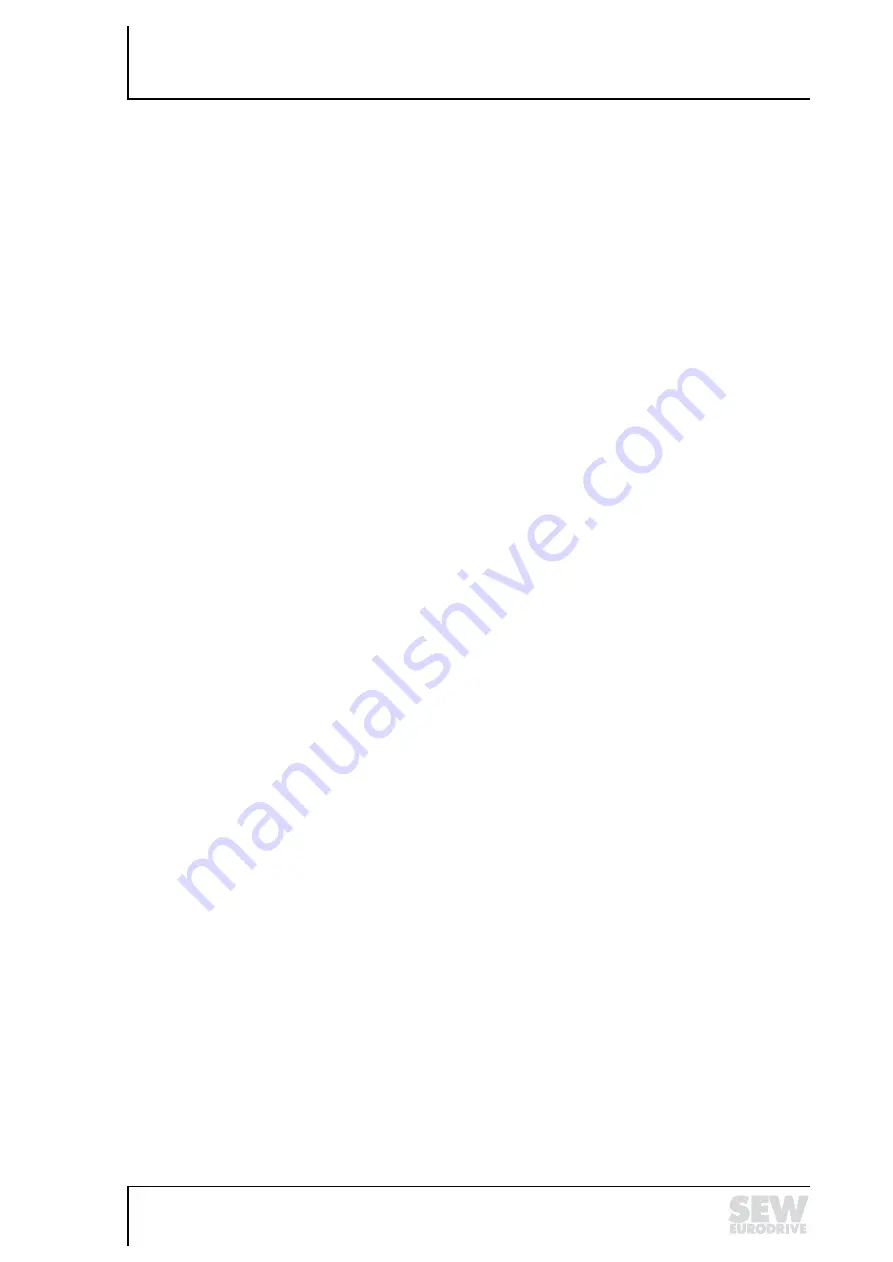
6
Startup
28
Manual
– ECDriveS® ECIO
6.2
Startup with Bus master
ECIO is a device that requires a remote PLC controller to connect and transfer data to
control its digital I/O points. This section describes the network architecture ut ilized for
the module and provides the data mapping details to access I/O for the 3 main prot oc ols
that the module recognizes.
6.2.1
ECDriveS
®
network architecture
Each module communicates to its adjacent modules and to any connected PC or PLC via
Ethernet physical media. ECDriveS
®
modules recognize 3 TCP/IP based protocols:
Modbus TCP
Profinet I/O
EtherNet/IP
Modbus TCP is the “native” protocol for communications between the fieldbus modules
modules and the ECShell PC software. When the modules create connections bet ween
them, they utilize Modbus TCP for inter-module communication.
EtherNet/IP is recognized by the modules and any given module can be at t ached t o an
EtherNet/IP capable PLC (Allen-Bradley ControlLogix or CompactLogix platforms for
example) and be recognized as a “Generic Ethernet Module” or explicitly as a module by
using the provided EDS file.
Profinet I/O is recognized by the modules and can be attached to any Profinet I/ O c apa-
ble PLC (applicable Siemens platforms). All protocols access the same internal data
locations on a given module.
Each EC
IO module’s internal data structure is arranged and addressed as Modbus Hold-
ing registers. The on-board communication and control processes attach logical mean-
ings to each holding register and read and write data to specific registers to initiate and/or
react to events. Certain registers contain information as to how the module is configured
(Inputs, Outputs, polarity etc.) for its local controls.
Understanding assemblies
The holding registers described above we will define as Module Register Addresses and
are used for the function of the module regardless of if any remote PLC or PC is connect-
ed. There are many Module Register Addresses that are used for the operation of the
module that are not applicable, required, or should even be made available t o a remot e
PLC. When connecting to a PLC, the module needs to gather cert ain specific Module
Register Addresses located scattered throughout the entire listing of Module Register
Addresses into a concise contiguous group or Assembly that the PLC can efficiently read
from and write to. The following Figure illustrates this concept:
Содержание ECDriveS ECIO-8-24-00
Страница 43: ......