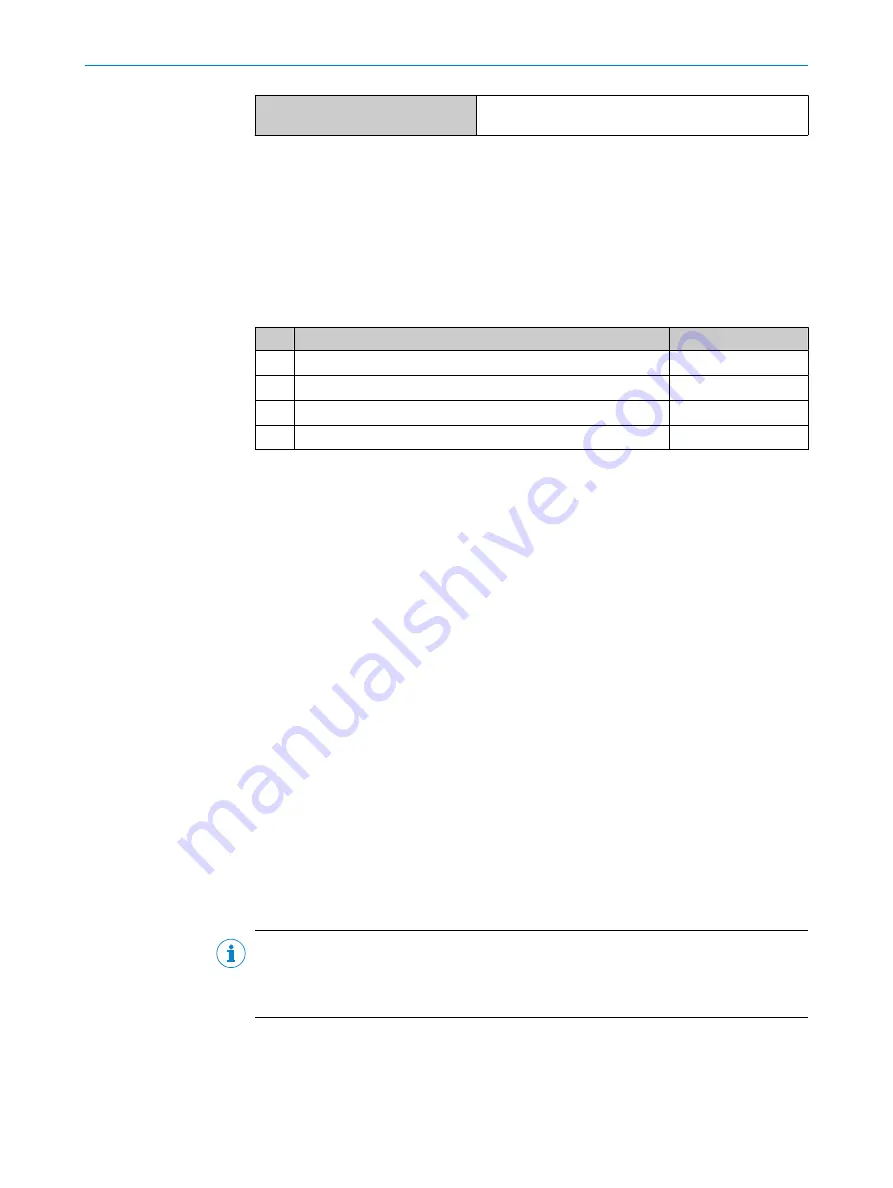
Parameter configuration server func‐
tion (data storage)
Yes
7.2.1
Process data
Data of the process data telegram (factory setting)
•
Measured distance value (unit: nanometer, 32 bit with sign)
•
Status Q1 (1 bit)
•
Status Q2 / Q
A
(1 bit)
The process data format and the offset for the distance value can be changed by
parameterizing the device.
Table 5: Process data formats
No.
Description
Comment
1
Distance (32 bit) + status Q1 (1 bit) + status Q2 / Q
A
(1 bit)
Factory setting
2
Level (32 bit) + status Q1 (1 bit) + status Q2 / Q
A
(1 bit)
-
3
Timer (32 bit) + status Q1 (1 bit) + status Q2 / Q
A
(1 bit)
-
4
Edge height (32 bit) + status Q1 (1 bit) + status Q2 / Q
A
(1 bit)
-
7.2.2
Device data
Device data (parameters, identification data, and diagnostic information) can be trans‐
mitted to and from the device. A product-specific device description file (IODD file) is
required in the IO-Link master for this purpose.
A download package containing the IODD file and supplementary documentation is
available at
7.3
Operation via SOPAS ET
Version 2021.2 and higher of the SOPAS Engineering Tool (SOPAS ET) software can
be used to parameterization of the device and for service and diagnostic purposes.
Measured values can be visualized and all device functions can be set and checked in
SOPAS ET. The device immediately applies parameters that have been modified using
SOPAS ET and permanently saves them. A separate function does not have to be called
up for this purpose.
SOPAS ET is particularly suitable for parameterizing the region of interest (ROI) and
edge height jump functions.
Requirements
■
A computer with the SOPAS ET software installed on it, and a free USB 2.0
compatible port
■
SICK SiLink2 Master (available as accessory)
■
Connection cable with M12 male and female connectors, 5-pin (available as
accessory)
NOTE
The most up-to-date version of the SOPAS ET software can be downloaded from
. The respective system requirements for installing SOPAS ET
are also specified there.
Establishing a connection
1.
Connect the device to the SiLink2 master via the male connector or an additional
connection cable.
2.
Connect the SiLink2 master to the computer using the supplied USB cable.
3.
Switch on and start the computer.
7
OPERATION
24
O P E R A T I N G I N S T R U C T I O N S | OD2000
8026231//2021-11-17 | SICK
Subject to change without notice