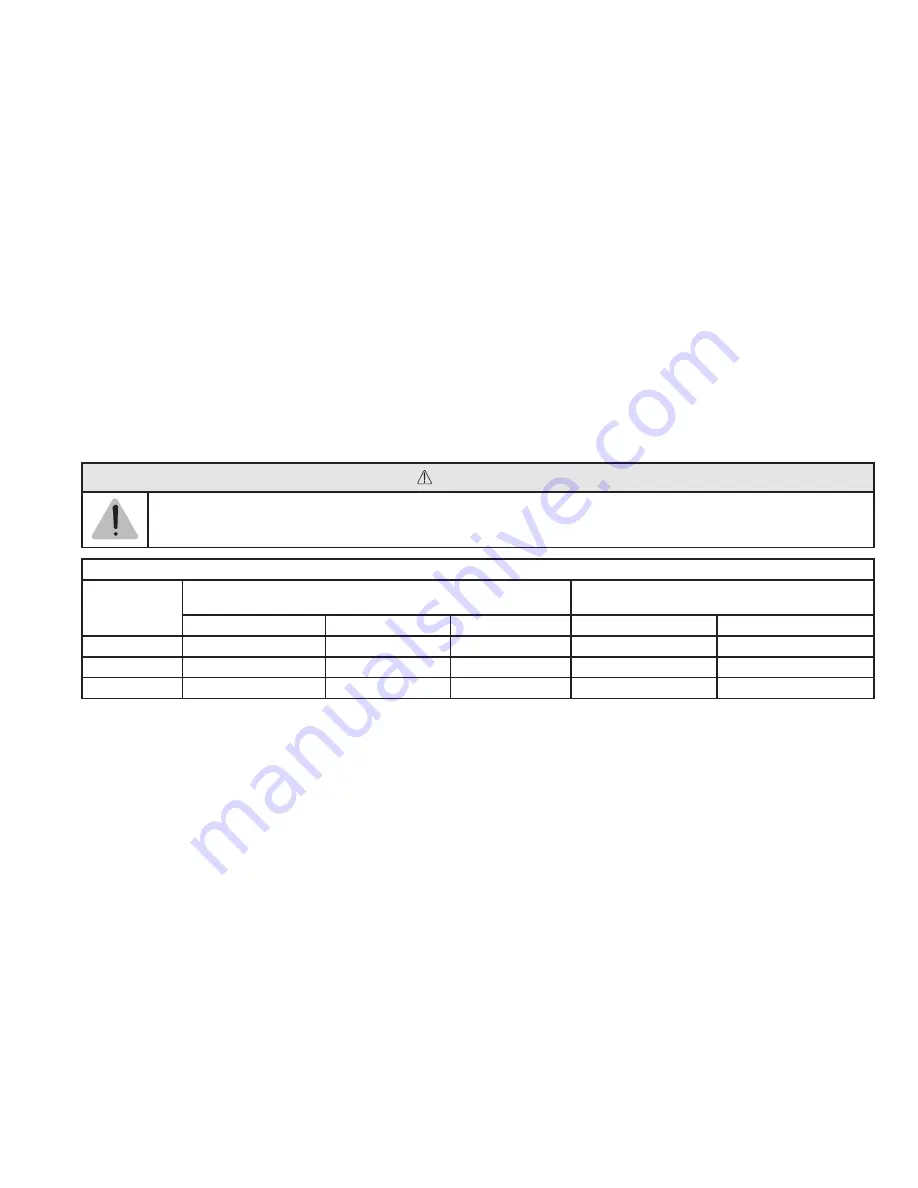
4
ZCE831
Date 2019May7/D
LUBRICATION
For maximum performance and tool life, an air line lubricator, set to deliver 4 drops per minute, is recommended. SIOUX No. 288 Air Motor Oil is
recommended.
If an airline lubrication is not used, it is recommended that the tool be oiled daily before use to improve performance. Add air motor oil and run the tool
for 10-20 seconds to distribute oil through the tool.
MAINTENANCE
Water, dust and other airline contaminants can cause rust and vane sticking. For long periods between tool use, flush the tool with 5 ml of oil and run for
10 seconds. This will help remove contaminants and reduce the formation of rust.
DISMANTLING & ASSEMBLY INSTRUCTIONS
Disconnect tool from air supply. Remove Cap Screws (9B) from Motor Housing (30) using a screw driver. Remove Steel Housing (44), while taking
care to capture the oil from the assembly. Remove Anvil (37 or 38) and Pins (36) from the front of the Frame (34), and then remove the Twin Hammers
(35) from the side of the Frame. Remove Cap Screws (9A) from Motor Housing to remove Throttle Handle (8) from Motor Housing. Remove Exhaust
Deflector (31) by removing Tapping Screws (32). Once these items are removed from the Motor Housing, heat the remaining Motor Housing
components until the assembly is hot to the touch. With the assembly still warm, press the Rotor (23) and Rear Plate (22) from the Motor Housing, then
press the Cylinder (25) from the Motor Housing. Remove the Hose Adapter (1) from the Throttle Handle using a wrench and remove the Throttle Spring
(4), Valve Ball (5), and Valve Pin (6) from the Throttle Handle using long nose pliers. Using a hammer and a punch, remove Spring Pin (10) and remove
Inside Trigger (12). Remove Screw (15) with a screw driver and remove Spring (14) and Steel Ball (13) from the detent hole in the Throttle Handle.
Remove Cap Screw (20) using a hex wrench and remove Reverse Lever (19). With these removed, remove Reverse Regulator (18) through the front of
the Throttle Handle.
REASSEMBLY
Clean and examine all parts for wear and replace any parts with parts obtained from manufacturer or authorized distributor. All parts must be dry. Check
that all bearings run smoothly. Before installing Cylinder (25) into Motor Housing (30) preheat the motor housing until the Motor Housing is hot to the touch
before press fitting together. When installing the Rear Plate (22) onto the Rotor (23), press equally on the inner and outer bearing races. Ensure a final
gap of 0.0010” to 0.0015” between the Rear Plate and Rotor. When reinstalling Twin Hammers (35) ensure that they are installed as mirror images; counter
bores facing each other and chamfers on the outside. Reassemble remaining tool parts in reverse order following the threadlocker schedule in the table.
Refill impact assembly with 60 mL of suitable impact oil. Connect tool to a suitable air supply (90 psi preferred) and run tool slowly for 5 seconds to allow
the oil to circulate
WARNING
Disconnect tool from air supply before performing any adjustment, maintenance, or repair.
NOISE AND VIBRATION READINGS
Catalog
Number
Noise (Tested in accordance with ISO Standard 15744)
Vibration (Tested in accordance with
ISO Standard 28927-1:2009)
Sound Pressure (dBA)
Sound Power (dBA)
Uncertainty (dBA)
Vibration m/s
2
Uncertainty m/s
2
IW1000MP-8H
102.7
108.1
3.0
12.4
1.99
IW1000MP-8H5
TBD
TBD
TBD
TBD
TBD
IW1000MP-8H8
98.9
110.5
3.0
6.93
0.38