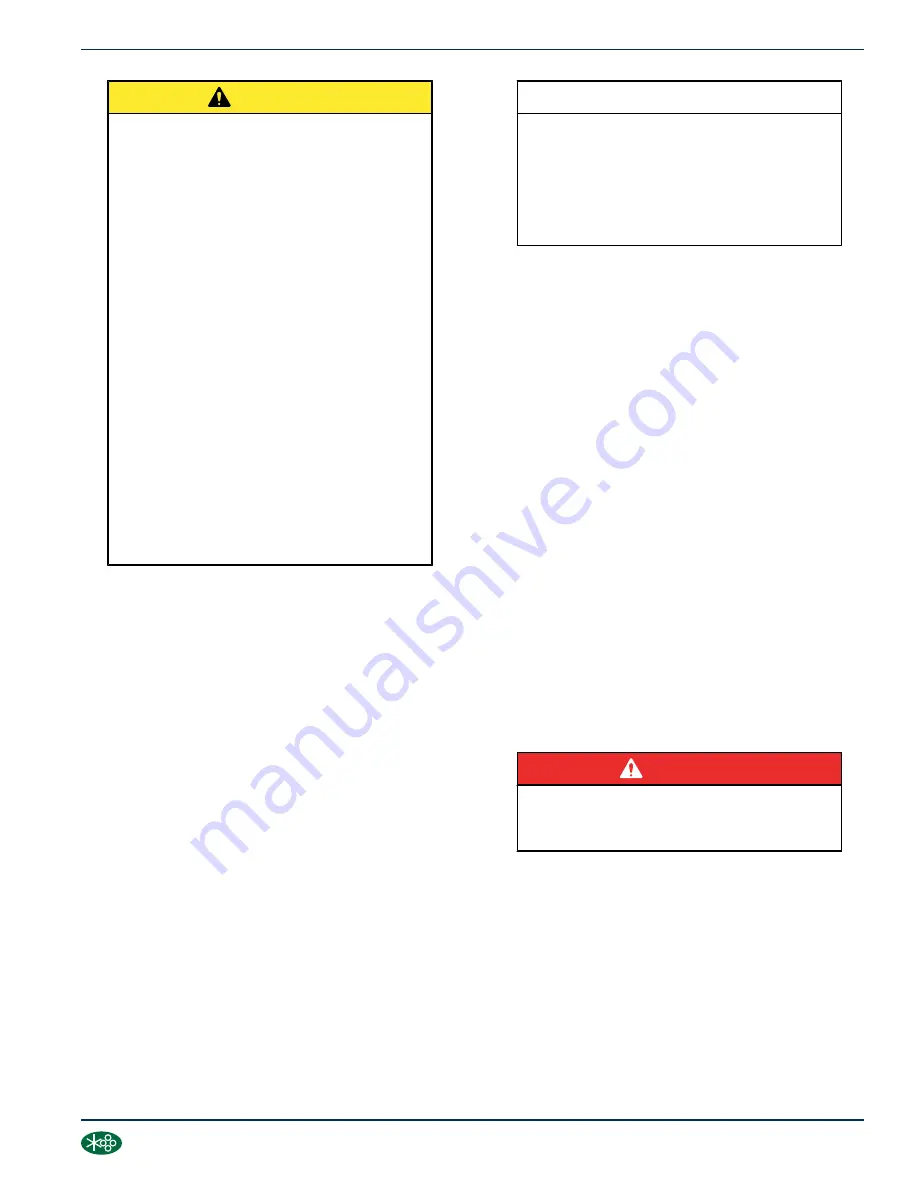
CAUTION
The use of plastic bowls on line filters
and other plastic airline components
without metal guards can be
hazardous. Synthetic coolants or the
additives used in mineral oils can alter
their structural integrity and create
hazardous conditions. Metal bowls
should be used on any pressurized
system for safety concerns.
"The Plastic Pipe Institute
recommends against the use of
thermoplastic pipe to transport
compressed air or other compressed
gases in exposed above ground
locations, e.g. in exposed plant
piping." (I)
Sullube should not be used with PVC
piping systems. It may affect the bond
at cemented joints. Certain other
plastic materials may also be affected.
(I) Plastic Pipe Institute,
Recommendation B, Adopted
January 19, 1972.
4.4 COUPLING ALIGNMENT CHECK
No coupling alignment is required; this machine is directly
driven.
4.5 FLUID LEVEL CHECK
The air compressor is shipped with the proper amount of
fluid installed. However, it is necessary to check the fluid
level at the time of installation and during continued
operation of the compressor. The fluid level is to be
checked when the compressor is in the SHUT DOWN
MODE (fluid level may not be visible when operating), and
by looking at the sight glass on the receiver tank. To be
able to see the fluid level it may be necessary to start the
machine and build the receiver tank pressure up to 10/20
psi and then shut down. If no fluid level is seen in the sight
glass add fluid to the center of the glass. Do not overfill in
any case. When a complete fluid change is performed, fill
the receiver tank to the maximum allowable fluid level,
which is center of the upper sight glass.
4.6 ELECTRICAL PREPARATION
Interior electrical wiring is performed at the factory.
Required customer wiring should be done by a qualified
electrician in compliance with OSHA, National Electrical
Code, and/or any other applicable state, federal and local
electrical codes concerning isolation switches, fused
disconnects, etc.
NOTE
Customer must provide electrical
supply power disconnect within sight
of machine. The fuse protecting the
circuit and the compressor must be
selected in accordance with the data
provided in the general information
section.
•
The compressor and drive should be provided with a
proper grounding conductor/earthed in accordance
with both local and National Electrical Code (NEC)
requirements.
•
Installation of this compressor must be in accordance
with recognized electrical codes and any local Health
and Safety Codes.
•
Feeder cables should be sized by the customer/
electrical contractor to ensure that the electrical circuit
the system is connected to is balanced and not
overloaded by any other electrical equipment. The
length of wiring from a suitable electrical feed point is
critical as voltage drop may impair the performance of
the compressor.
•
Feeder cable connections to incoming terminals L1-
L2-L3 should be tight and clean.
The applied voltage must be compatible with the motor
and compressor data plate ratings.
•
A starter hole is provided for incoming power
connection. If it is necessary to make a hole in the
control box in a different location, care should be taken
to not allow metal shavings to enter the starter and
other electrical components. If another hole is used,
the original hole must be blocked off with a suitable
knockout seal.
•
A few electrical checks should be made to help assure
that the first start-up will be trouble-free.
DANGER
Lethal shock hazards exist inside.
Disconnect all power at source and
lock out before opening or servicing.
1. Check incoming voltage. Be sure that the compressor
is wired for the correct incoming voltage.
2. Check the motor starter for correct size, properly sized
overload relay, and correct heaters for the load.
3. Check all electrical connections for tightness. Check
all grounding connection for bond.
4. “DRY RUN” the electrical controls by disconnecting
the three (3) motor leads from the starter. Energize the
control circuits by pressing the “I” (START) pad, and
check all protective devices to be sure that they will
de-energize the starter coil when tripped.
INSTALLATION
®
SULLAIR
®
1100e, 1500e, 1800e Operator’s Manual and Parts List
33
Содержание 1107e
Страница 13: ...THIS PAGE INTENTIONALLY LEFT BLANK DESCRIPTION SULL AIR 1100e 1500e 1800e Operator s Manual and Parts List 9...
Страница 34: ...SECTION 3 THIS PAGE INTENTIONALLY LEFT BLANK 30 1100e 1500e 1800e Operator s Manual and Parts List SULL AIR...
Страница 42: ...SECTION 5 THIS PAGE INTENTIONALLY LEFT BLANK 38 1100e 1500e 1800e Operator s Manual and Parts List SULL AIR...
Страница 50: ...SECTION 6 THIS PAGE INTENTIONALLY LEFT BLANK 46 1100e 1500e 1800e Operator s Manual and Parts List SULL AIR...
Страница 58: ...7 4 AIR INLET SYSTEM 02250157_200r02 SECTION 7 54 1100e 1500e 1800e Operator s Manual and Parts List SULL AIR...
Страница 62: ...7 6 FLUID PIPING 02250154 767R003 SECTION 7 58 1100e 1500e 1800e Operator s Manual and Parts List SULL AIR...
Страница 68: ...7 9 MOISTURE DRAIN 02250157_143R00 SECTION 7 64 1100e 1500e 1800e Operator s Manual and Parts List SULL AIR...
Страница 84: ...7 14 ENCLOSURE 02250155_649R05 SECTION 7 80 1100e 1500e 1800e Operator s Manual and Parts List SULL AIR...
Страница 100: ...SECTION 7 THIS PAGE INTENTIONALLY LEFT BLANK 96 1100e 1500e 1800e Operator s Manual and Parts List SULL AIR...
Страница 101: ...THIS PAGE INTENTIONALLY LEFT BLANK...