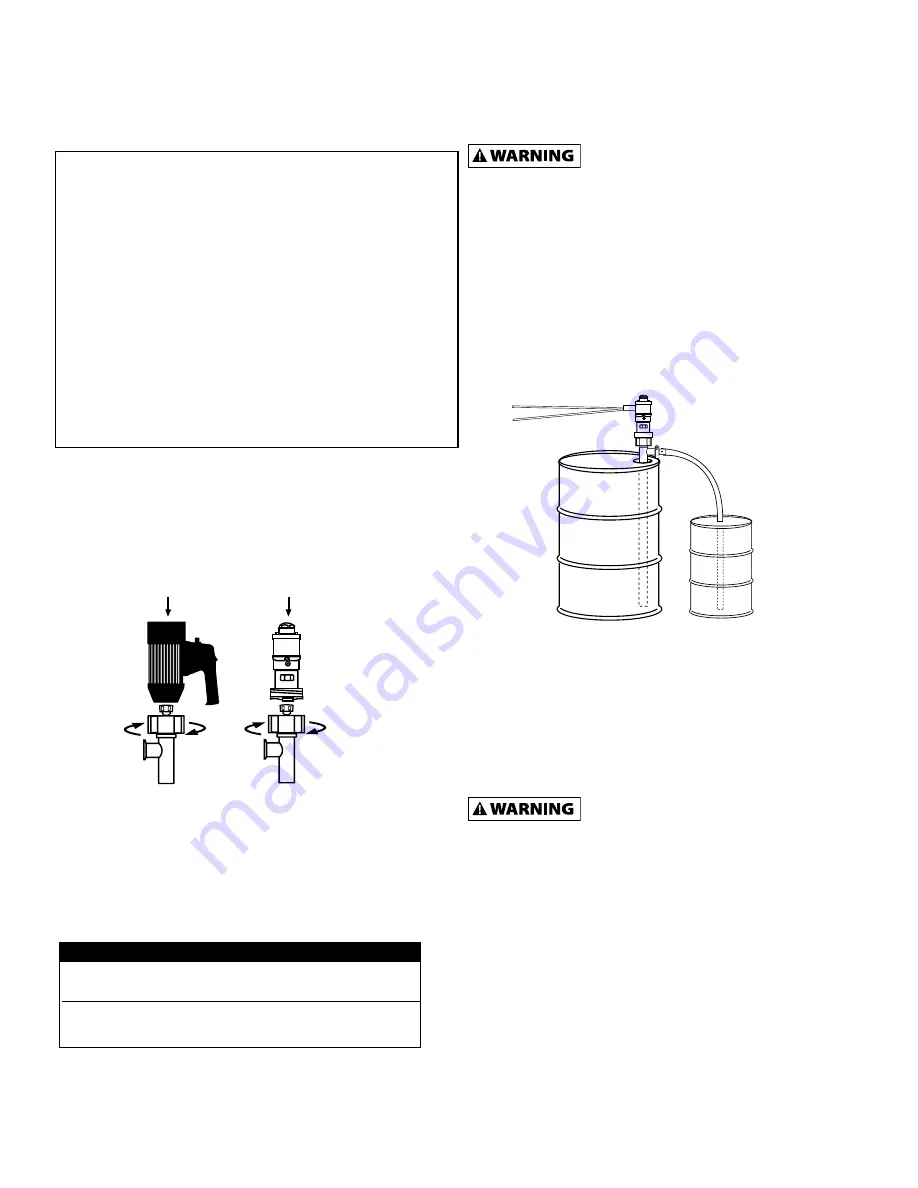
6
Standard Pump Operating Instructions and Parts Manual (OIPMS0611)
Assembly
1
. Remove the pump and motor from packaging.
2 . Inspect all contents for damage .
3. Couple the motor to the pump tube by using the Hex Nut
(see Figure 1) .
4. First pump clean water in order to familiarize yourself with
the pump’s operation, flow rate, discharge pressure and
motor speed .
5. It is recommended to thoroughly clean and sanitize models
SP-8800 & SP-8900 before operation.
Do not use these pumps for the transfer of
flammable or combustible products or in an
environment where flammable or combustible fumes are present
unless used in conjunction with an Explosion Proof Motor or
SP-A1FP / SP-A2 Series air motor. Please contact the factory or
authorized distributor with any questions regarding this matter
(see page 24).
General Operation Guide (SP-8800 & SP-8900)
1
. Use closed top drum or other cover to avoid possible
contamination .
2. Once the pump is fully cleaned, assembled and all
connections are securely fastened, insert the pump into the
drum or tank .
3. It is recommended to attach a suitable hose or pipe to the
pump discharge.
4. If you opt to use a hose, fasten the hose to the hose
barb with a suitable hose clamp that exceeds the pump
discharge pressure.
Make sure the hose meets the pump
discharge pressure requirements (SP-8800
= 16 psi (1,1 bar)) / (SP-8900 = 32 psi (2,2 bar). It is
recommended to use a hose that is rated 4 x the pump
discharge pressure. Ex: 32 x 4 = 128 psi (9 bar).
5. Turn the motor to the “ON” position.
6. After use, clean the pump and store vertically.
Disassembly / Cleaning Procedures
(SP-8800 & SP-8900)
1. In order to clean a majority of the residue from the pump
tube, immerse the pump into a 55 Gallon Drum of water
or a non-flammable, food safe cleaning agent. Allow the
pump to circulate the water for 3 minutes.
2. For a more thorough cleaning remove the motor from the
pump tube by loosening the connection nut (P/N: 8842)
(see Figure 2) .
SP-8800 & SP-8900 SERIES
Note:
Flow rates are based on water. As viscosity increases, the flow
rate will decrease .
Specifications
Models SP-8800 & SP-8900
Maximum Liquid
Temperature . . . . . . . . . . . . . . . . . . . .175º
F (79
º C)
Pump Type . . . . . . . . . . . . . . . . . . . . . . .Centrifugal
Pump Speed . . . . . . . . . . . . . . . . . . . . .10,000 RPM
Max. Flow Rate
SP-8800
. . . . . . . . . . . . . . . . . . 32 GPM (121 LPM)
SP-8900
. . . . . . . . . . . . . . . . . . . . 15 GPM (57 LPM)
Max. Discharge Pressure SP-8800
. . . . . . . . . . . . . . . . . . . . . . . . 16 psi (1,1 bar)
SP-8900
. . . . . . . . . . . . . . . . . . . . . . . . 32 psi (2,2 bar)
Wetted Materials . . . . . . . . . . . .SS 316, Buna & Teflon
Immersion Length
. . . . . . . . . . .47" (1200 mm) (Tanks)
39
" (1000 mm) (Drums & Barrels)
Discharge Port
. . . . . . . . . . . . . . . . . . . .1 .0"
(25mm) Hose Barb &
1 .5" (38 mm) Tri-Clamp
Motors . . . . . . . . . . . . . . . . . . . . . . . . . . . . .SP-280P Series, SP-ENC Series,
SP-A1FP, SP-A2 Series
Electric
Air
Figure 1
Model
Air Connection
Consumption
SP-A1FP
.125" (3,2 mm)
28 CFM @ 90 psi
13 .2 L/sec @ 6,2 bar
SP-A2L
.25" (6,3 mm)
28 CFM @ 90 psi
SP-A2
13 .2 L/sec @ 6,2 bar
Note:
For optimum performance make sure proper size air
lines are installed .
Air Line
Air Exhaust
Note:
Recommend plumbing discharge air away from drum or
tank to prevent possible contamination . Left port is air intake,
right port is air exhaust.