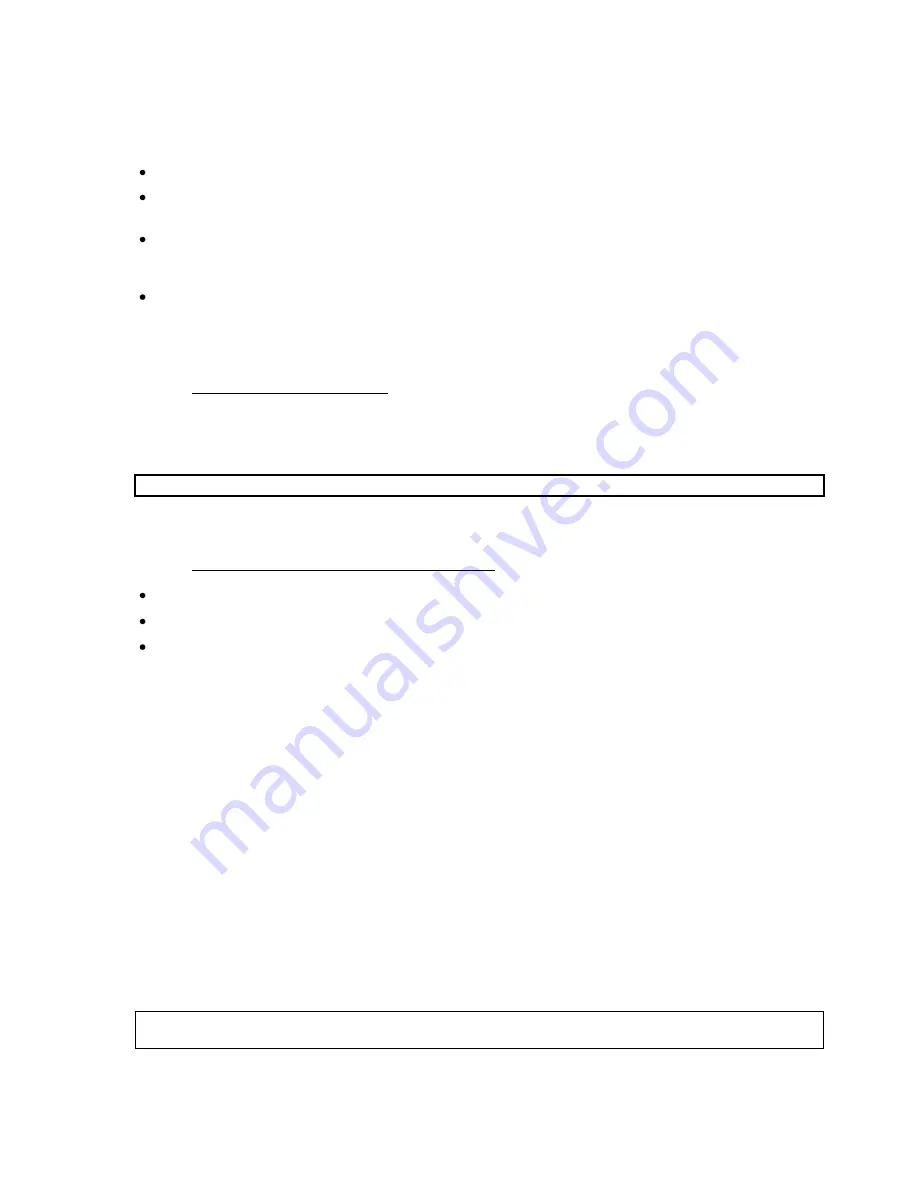
Maintenance Manual STEMME S10-VT
Date of Issue: Jan. 01, 1998
Page 7-30
Amendment Nr. 22
Date: Jan. 10, 2014
A4011121_B23.doc
Doc. No. A40-11-121
Ventilation of Hydraulic System
If the braking efficiency remains poor after mechanically adjusting, the second step is to bleed the hydraulic
system:
Before bleeding make sure that the level of the brake fluid is near “MIN”
(use DOT 4 brake fluid).
Fill a plastic syringe (approx. 300 ml) and a transparent tube (Di = 6 mm / 0.24 in.) with brake fluid and
fasten them to the nipple of the bleeder on the brake clamp.
Open the bleeder slowly using an open-
jaw spanner (width ¼‘‘).
Inject the brake fluid into the system with
the help of the syringe. Brake fluid and air are discharged from the system into the reserve container in
the process. Close the air bleeder.
Repeat the process until only brake fluid is discharged. Carry out the bleeding on both wheels one after
the other. Make sure that the excess brake fluid is sucked out of the reserve container.
The same procedure must be applied in the case of brake fluid replacement.
7.5.1.6 Replacement of brake linings
The linings must be replaced at the latest shortly before the attachment rivets are exposed. The wheel brake
callipers are provided with brake pads to the right and to the left side of the brake disc.
For replacement of the brake pads, the brake callipers can be removed by undoing of both 1/4" screws.
CAUTION:
Do not actuate the brake now.
The pads with the riveted brake lining can now be replaced by new ones.
7.5.1.7 Removal and installation of landing gear legs
Loosen all attachments to the frame.
Remove locking screws in front of the main bearings.
Push the bearing bolts out to the front and to the rear, respectively.
Installation is carried out in the reverse order.
7.5.2 Tailwheel
Description:
See section 3.5.2
Lubrication:
See section 6.5
Support tail cone to check tail wheel. Fully deflect rudder pedals left and right and check clearance between
wheel and fuselage structure (and additionally fairing, if applicable) and ease of operation. Check condition of
fork (cracks, corrosion, deformation).
Check condition of tire and observe the slip mark. The tire wears down within a relatively short time, since
during manoeuvring on the ground, the high inertia moment of the wing span of 23 m / 75.5 ft. counteracts
the steering force.
Inflation Pressure of Tail Wheel Wires:
2.8 ± 0.2 bar / 41 ± 3 p.s.i
Check friction damping of tailwheel: If pushed to its upper stops (under load) the fork must show a heavy
friction against turning. Check smooth steering of the fork if hanging free. Check axial and radial backlash of
fork in its bearings (no diametrical backlash or tilting due to worn out upper bearing, sufficient clearance for
rudder control when tail is lifted). Grease lower axial bearing if required (observe section 6.5).
NOTE:
Never grease upper axial bearing of the tail wheel! The friction under load is required to prevent tail
wheel flutter.
Check condition of steering assembly coupled to rudder (springs, rods). Check rods and springs for safe
connection, specially the spring relieved, by deflecting rudder to its stops.