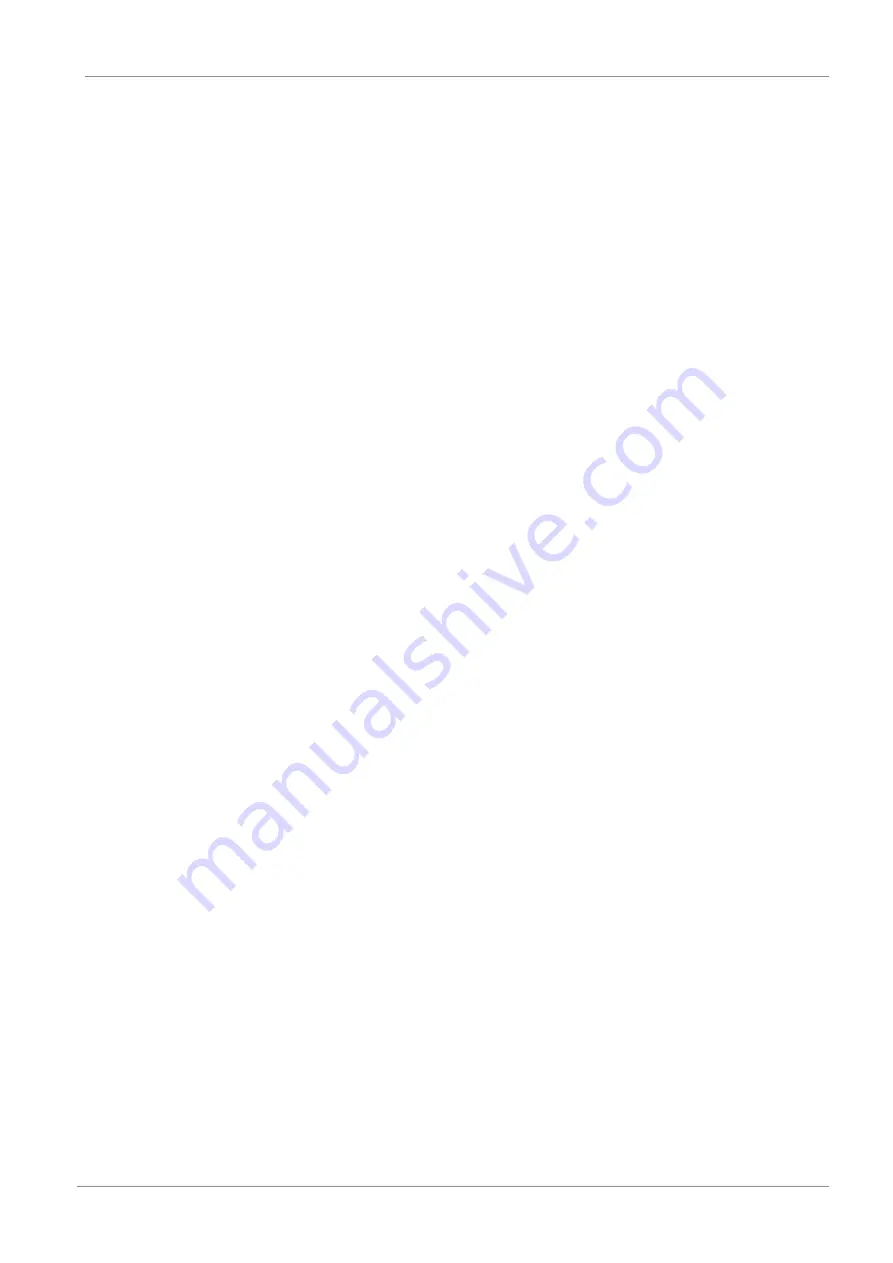
STOBER
7 | Commissioning
02/2020 | ID 443025.06
33
7.2.4
Parameterizing a SoftMotion axis
ü
You have selected the
CiA 402 HiRes Motion
application and fully configured the associated axis model in
DriveControlSuite.
1.
In the device tree, navigate to the first SoftMotion axis
SM_Drive_ETC_STOEBER_SI6_SC6_HiRes
of the first added SC6
or SI6 drive controller and double click to open it.
ð
SM_Drive_ETC_STOEBER_SI6_SC6_HiRes
tab >
General
opens in the editor window.
2.
Switch to the
Axis type and limits
area.
3.
Modulo/Finite
:
Activate your drive according to the listed options and parameterize the conditions necessary in each case.
Modulo
>
Modulo settings
: Define the modulo range by entering the associated modulo value.
Finite
>
Software limits
: If you want to put a limit on position values with a lower negative limit or upper positive limit,
enable this option and enter the associated values.
4.
Software error reaction
:
Delay
: If braking is to be done on a delay, enter the associated value.
Maximum distance
: Parameterize a maximum distance within which the drive must have reached a stop after an error
has occurred.
Set value monitoring of the drive controller is activated by default in the
CiA 402
and
CiA 402 HiRes Motion
applications. In order to prevent the drive controller from transitioning into the
excessive set value jump
state,
parameterize ramp that can realistically be implemented.
5.
Dynamic limits
(optional):
If you are using CNC or robotic functions, parameterize the associated limit values for velocity, acceleration,
deceleration and jerk.
6.
Velocity ramp type
(optional):
Using the velocity ramp type, define the velocity profile for movement-generating single axis modules and for
master/slave modules. Select the appropriate profile.
7.
Position lag supervision
(optional):
Use the associated picklist to define the response of the controller when a following error is detected.
Lag limit
: A following error is detected if the difference between the set position and actual position exceeds the lag
limit. If you have enabled position lag supervision by selecting a response, specify the associated value.
8.
Switch to the
Scaling/Mapping
vertical tab >
Scaling
area.
9.
Precision (decimal places)
:
Specify the parameterized number of decimal places in DriveControlSuite (I06 Decimal places position) for specifying
and displaying position set values, velocity values and acceleration values.
10. Repeat steps 2 – 9 for each additional SoftMotion axis in your EtherCAT system.
ð
The SoftMotion axes are parameterized.