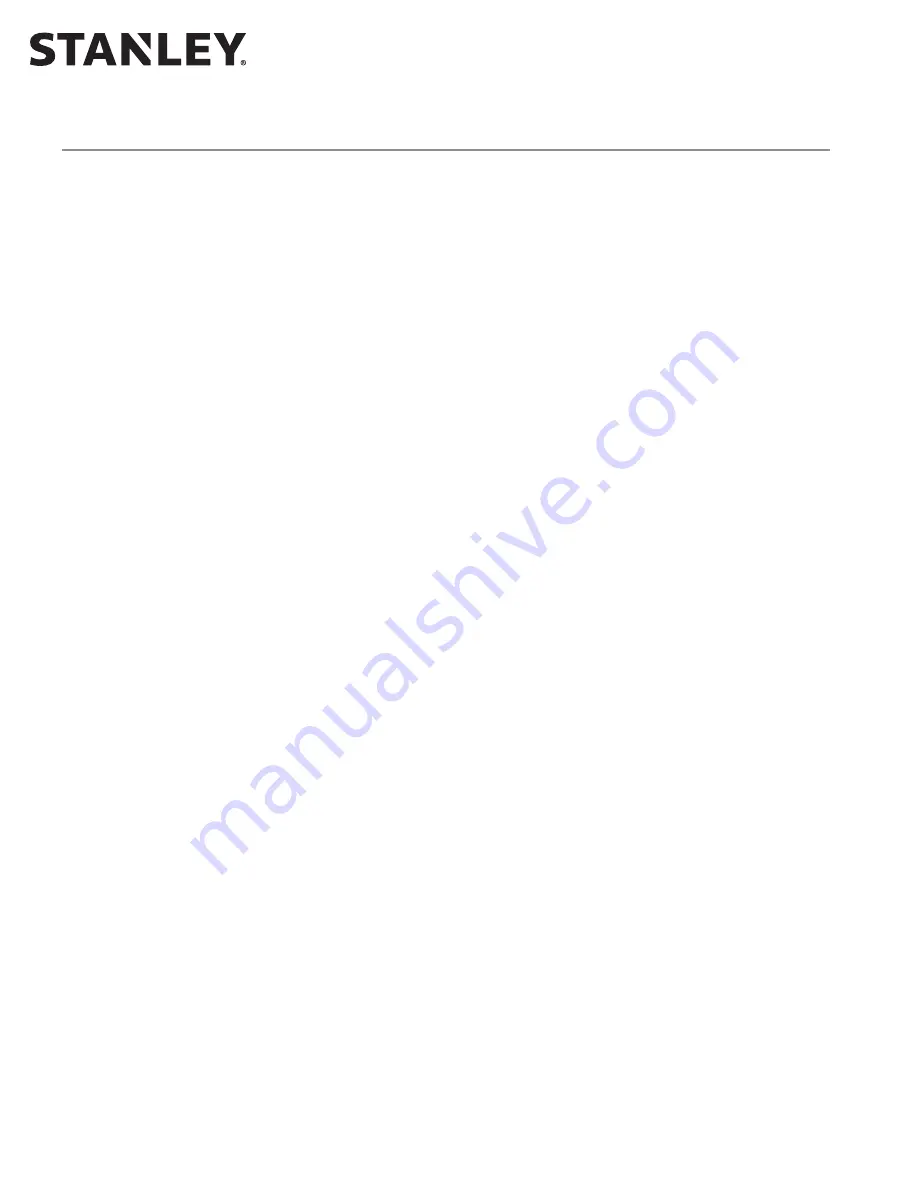
iQ Control Box
6 Document # 204144 REV B • www.stanleyaccess.com • 1.800.7.ACCESS
Cop
yr
ight 2019, S
tanley Ac
cess T
echnologies, LL
C.
All rights r
es
er
ved. R
epr
oduction
in whole or in p
ar
t without the expr
ess wr
itt
en permission o
f S
tanley is pr
ohibit
ed.
01.25.2019
Tuning In the iQ Controller Using the Controller Pushbuttons
1. To change the
INDEX
and
VALUE
:
To show the
INDEX
press and hold
ENTER
, the current
INDEX
will display. Once ENTER is released, the display
will show the
VALUE
of that
INDEX
. After 2.5 seconds, the display will return to the current status code.
2. To change the
INDEX
:
Hold
ENTER
switch while pressing
UP
or
DOWN
to get desired
INDEX
.
3. To change a
VALUE
:
a.
Unlock the keypad by setting index 99 to value 00.
b. After the desired
INDEX
is selected, release
ENTER
and
within 2.5 seconds
press
UP
or
DOWN
to get the
desired VALUE. (If the
UP
or
DOWN
buttons are not pressed within 2.5 seconds of releasing the
ENTER
button, the display will change from the
VALUE
back to the
STATUS
.)
4. To display
STATUS CODE
:
A few seconds after the
VALUE
is selected, the display indicates the
STATUS CODE
.
5. Refer to Tables 2 and 3 for a list of index setting descriptions and values. Read the descriptions entirely
before performing each step. Check the
INDEX
and
VALUE
after each step.
6. To
STORE CHANGES
in permanent memory:
Cycling door open one time will store changes.
7. To
LOCK
keypad:
Lock keypad by setting index
99
to value
01
or by turning power
OFF
and then
ON
.
8. To
ACCESS
the door cycle counter function:
a.
Ensure
that the keypad is locked by setting index 99 to 01.
b.
Ensure
that the index is set to any index but 99.
c.
Press
the up or down key to access the door cycle counter.
The display will show “
dc
” followed by four pairs of digits, followed by “
dc
”.
Example
: If the Door Count was
12345678
cycles the controller will display “
dc
” “
12
” “
34
” “
56
” “
78
” “
dc
”.