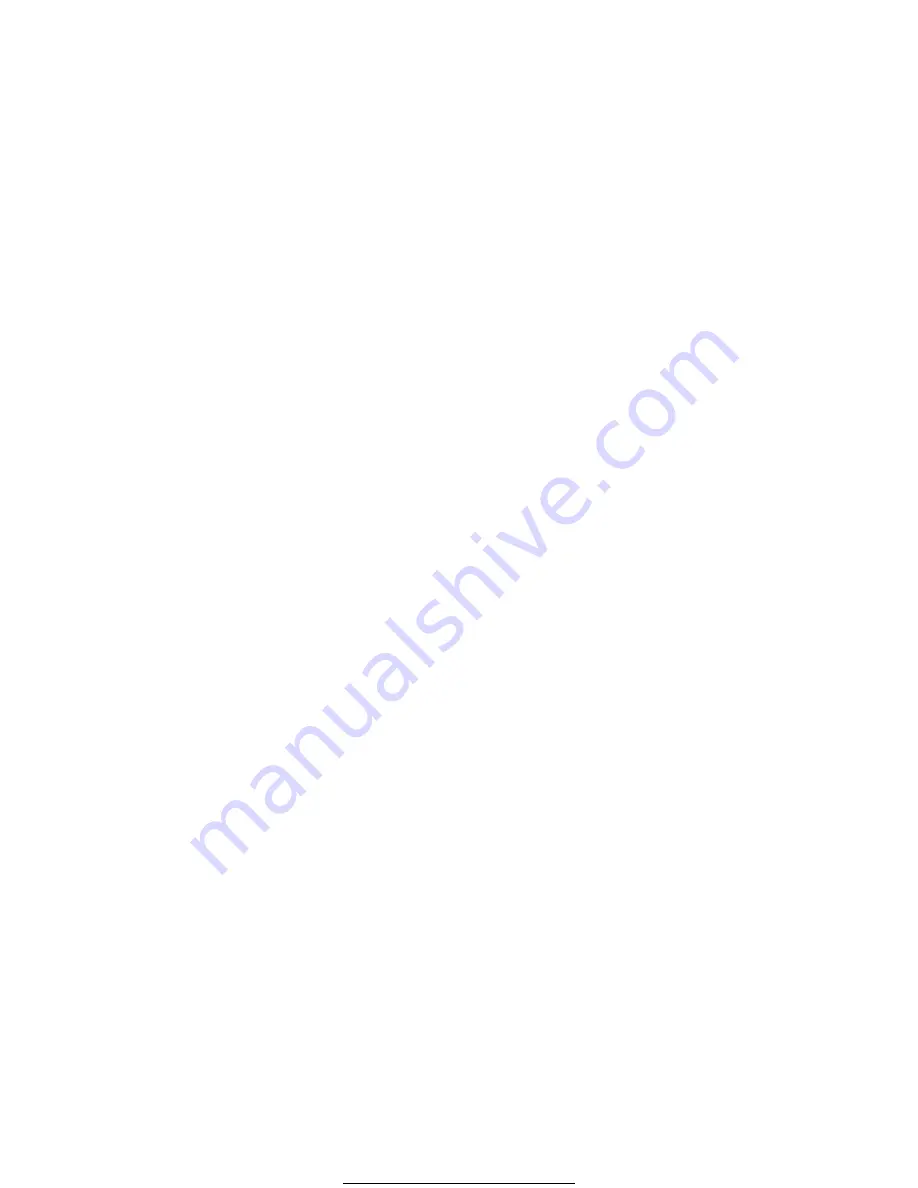
7
MOISTURE
Moisture is always present in air lines due to condensation within the lines as the air cools. Steps
must be taken to remove this moisture and to keep it from the air tool. This is because water tends
to wash away lubricants and cause corrosion, sticking and failure of internal parts.
The main line should be pitched so the far end terminates in a water leg. Branch lines are taken
from the top of the main, never off the bottom. Every branch should have a water leg at its lowest
point, with a drain cock which is drained daily.
If these precautions are taken and water is still present, an after cooler and a moisture separator
are required between the compressor and the air receiver tank. A large air line separator can be
installed in the air tool line, but precautions must be taken to insure that it will be drained daily,
before the air tool is operated.
Water in air lines is a constant threat to the proper operation of air tools. Even near
freezing operating conditions, a good refrigerant type dryer is essential. A good dryer will remove
95% or more of water right at the compressor. The remaining moisture is removed at the water leg
in the piping system or in the filter, Signode Part No. 173111. Additional information is available in
the Signode publication, "Air Supply Manual" Signode Part No. 186038. If you have any questions,
contact your local Signode Representative.
LUBRICATION
The air motor must be properly lubricated. This is achieved by keeping the air line lubricator filled
with oil and correctly adjusted. Without proper lubrication, the motor will become sticky and the
tool will give low and erratic tension and be difficult to release from the strap.
Install the lubricator as close to the air tool as possible. The arrow on the lubricator's top surface
must point in the direction of air flow.
For proper operation, oil must drop through the lubricator sight glass at a rate of 4 to 10 drops per
minute. This rate is to be checked while the air tool is running free. Only 20% of this oil is actually
delivered to the tool. The remaining oil drops back into the oil reservoir. The unit is factory set
and should require no adjustment. If an adjustment is required, the adjusting screw on top of the
lubricator may be turned as marked to reduce or increase the flow of oil.
The correct grade of oil must be used in the lubricator; too heavy an oil will not provide sufficient
lubrication and will cause sticking and sluggish operation of the air tool.
Recommended oils are any good grade of rust and oxidation inhibiting oil with a viscosity of 80-
120 S.U.S. at 100 degrees Fahrenheit. (0.15 to 0.25 cm
2
/sec. at 38 degrees Celsius), such as:
Non Fluid Oil Co., grade #LS-1236
Signode oil - Part No. 008556
If necessary, use SAE #5 or SAE #10, non-detergent, cut 1:1 with kerosene. Some oils contain
anti-wear additives which may disable the air motor. Be certain to use recommended oil.
Several drops of lubricator oil added to the inlet of the air motor or into the air line each day will
help insure good operation. A noticeable reduction of air motor performance can usually be
corrected by squirting a few drops of oil into the air line.
For Parts & Service 1-877-862-6699
WWW.TRADITIONALTOOL.COM