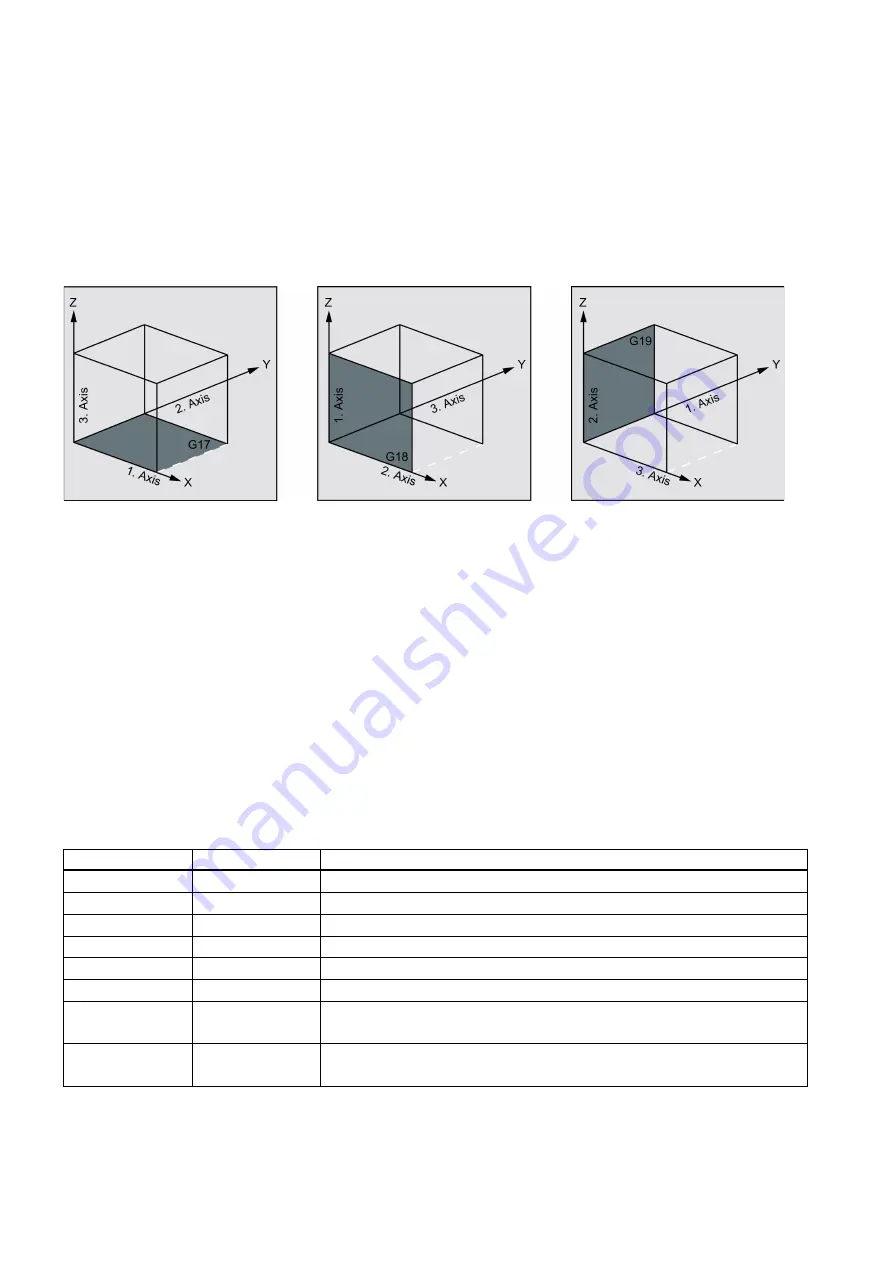
Programming and Operating Manual (Milling)
162
6FC5398-4DP10-0BA1, 01/2014
The center point coordinates for the milling pattern or the pocket to be machined are programmed in a rectangular
coordinate system.
The G functions active prior to the cycle call and the current programmable frame remain active beyond the cycle.
Plane definition
Milling cycles generally assume that the current workpiece coordinate system has been defined by selecting a plane (G17,
G18 or G19) and activating a programmable frame (if necessary). The infeed axis is always the third axis of this coordinate
system.
See the following illustration for plane and axis assignment:
Messages with regard to the machining state
During the execution of the milling cycles, various messages that refer to the machining status are displayed on the screen.
The following messages are possible:
●
"Elongated hole <No.>(first figure) being machined"
●
"Slot <No.>(other figure) being machined"
●
"Circumferential slot <No.>(last figure) being machined"
In each case, <No.> stands for the number of the figure that is currently being machined.
These message do not interrupt the program execution and continue to be displayed until the next message is displayed or
the cycle is completed.
9.6.2
Face milling - CYCLE71
Programming
CYCLE71 (_RTP, _RFP, _SDIS, _DP, _PA, _PO, _LENG, _WID, _STA, _MID, _MIDA, _FDP, _FALD, _FFP1, _VARI, _FDP1)
Parameters
Parameter
Data type
Description
_RTP
REAL
Retraction plane (absolute)
_RFP
REAL
Reference plane (absolute)
_SDIS
REAL
Safety clearance (to be added to the reference plane; enter without sign)
_DP
REAL
Depth (absolute)
_PA
REAL
Starting point (absolute), first axis of the plane
_PO
REAL
Starting point (absolute), second axis of the plane
_LENG
REAL
Rectangle length along the first axis, incremental.
The corner from which the dimension starts results from the sign.
_WID
REAL
Rectangle length along the second axis, incremental.
The corner from which the dimension starts results from the sign.