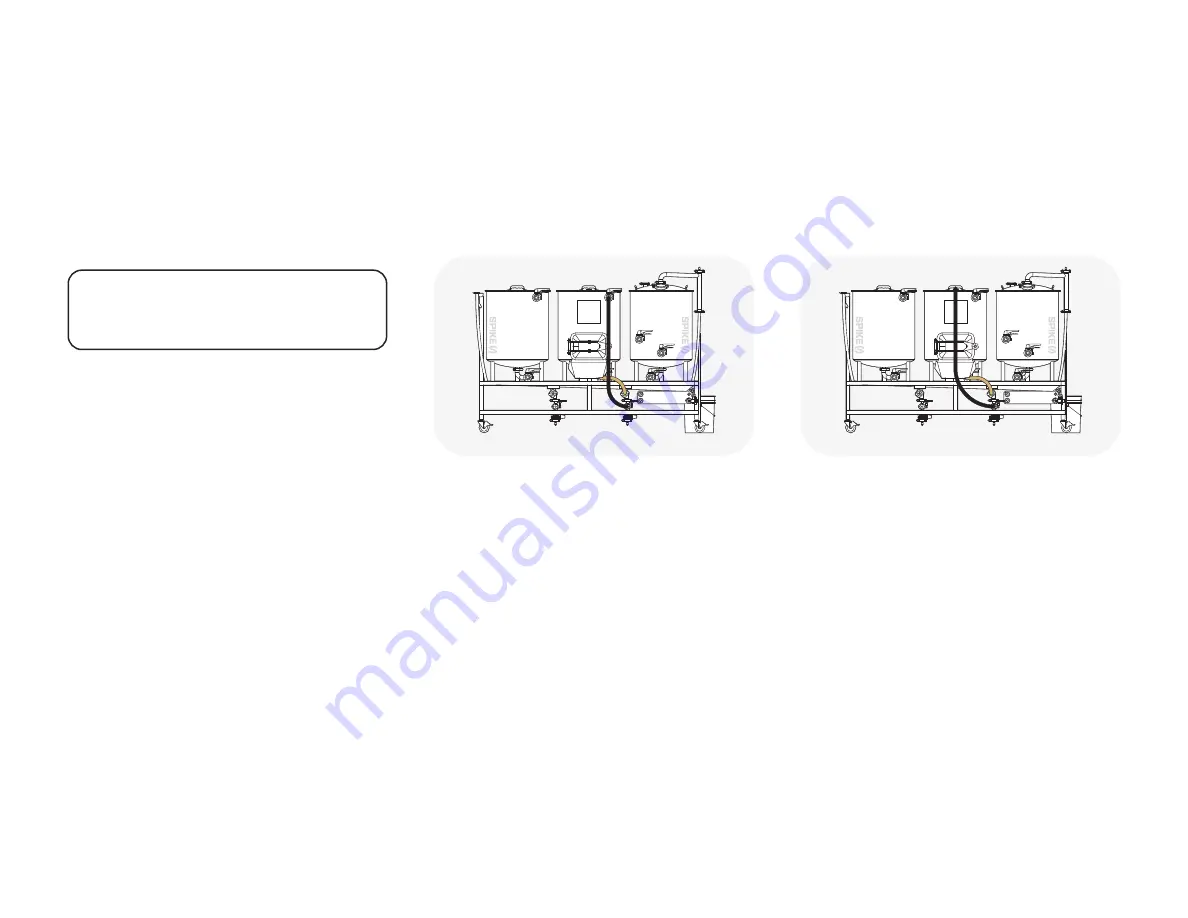
S P I K E N A N O U S E R G U I D E
30
Brew Day –
Cleaning
1.
Before CIP (Clean In Place), we recommend
opening the bottom drain on each of the three
kettles, and rinsing all loose material (hops, malt,
etc) onto the drip tray. Also, remove the false
bottom and scrub the kettle walls in the MT and
BK with a soft brush.
2.
Backflush the wort chiller by pumping hot water
through it in the opposite direction. Send the
water into the “Wort Out” port and out through the
“Wort In” port then into a drain.
3.
Your MT will have hot reclaimed water from the
knockout stage; 10 gallons of reclaimed water will
be enough. The water should be roughly 150F,
which is the heat recommended for most caustic
cleaning chemicals. If the water is below 150F,
use the MCS heater to raise it. You can add your
caustic to the MT as prescribed by the caustic
instructions.
4.
Move the hose (
Gold
) from the heat exchanger
‘Water Out’ to the wort pump inlet. (see
Figure 8
)
5.
Move the hose (
Black
) from the wort pump inlet
to the wort pump outlet. Move the other end from
the BK racking port to the top port on the MT. (see
Figure 8
)
Follow these steps to speed through the cleanup process and keep
your equipment running smoothly for your next Brew Day.
6.
Attach the vorlauf arm to the inside of the MT and
turn the wort pump on. Let this run for a minute or
until the plate and tube have been cleaned.
7.
Turn the wort pump off.
8.
Close the 3-piece valve and open the
bottom bleed valve. This will ensure the
bleed system is cleaned.
9.
3 piece valves are great at giving precise
flow control but they are a little harder to
clean. Turn the pump on, open and close the
3 piece valve slowly to make sure the ball
and seats are cleaned thoroughly.
10.
Turn off the pump and attach the CIP ball to the flat
lid with the 1.5” TC port. Add this lid to the MT.
11.
Move the hose (
Black
) from the top port on the MT
to the CIP ball. (see
Figure 9
)
Figure 8
Figure 9
12.
Turn the wort pump on and let the CIP ball
clean the inside of the tank for about 5
minutes. Turn the wort pump off and inspect
inside for any areas that didn’t get cleaned.
If there are areas that are still dirty a quick
hand scrub with a brush or more time with
the CIP ball might be needed.
13.
Once the MT is cleaned move all the liquid from the
MT to the BK.
14.
Move the hose (
Black
) from the top CIP ball port to
the bottom drain of the BK. (see
Figure 10
on next
page)
15.
Turn on the wort pump until all the liquid is drained
from the MT.
Continued on next page.
PRO TIP:
Since the HLT and water pump
are only used for clean water, they do not
need to be cleaned after brewing.