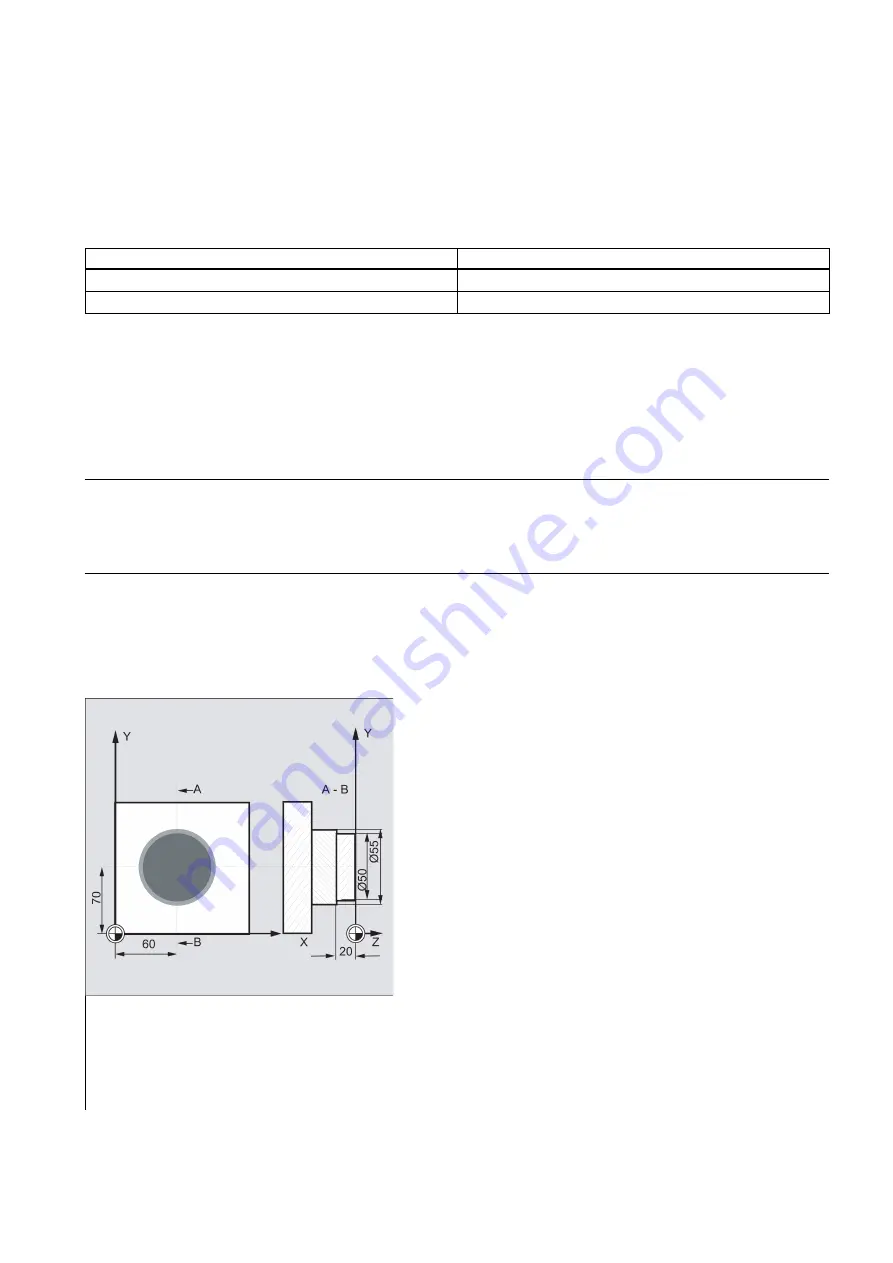
Programming and Operating Manual (Milling)
6FC5398-4DP10-0BA1, 01/2014
183
PA, PO (spigot center point)
Use the parameters PA and PO to define the reference point of the spigot.
CDIR (milling direction)
Use this parameter to specify the machining direction for the spigot. Using the parameter CDIR, the milling direction can be
programmed directly with "2 for G2" and "3 for G3", or alternatively with "synchronous milling" or "conventional milling".
Down-cut and up-cut milling are determined internally in the cycle via the direction of rotation of the spindle activated prior to
calling the cycle.
Down-cut
Up-cut
M3 → G3
M3 → G2
M4 → G2
M4 → G3
VARI (machining type)
Use the parameter VARI to define the machining type. Possible values are:
●
1=roughing
●
2=finishing
AP1 (diameter of blank spigot)
Use this parameter to define the blank dimension of the spigot (without sign). The internally calculated radius of the
approach semi-circle depends on this dimension.
Note
A tool compensation must be programmed before the cycle is called. Otherwise, the cycle is canceled and alarm 61009
"Active tool number=0" is output. Internally in the cycle, a new current workpiece coordinate system is used which influences
the actual value display. The zero point of this coordinate system is to be found in the pocket center point.
At the end of the cycle, the original coordinate system is active again.
Programming example: Circular spigot
Machining a spigot from a blank with a diameter of 55 mm and a maximum infeed of 10 mm per cut; specification of a final
machining allowance for subsequent finishing of the spigot surface. The whole machining is performed with reverse rotation.
See the following programming example for circular spigot:
N10 G90 G17 G0 S1800 M3 D1 T1
; Specification of technology values
N11 M6
N20 CYCLE77 (10, 0, 3, -20, ,50, 60, 70, 10, 0.5, 0, 900,
800, 1, 1, 55)
; Roughing cycle call
N30 D1 T2 M6
; Change tool
N40 S2400 M3
; Specification of technology values