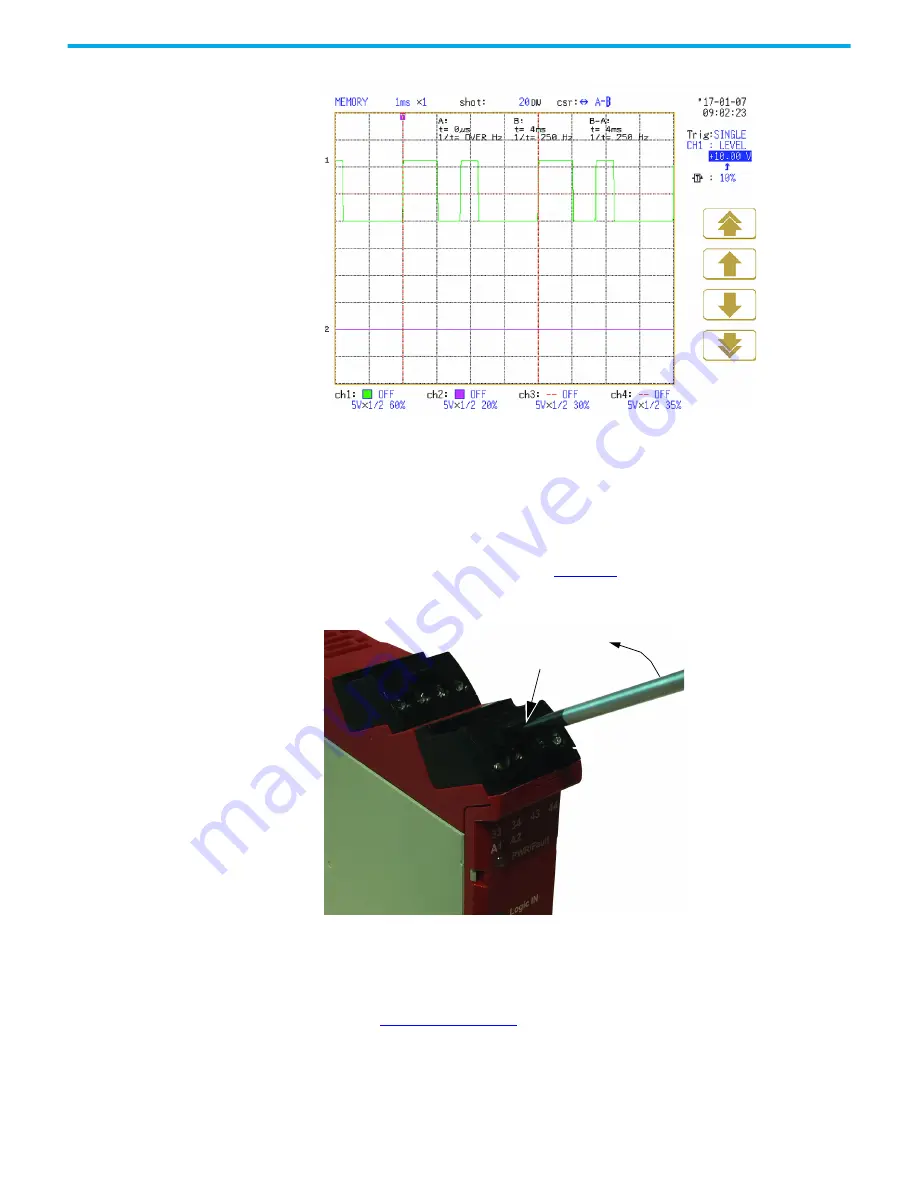
Rockwell Automation Publication 440R-UM013F-EN-P - July 2021
75
Chapter 11 Troubleshooting
Figure 87 - The B1-B2 Waveform When the EMD Safety Relay Output is ON
Terminal Block Removal
and Replacement
Terminal blocks can be replaced following these instructions.
Terminal Block Removal
GSR safety relays have removable terminal blocks. Use a screwdriver as a lever
to remove the blocks. As shown in
, insert the screwdriver into the
slot and pry up.
Figure 88 - Terminal Block Removal
Terminal Block Replacement
The terminal blocks are keyed to help prevent a block from being inserted into
an incorrect location. The orange-colored insert provides the orientation of the
key (see
1.
Insert
2.
Pry Up
Содержание 440R-D22R2
Страница 12: ...12 Rockwell Automation Publication 440R UM013F EN P July 2021 Chapter 1 Overview Notes...
Страница 16: ...16 Rockwell Automation Publication 440R UM013F EN P July 2021 Chapter 2 Installation Notes...
Страница 81: ...Rockwell Automation Publication 440R UM013F EN P July 2021 81 Appendix A Specifications Notes...
Страница 82: ...82 Rockwell Automation Publication 440R UM013F EN P July 2021 Appendix A Specifications...
Страница 89: ...Rockwell Automation Publication 440R UM013F EN P July 2021 89 Guardmaster Safety Relays User Manual...