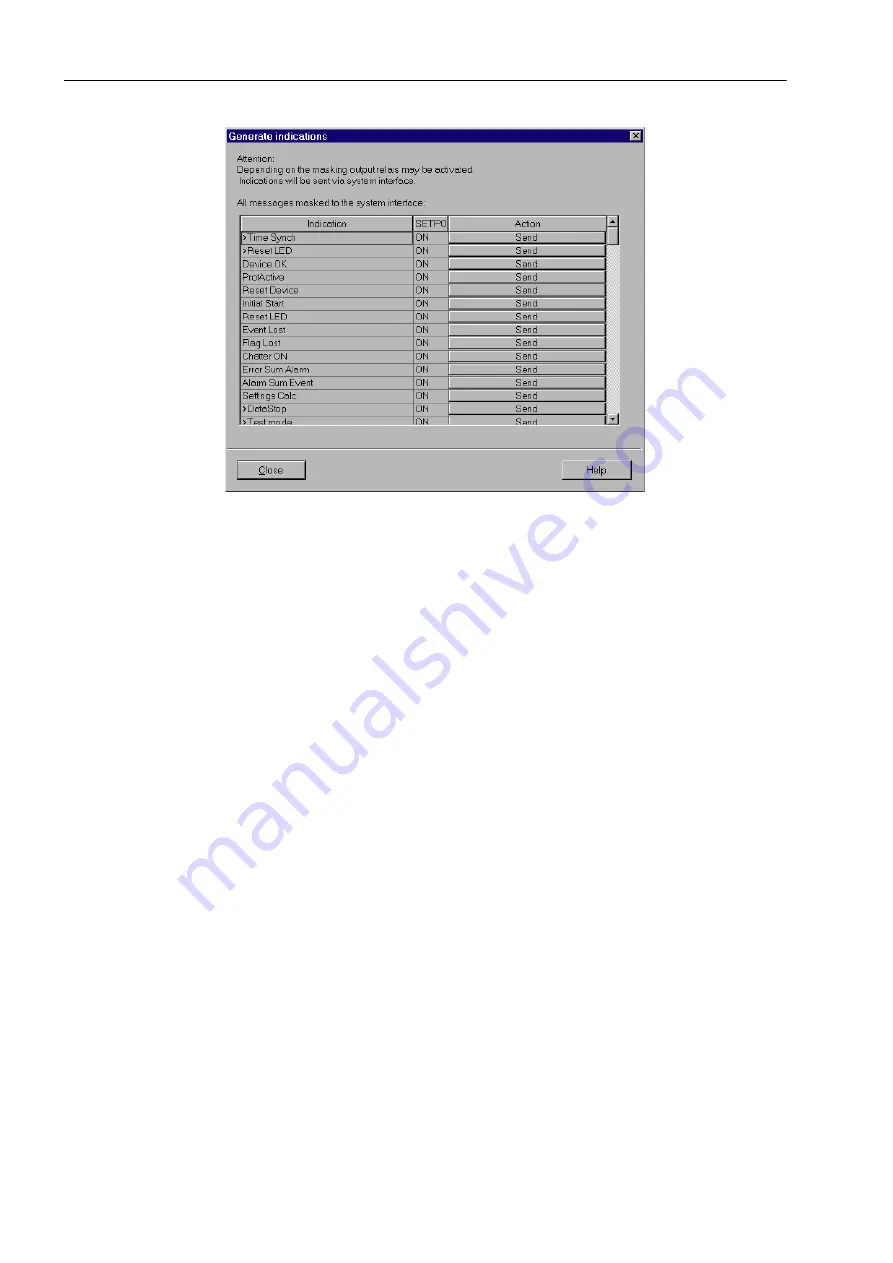
3 Installation and Commissioning
120
6MD665 Manual
C53000-G1876-C103-3
Figure 3-13
System interface test with dialog box: Generate indications — example
Changing the Oper-
ating State
Clicking for the first time on one of the field in column Action you will be asked for
password no. 6 (for hardware test menus). After you have entered the password cor-
rectly you now can send the indications individually. To do so, click on the button Send
on the corresponding line. The corresponding indication is issued and can be read out
either from the event log of the SIPROTEC
®
4 device or from the substation.
As long as the window is open, further tests can be performed.
Test in Message
Direction
For all information that is transmitted to the central station test in Status Scheduled
the desired options in the list which appears:
• Make sure that each checking process is carried out carefully without causing any
danger (see above and refer to DANGER!)
• Click on Send in the function to be tested and check whether the transmitted infor-
mation reaches the central station and shows the desired reaction. With this proce-
dure the information (beginning with ">”) which is normally coupled via binary inputs
is also transmitted to the central station. The function of the binary inputs itself is
tested separately.
Exiting the Test
Mode
To end the System Interface Test, click on Close. The device is briefly out of service
while the start-up routine is executed. The dialogue box closes.
Test in Command
Direction
The information transmitted in command direction must be indicated by the central
station. Check whether the reaction is correct.
3.3.4
Checking the Binary Inputs and Outputs
Prefacing Remarks
The binary inputs, outputs, and LEDs of a SIPROTEC
®
4 device can be individually
and precisely controlled in DIGSI
®
. This feature is used to verify control wiring from the
Содержание SIPROTEC 6MD665
Страница 8: ...Preface vi 6MD665 Manual C53000 G1876 C103 3 ...
Страница 14: ...Contents vi 6MD665 Manual C53000 G1876 C103 3 ...
Страница 140: ...3 Installation and Commissioning 126 6MD665 Manual C53000 G1876 C103 3 ...
Страница 166: ...4 Technical Data 152 6MD665 Manual C53000 G1876 C103 3 ...
Страница 201: ...A 9 Group Alarms 187 6MD665 Manual C53000 G1876 C103 3 A 9 Group Alarms No Description No Description ...
Страница 210: ...Literature 196 6MD665 Manual C53000 G1876 C103 3 ...
Страница 222: ...Index 208 6MD665 Manual C53000 G1876 C103 3 ...