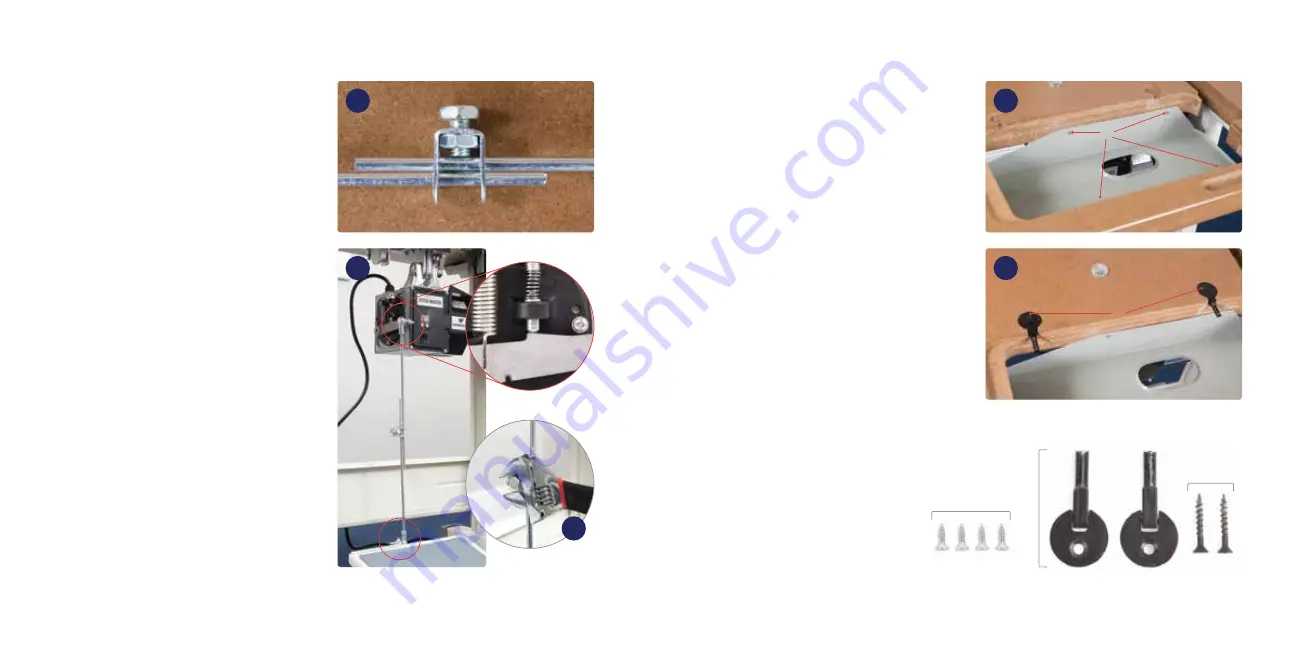
Linkage Bar Installation
1.
Loosen the center nut on the linkage bar
(
A
) so that it will slide apart (
18
). Slide into
furthest position so the linkage bar is at
its longest length and re-snug the nut. On
each end of linkage bar take off the first nut
and lock washer.
2.
Bolt the linkage bar (
A
) to the outer-most
holes of the motor operation lever on the
Workhorse™ Servo Motor and the treadle-
bracket of the treadle (
19
). By increasing
or decreasing the overlap of the linkage
bar, different treadle pedal angles can be
achieved depending on user preference.
Use a crescent wrench to set the angle (
20
).
3.
If the linkage bar overlap is too agressive,
the pedal angle will be extreme preventing
the operation lever to make contact with its
resting stop. When this happens, the motor
will not run. Image (
B
) is correct with the
pedal not actuated.
Install Oil Tray and Hinges
1.
Find the metal oil tray (
C
) and reference
the belt slot of the tabletop (
21
). Place the
oil tray (
C
) under the tabletop and line up
the mounting holes in the oil tray to the
pilot holes inside the rim of the tabletop
cutout. Next, thread in the four flat head
tapping screws (
D
) to attach the oil tray
(Due to small size, extras are included in
the package). Use a #1 Stubby Phillips
screwdriver.
2.
Place the two hinges (
E
) into the pre-made
hinge holes in the tabletop. Secure with
included wood screws (
F
) (
22
).
18
19
20
21
22
Hardware is scaled 50%
E
F
D
A
A
B
C
E
E
D
F
Stitch Master
®
Guidebook: Assembling the Stitch Master
14
13