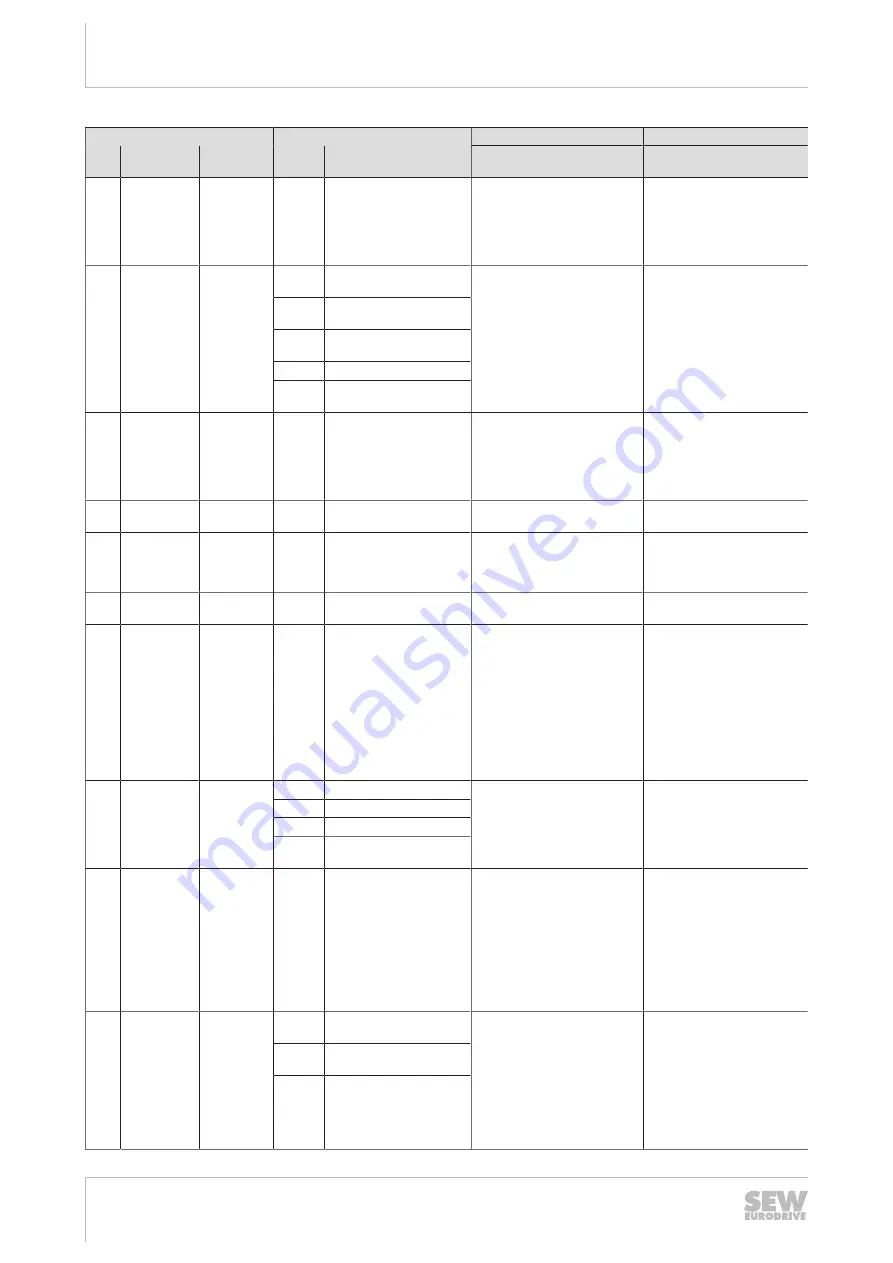
6
Service
Fault messages and list of faults
Compact Operating Instructions – MOVIDRIVE
®
MDX60B/61B
32
Fault
Subfault
Code Designation Response
(P)
Code
Designation
Possible cause
Measure
82
Open output
Immediate
stop
0
Output open with "VFC
hoist"
Only in "VFC hoist" mode:
• Two or all output phases are
interrupted.
• Nominal motor power too
small in relation to rated in-
verter power
• Check connection between
inverter and motor
• Check startup data and per-
form new startup, if neces-
sary.
84
Motor protec-
tion
Emergency
stop (P)
0
"Motor temperature emula-
tion" fault
• Motor utilization too high.
• I
N
-U
L
monitoring triggered
• P530 set later to "KTY"
• The motor
must
cool off,
then reset the fault
• Reduce load
• Extend ramps
• Observe longer pause
times
• Check P345/346
• Select a larger motor
2
Temperature sensor wire
break
3
No thermal motor model
available
4
UL monitoring fault
11
Temperature sensor short
circuit
86
Memory
module
Immediate
stop
0
Fault in connection with
memory module
• No memory card
• Memory card defective
• Tighten knurled screw
• Insert and secure memory
card
• Replace memory card
• Load delivery status and
parameter set
87
Technology
function
Immediate
stop
0
Technology function selec-
ted with standard unit
A technology function was acti-
vated in a standard device
Disable technology function
88
Flying start
Immediate
stop
0
"Flying start" fault
Only in VFC n-CTRL operating
mode:
Actual speed > 6000 rpm when
inverter enabled
Only enable a actual speed
≤ 6000 min
-1
92
DIP encoder
problem
Fault display
(P)
1
Stahl WCS3 dirt problem
Encoder signals a fault
Possible cause: Encoder is
dirty → clean encoder
93
DIP encoder
fault
Emergency
stop (P)
0
"Absolute encoder" fault
The encoder signals a fault,
e.g. power failure
• Connection cable between
the encoder and DIP11B
does not meet the require-
ments (twisted pair, shielded)
• Clock frequency too high for
cable length
• Permitted max. speed/accel-
eration of encoder exceeded
• Encoder defective
• Check absolute encoder
connection
• Check connection cables
• Set correct clock frequency
• Reduce maximum travel
speed or ramp
• Replacing absolute en-
coders.
94
EEPROM
checksum
Immediate
stop
0
Power section parameters Inverter electronics disrupted.
Possibly due to EMC influence
or defect.
Sending in a device for repair
5
Control unit data
6
Power section data
7
Invalid version of the con-
figuration data set
95
DIP plausibil-
ity fault
Emergency
stop (P)
0
Plausibility monitoring of
absolute position
No plausible position could be
determined
• Incorrect encoder type set
• IPOS
PLUS®
travel parameter
set incorrectly
• Numerator/denominator
factor set incorrectly
• Zero adjustment performed
• Encoder defective
• Set the correct encoder
type
• Check IPOS
PLUS®
travel pa-
rameters.
• Check travel speed.
• Correct numerator/denom-
inator factor
• Reset after zero adjustment
• Replacing absolute en-
coders.
97
Copy fault
Immediate
stop
0
Parameter set upload is/
was faulty
• Memory card cannot be writ-
ten or read
• Fault during data transmis-
sion
• Repeat copying process
• Restore delivery state
(P802) and repeat copying
process
1
Download of parameter
set to unit canceled.
2
Not possible to adopt pa-
rameters
Not possible to adopt pa-
rameters from memory
card
24770531/EN – 11/2017
Содержание Movidrive MDX60B
Страница 2: ...SEW EURODRIVE Driving the world...
Страница 60: ......
Страница 61: ......
Страница 62: ......
Страница 63: ......