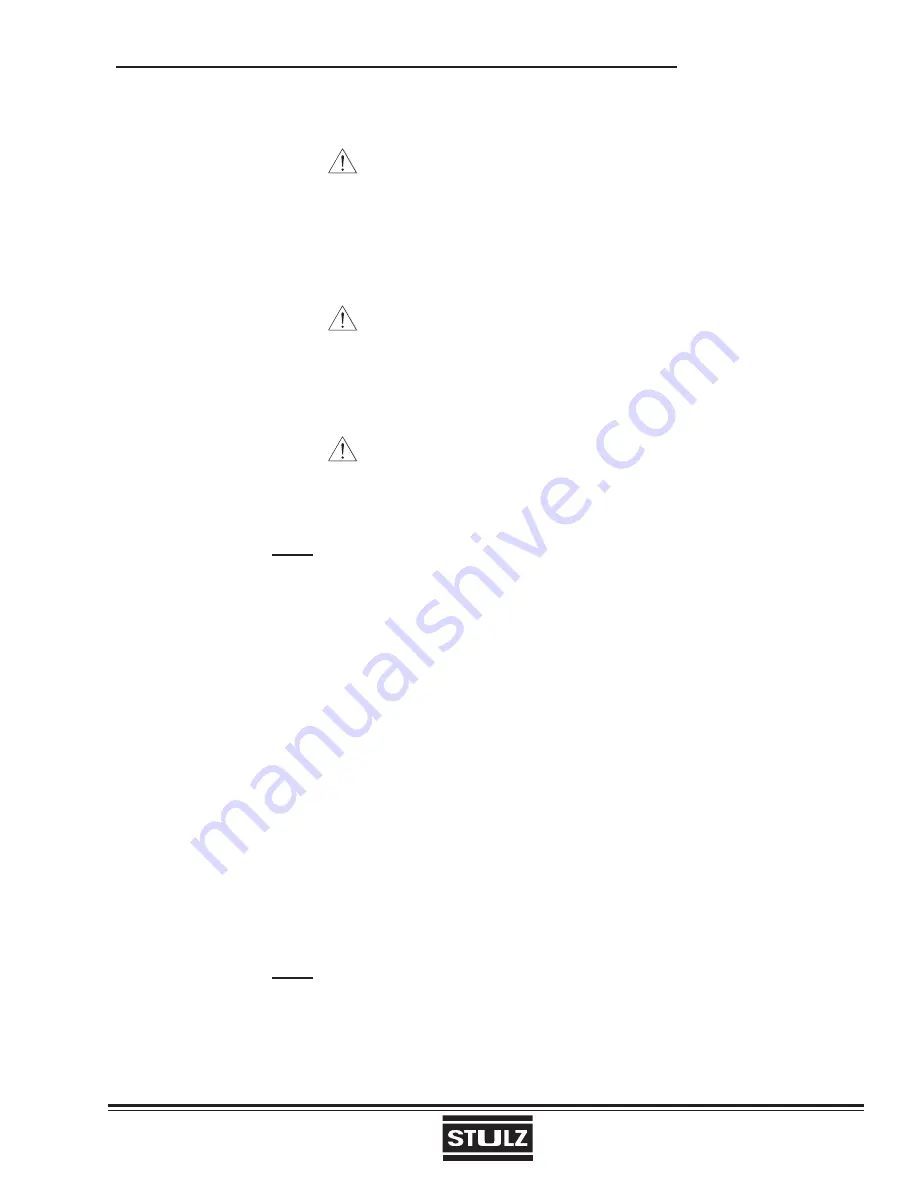
(Mar, 2012)
CeilAiR OHS Series Installation, Operation & Maintenance Manual
Air Technology Systems, Inc.
4-7
CAUTION
Damage to a replacement compressor caused
by improper system cleaning constitutes abuse
under the terms of the warranty. This will
VOID
THE COMPRESSOR WARRANTY.
Always
consult the factory prior to replacing the
compressor.
CAUTION
POE oil is used in systems with R-407C refriger-
ant. If a replacement compressor is provided, en-
sure that it is fi lled with POE oil before installing.
4.3.4.2 Standard Cleanout Procedure
CAUTION
Avoid touching or contacting the gas and oil with
exposed skin. Severe burns will result. Use long
rubber gloves in handling contaminated parts.
NOTE
Cleaning operations must be performed by
a journeyman, refrigeration mechanic, or air
conditioning technician.
1. Turn off power to unit at the main power
disconnect switch.
2. Remove the old compressor and install the new
compressor.
3. Remove the liquid line drier and install an
oversized liquid line fi lter-drier (one size larger
than the normal selection size).
4. Evacuate the system according to standard
procedures. Normally, this will include the use of
a high-vacuum pump and a low-vacuum micron
gauge for measuring the vacuum obtained.
5. Recharge the system.
6. Turn on the power at the main power disconnect
switch and start the system.
4.3.4.3 Burn-Out/Acidic Cleanup Procedure
NOTE
Cleaning operations must be performed by
a journeyman, refrigeration mechanic, or air
conditioning technician.
1. These systems should be cleaned using the suc-
tion line fi lter-drier method.
2. Turn off power to the unit at the main power
disconnect switch.
3. Remove the burned-out compressor and install
the new compressor.
4. Install a suction line fi lter-drier designed for acid
removal.
5. Remove the liquid line drier and install an
oversized liquid line fi lter-drier (one size larger
than the normal selection size).
6. Check the expansion valve, sight glass and other
controls to see if cleaning or replacement is
required.
7. Evacuate the system according to standard
procedures. Normally, this will include the use of
a high-vacuum pump and a low-vacuum micron
gauge for measuring the vacuum obtained.
8. Recharge the system through the access valve
on the suction line fi lter-drier.
9. Turn on power at the main power disconnect
switch and start the system.
10. The permanently installed suction line fi lter-drier
permits small-system cleanup to be completed
in one service call. The pressure drop across the
suction line fi lter-drier should be measured during
the fi rst hour of operation. If the pressure drop
becomes excessive, the suction line fi lter-drier
should be replaced (See Sporlan Bulletin 40-10,
for the maximum recommended pressure drop
(PSI) for the suction line fi lter drier).
11. In 24 hours, take an oil sample. Observe the
color and test for acidity. If the oil is dirty or
acidic, replace the suction line fi lter-drier.
12. In 2 weeks, examine oil to determine if another
suction line fi lter-drier change is necessary.
4.3.4.4 Humidifi er Cylinder Replacement
After an extended period of operation, the yellow LED
on the humidifi er cabinet will repeatedly fl ash four
times indicating that the cylinder is completely used
and a replacement cylinder must be installed. The
cylinder is disposable and cylinder life is dependent
on water supply conditions and humidifi er usage.
Refer to the humidifi er operator’s manual supplied
under separate cover for detailed instructions on
changing the cylinder. The following procedures are
to be followed when replacing the cylinder.
Содержание CeilAiR Series
Страница 1: ... Mar 2012 CeilAiR OHS Series Installation Operation Maintenance Manual Air Technology Systems Inc ...
Страница 54: ... Mar 2012 CeilAiR OHS Series Installation Operation Maintenance Manual Air Technology Systems Inc NOTES ...
Страница 56: ... Mar 2012 CeilAiR OHS Series Installation Operation Maintenance Manual Air Technology Systems Inc ...
Страница 58: ... Mar 2012 CeilAiR OHS Series Installation Operation Maintenance Manual Air Technology Systems Inc ...