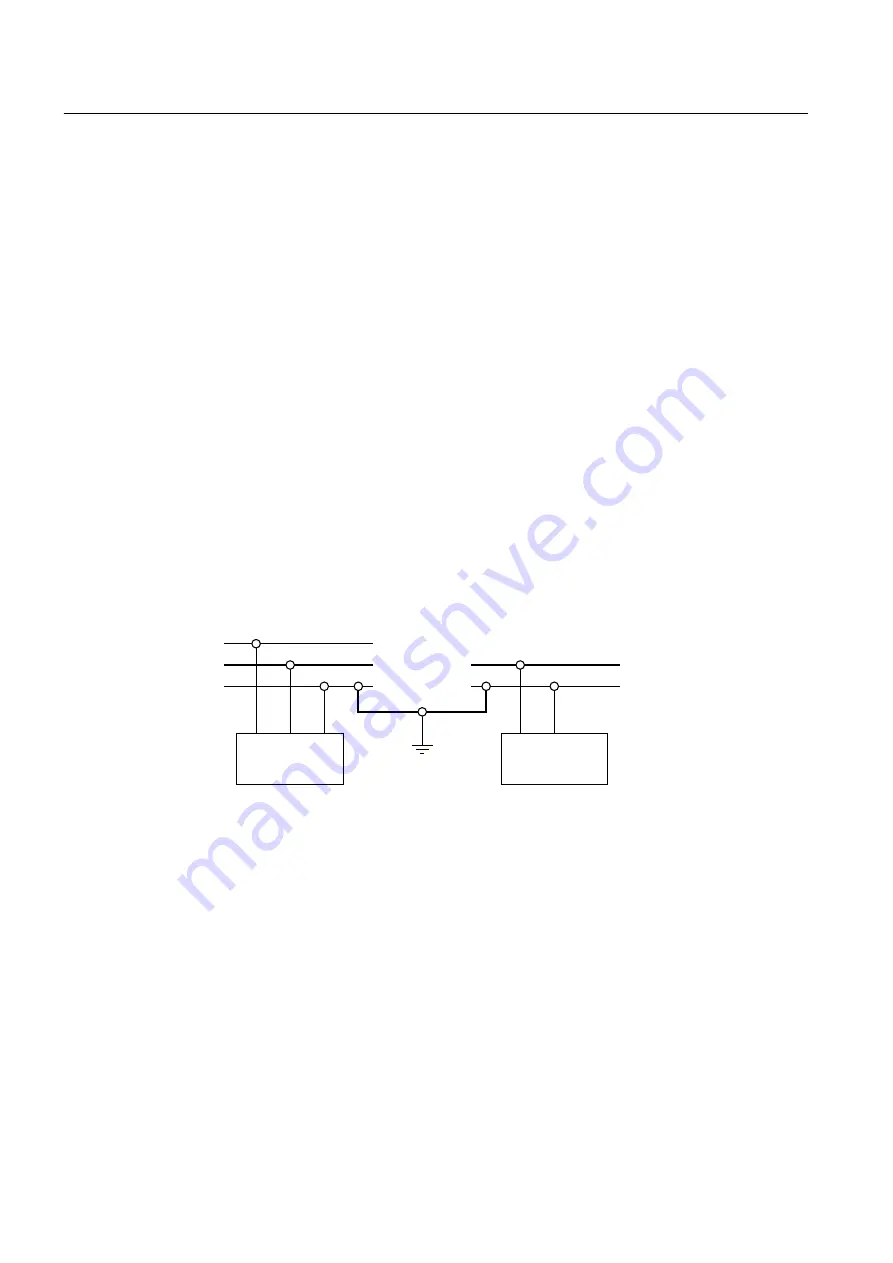
I/O connection
● Create a low-impedance ground connection for additional cabinets, system components,
and distributed devices with the largest possible cross-section (at least 16 mm²).
● Ground unused lines at one end in the cabinet.
● Choose the greatest possible clearance between the power and signal cables (at least 20
cm). The greater the distance over which the cables are routed in parallel, the greater the
clearance must be. You must install additional shields if sufficient clearance cannot be
maintained.
● Avoid unnecessarily long cable loops.
● Surge suppressors, e.g. RC elements or varistors must be connected to the operating coils
for contactors and relays in the converter.
● In order to reduce noise/interference entering or exiting via the cable, filter auxiliary voltages
in the control cabinet.
6.3
Potential concept
A noise-free connection between the internal and external supply voltage can be achieved by
connecting the 0 V potentials to each other and grounding them. This also eliminates the need
for the control circuit insulation monitor required by DIN EN 60204-1.
,QWHUQDO
ORDGV
([WHUQDO
ORDGV
3
0
3
0
1
Figure 6-3
Potential concept
Electrical connection
6.3 Potential concept
SINAMICS GM150 6SL3815-2LN41-4AA2
106
Operating Instructions 04/2017
Содержание SINAMICS GM150
Страница 2: ...20 04 2017 13 25 V27 00 ...
Страница 16: ...Table of contents SINAMICS GM150 6SL3815 2LN41 4AA2 16 Operating Instructions 04 2017 ...
Страница 18: ...Introduction 1 1 About these instructions SINAMICS GM150 6SL3815 2LN41 4AA2 18 Operating Instructions 04 2017 ...
Страница 72: ...Description 3 6 Description of options SINAMICS GM150 6SL3815 2LN41 4AA2 72 Operating Instructions 04 2017 ...
Страница 192: ...Operation 8 5 Fault and system messages SINAMICS GM150 6SL3815 2LN41 4AA2 192 Operating Instructions 04 2017 ...
Страница 228: ...Spare parts SINAMICS GM150 6SL3815 2LN41 4AA2 228 Operating Instructions 04 2017 ...
Страница 232: ...Service Support SINAMICS GM150 6SL3815 2LN41 4AA2 232 Operating Instructions 04 2017 ...
Страница 256: ...Index SINAMICS GM150 6SL3815 2LN41 4AA2 256 Operating Instructions 04 2017 ...
Страница 257: ......