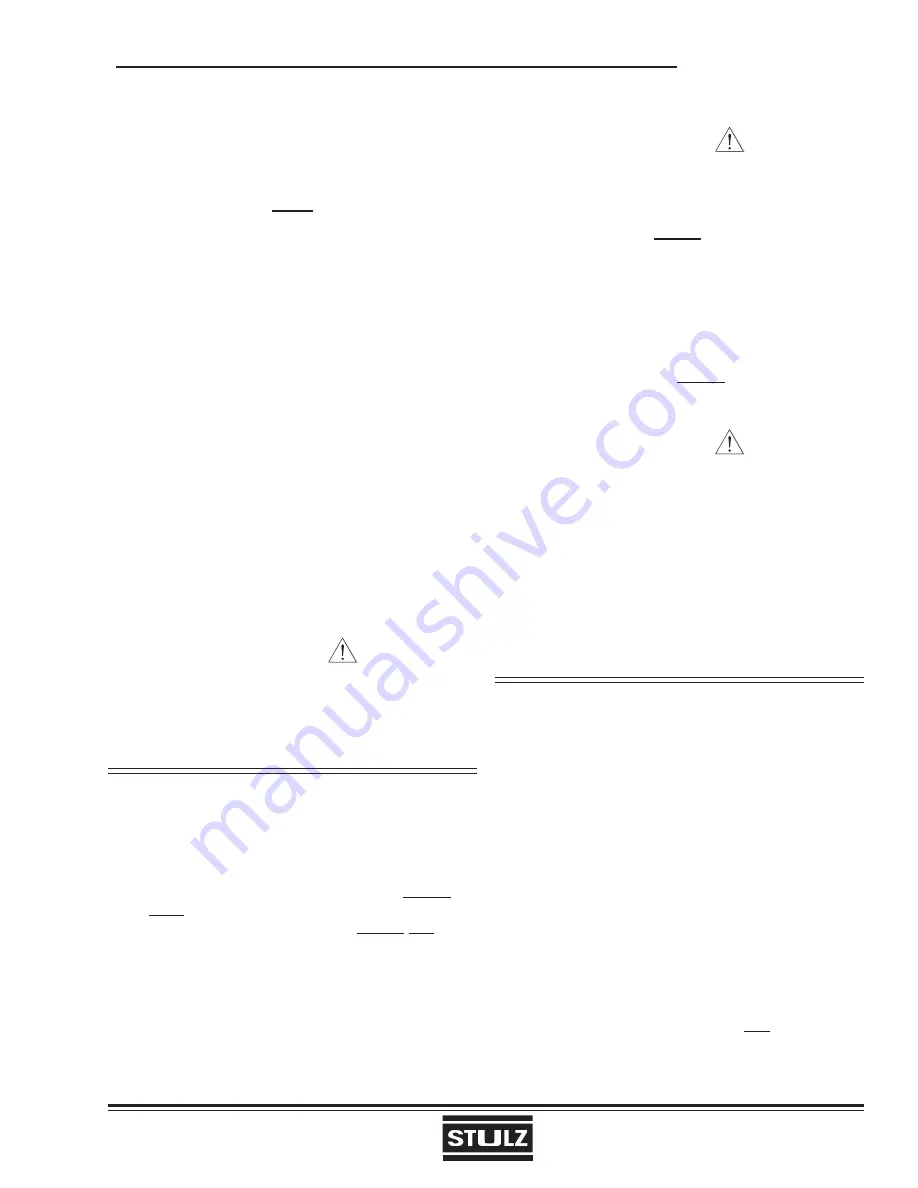
(Mar, 2012)
CeilAiR OHS Series Installation, Operation & Maintenance Manual
Air Technology Systems, Inc.
2-20
temperature-measuring device being well
insulated. The sub-cooling temperature should
be approximately 10-20ºF.
NOTE
Under cold climate conditions it is recommended to do
the following:
6. Block off the intake air to the condenser with
cardboard (or reduce the water glycol fl ow) until
a constant discharge pressure (225-280 psig)
can be obtained. This will lower the possibility of
overcharging and avoid the occasional bubbles
that may appear in the sight glass during fan
cycling. (For units with fan cycling only.)
7. If the unit has a hot gas reheat option, the previ-
ous steps are still followed except the hot gas
reheat valve must be opened to allow refrigerant
to fl ow into the reheat coil to obtain the proper
amount of unit charge. This process may need to
be repeated several times, which can be done by
enabling a call for dehumidifi cation. After cycling
the system through the hot gas reheat cycle, re-
check the system charge in the COOL-
ING-ONLY mode.
8. Ensure the crankcase heater is operational by
checking the amperage.
CAUTION
Remove the blockage to the air intake of the con-
denser (or restore the water/glycol fl ow).
9. Fill out applicable blocks of Warranty Registration
and Start-Up Checklist.
2.8.1.2.2 -30ºF Flooded Head Pressure Control
The following instructions are for charging systems with
fl ooded head pressure control using R-22 refrigerant.
1. Bleed air from hoses and “break” the system
vacuum by supplying R22
liquid
to the service
valve of the receiver until the receiver is full.
Then supply R22
vapor
to the suction port until
the pressure is raised to about 50 psig (low
pressure switch makes).
2. Referring to Section 3.0, start the system and
use the microprocessor controller to lower
the temperature set-point 3-5°F below room
temperature. This will ensure cooling remains on
during charging procedure.
CAUTION
An adequate heat load must be supplied to the unit
to ensure a proper charge.
3. After starting the system, immediately supply
R22
vapor
to the suction
port until the liquid line
sight glass is clear of all bubbles.
4. Raise the discharge pressure to 300-325 psig
and hold it constant by blocking the air intake of
the condenser.
5. Once the discharge pressure has stabilized for 5
to 10 minutes, additional refrigerant R22
vapor
must be added to the suction port until the “fl oat
ball” in the level indicator of the receiver begins to
fl oat.
CAUTION
Remove the blockage to the air intake of the con-
denser.
6. Take a superheat reading near the feeler bulb
from the thermal expansion valve. The ideal
superheat temperature is 12-15°F. The maximum
allowable superheat temperature is 20°F.
7. Ensure the crankcase heater is operational by
checking the amperage.
8. Fill out applicable blocks of Warranty Registration
and Start-Up Checklist.
2.8.2 R407C Refrigerant Charging
Procedures
R407C is a blended refrigerant recognized for being
safer for the environment. Refrigerants that are multi-
component blends have component parts with different
volatilities that result in a change in composition and
saturation temperature as evaporation and condensa-
tion occur. Typically, the composition of R407C vapor
is different than that of R407C liquid within a contained
system. The composition of liquid R407C refrigerant re-
mains relatively constant, however, the refrigerant vapor
tends to separate into its component parts even when
circulating. When charging a system using blended
refrigerants, it is essential that the composition of the re-
frigerant is maintained. To ensure correct composition,
introduce R407C into the system in liquid form rather
than vapor form. Cylinders which are not provided with
dip tubes should be inverted to allow only
liquid
refrig-
erant to charge the system. Keeping the temperature of
the cylinder below 85°F will help to maintain the correct
refrigerant composition while the cylinder is emptied.
Содержание CeilAiR Series
Страница 1: ... Mar 2012 CeilAiR OHS Series Installation Operation Maintenance Manual Air Technology Systems Inc ...
Страница 54: ... Mar 2012 CeilAiR OHS Series Installation Operation Maintenance Manual Air Technology Systems Inc NOTES ...
Страница 56: ... Mar 2012 CeilAiR OHS Series Installation Operation Maintenance Manual Air Technology Systems Inc ...
Страница 58: ... Mar 2012 CeilAiR OHS Series Installation Operation Maintenance Manual Air Technology Systems Inc ...