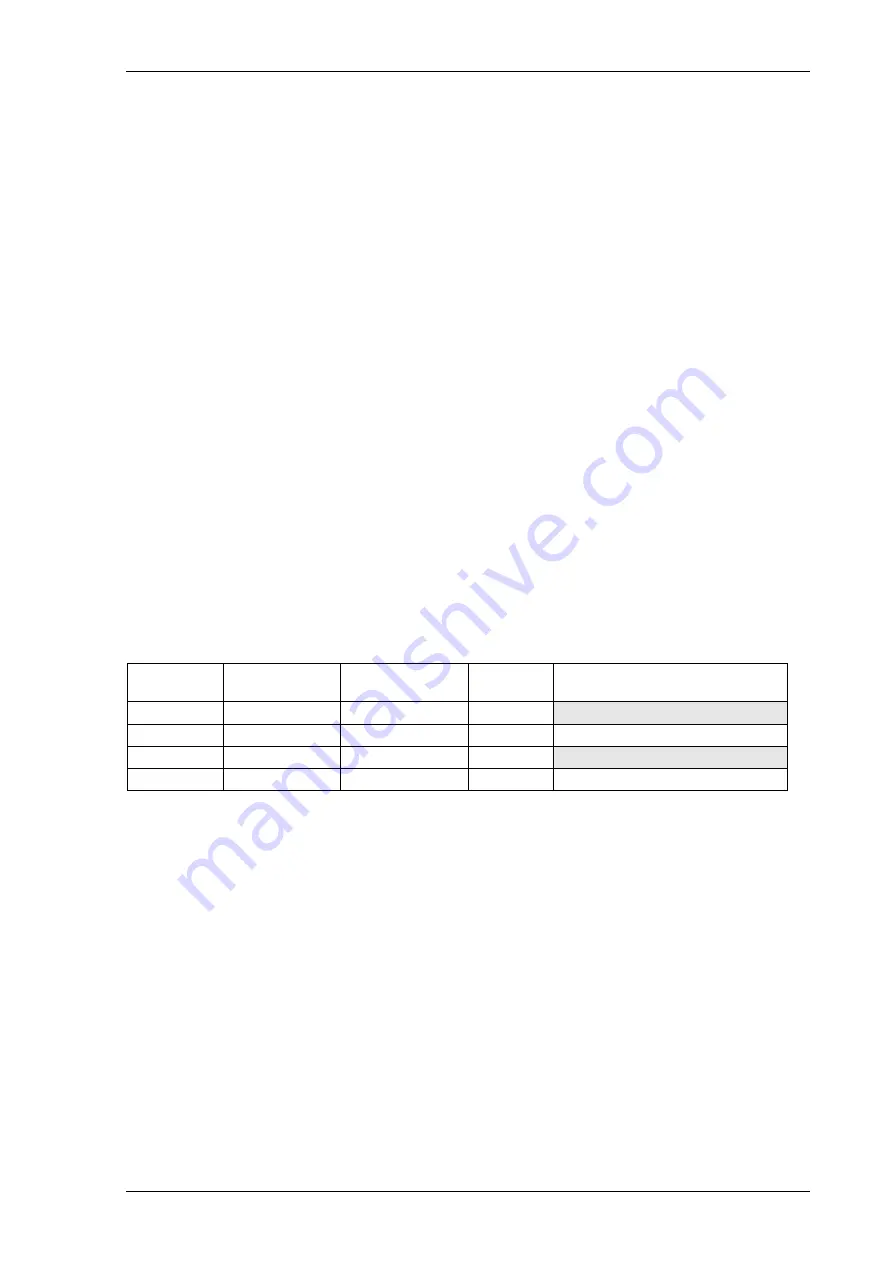
Chapter 6 - 7SR157 Commissioning and Maintenance Guide
Chapter 6 - Page 5 of 14
©2016 Siemens Protection Devices Limited
1.3.2
Secondary Injection Tests
Select the required relay configuration and settings for the application.
Isolate the auxiliary D.C. supplies for alarm and tripping from the relay and remove the trip and intertrip links.
Carry out injection tests for each relay function, as described in this document
1.3.3
Primary Injection Tests
Primary injection tests are essential to check the ratio and polarity of the transformers as well as the secondary
wiring.
1.3.4
Putting into Service
After tests have been performed satisfactorily the relay should be put back into service as follows:-
Remove all test connections.
Replace all secondary circuit fuses and links, or close miniature circuit breaker (MCB).
Ensure the Protection Healthy LED is on, steady, and that all LED indications are correct. If necessary press
CANCEL
until the Relay Identifier screen is displayed, then press
TEST/RESET
to reset the indication LEDs.
The relay meters should be checked in Instruments Mode with the relay on load.
The relay settings should be downloaded to a computer and a printout of the settings produced. The installed
settings should then be compared against the required settings supplied before testing began. Automated setting
comparison can be carried out by Reydisp using the
Compare Settings Groups
function in the
Edit
menu. Any
modified settings will be clearly highlighted.
1.4
AC Analogue Energising Quantities
Voltage measurement for each input channel is displayed in the Instrumentation Mode sub-menus. Each input
should be checked for correct connection and measurement accuracy by single phase secondary injection at
nominal levels. Ensure that the correct instrument, displays the applied signal within limits of the Performance
Specification.
Applied Sec
Volts (Vrms)
Tolerance
V Line
Secondary
Primary
Line VT Ratio:
V Bus
Secondary
Primary
Bus VT Ratio:
Note: Instrument tolerance is:
±
1 % Vn (0.1 x Vn ≤ V ≤ 1.2 x Vn).
1.5
Binary Inputs
The operation of the Binary Input(s) can be monitored on the Binary Input Meters display shown in Instruments
Mode. Apply the required voltage onto each binary input in turn and check for correct operation. Depending on the
application, each binary input may be programmed to perform a specific function. Each binary should be checked
to prove that it’s mapping and functionality is as set as part of the Scheme Operation tests.
Where the pick-up timers associated with a binary input are set for DC operation, these delays should be checked
either as part of the scheme logic or individually. To check a binary pick-up time delay, temporarily map the binary
input to an output relay that has a normally-open contact. This can be achieved in the Output Matrix sub-menu by
utilising the
BI n Operated
settings. Use an external timer to measure the interval between Binary Input
energisation and closure of the output contacts. Similarly, to measure the drop-off delay, map the Binary Input to
an output relay that has a normally-closed contact; time the interval between binary input de-energisation and
closure of the output contacts.
The timers are also used to ensure correct operation of Binary Inputs from AC voltage energisation. If a delayed
pickup is required, this must be provided by additional Quick Logic configuration. An example is shown in Chapter
7 – Applications Guide.
Содержание 7SR157 Argus
Страница 1: ...Energy Management 7SR157 Argus Check and System Synchronising Relay Reyrolle Protection Devices ...
Страница 2: ......
Страница 4: ...7SR157 Contents ...
Страница 58: ...7SR158 Technical Manual Chapter 3 Page 2 of 18 2022 Siemens Protection Devices Limited ...
Страница 76: ...7SR157 Technical Manual Chapter 4 Page 2 of 58 2016 Siemens Protection Devices Limited ...
Страница 80: ...7SR157 Technical Manual Chapter 4 Page 6 of 58 2016 Siemens Protection Devices Limited ...
Страница 92: ...7SR157 Technical Manual Chapter 4 Page 18 of 58 2016 Siemens Protection Devices Limited ...
Страница 122: ...7SR157 Technical Manual Chapter 4 Page 48 of 58 2016 Siemens Protection Devices Limited ...
Страница 124: ...7SR157 Technical Manual Chapter 4 Page 50 of 58 2016 Siemens Protection Devices Limited ...
Страница 126: ...7SR157 Technical Manual Chapter 4 Page 52 of 58 2016 Siemens Protection Devices Limited ...
Страница 150: ...7SR157 Technical Manual Chapter 5 Page 18 of 18 2018 Siemens Protection Devices Limited ...
Страница 161: ...Chapter 6 7SR157 Commissioning and Maintenance Guide Chapter 6 Page 11 of 14 2016 Siemens Protection Devices Limited ...
Страница 179: ...Siemens Protection Devices 1 ...