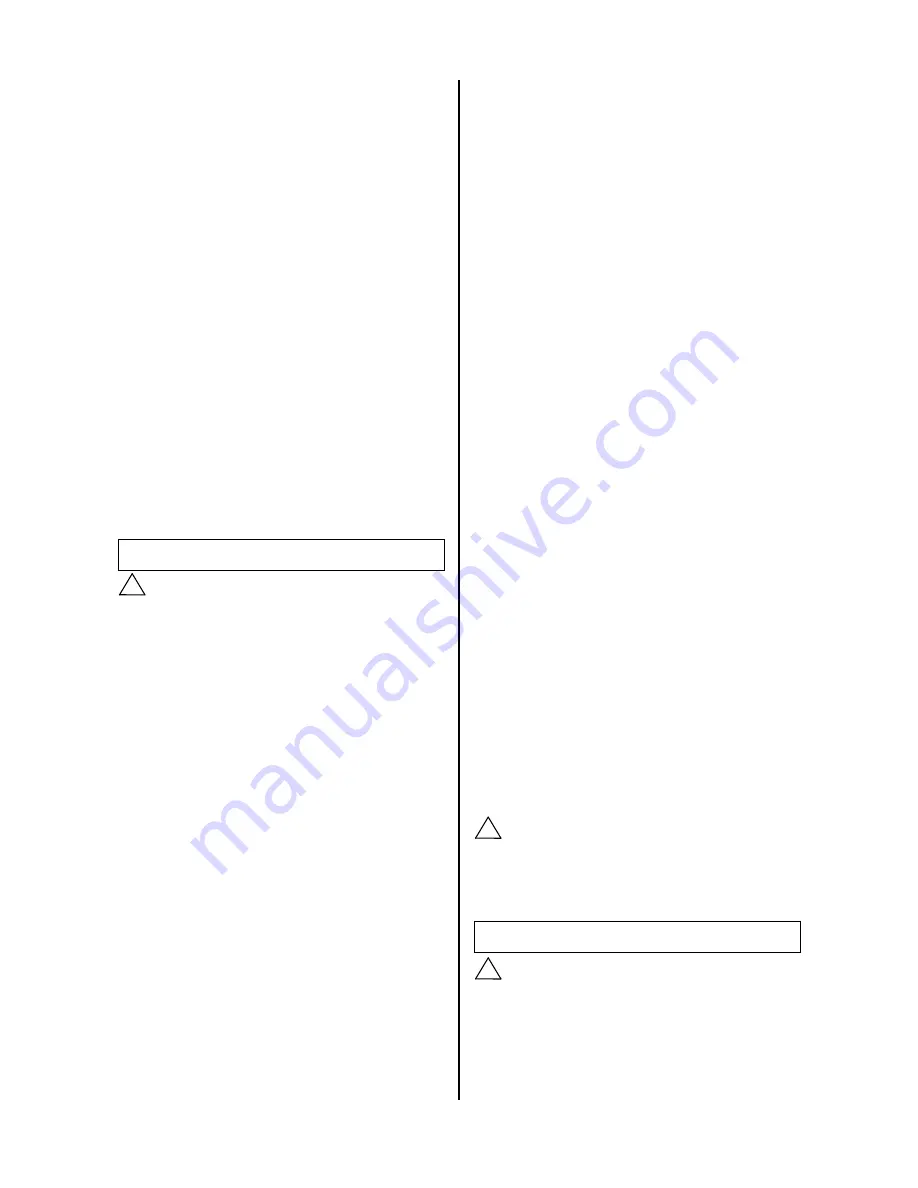
3
8. Consider emergency stops.
Design the machinery so that human injury
and/or damage to machinery and equipment will
not be caused when machinery is stopped by a
safety device under abnormal conditions, a
power outage or a manual emergency stop.
9. Consider actions when operation is restarted
after an emergency stop or abnormal stop.
Design the machinery so that human injury or
equipment damage will not occur upon restart of
operation. When the cylinder is required to return
to the initial position, provide the equipment with
a safe override.
10.
Construct the machinery so that moving
objects and the moving parts of the cylinder
with brake do not come into direct contact with
the human body.
11.
Use a balanced circuit in which lurching of the
cylinder is prevented. When operation is locked
in specified intermediate positions of the stroke,
and air pressure is applied to only one side of
the cylinder, the piston will lurch when the lock
is released. This might cause injury or damage
to machinery.
Selection
Warning
1. Confirm the specifications.
The product in this manual is designed to be
used only in industrial compressed air system.
The product should not be used with pressures
or temperatures outside the range of the
specifications, as this may cause damage or
malfunction, etc.
2. Intermediate stop
When cylinder piston is stopped intermediately
by 3-position closed center type of directional
control valve, intermediate stop positions may
not be as precise and exact as hydraulic
operation due to compressibility of air. Valves
and cylinders are not guaranteed for zero air
leakage, and stop position may not be held in a
long period of time. Consult SMC for long term
holding of stop positions.
3.
When a cylinder is in a no-load and locked state,
the holding force (maximum static load) is the
lock
’s ability to hold a static load that does not
involve vibrations or shocks. To ensure braking
force, the maximum load must be set as described
below.
①
For constant static loads, such as for drop
prevention:
35% or less of holding force (Maximum static
load)
Note) For applications such as drop prevention,
consider situations in which the air source
is shut off, and make selections based on
the holding force of the spring locked
state. Do not use the pneumatic lock for
drop prevention purposes.
②
When kinetic energy acts upon the cylinder,
such as when effecting an intermediate stop,
there are constraints in terms of the allowable
kinetic energy that can be applied to the
cylinder in a locked state. Refer to the
allowable kinetic energy of the respective
series. Furthermore, during locking, the
mechanism must sustain the thrust of the
cylinder itself, in addition to absorbing the
kinetic energy. Therefore, even within a given
allowable kinetic energy level, there is an
upper limit to the amount of the load that can
be sustained.
- Maximum load for horizontal mounting: 70%
or less of the holding force (Maximum static
load) for spring lock
- Maximum load for vertical mounting: 35% or
less of the holding force (Maximum static
load) for spring lock
③
In a locked state, do not apply impact, strong
vibrations or rotational forces. Any impact,
strong vibrations or rotational forces from
external sources could damage or shorten
the life of the lock unit.
④
Although the cylinder can be locked in both
directions, be aware that its holding force is
smaller in one of the directions. Holding
force at piston rod extended side is approx.
15% less.
Caution
1. Mount speed controller and adjust cylinder
operation speed gradually from low speed to
a desired speed.
Air Supply
Warning
1. Do not use the product out of the specified
ranges for pressure and temperature to
pre-vent equipment damage and
mal-function.
!
!
!
Содержание CE2
Страница 14: ...2 2 System Configuration...
Страница 20: ...5 External Dimension Drawing 5 1 Monosashi kun with Brake...
Страница 21: ......
Страница 22: ...5 2 Controller...
Страница 23: ...5 3 Extension Cable...
Страница 27: ...7 3 Input Signal Wiring 7 3 1 Input Signal Wiring Diagram...