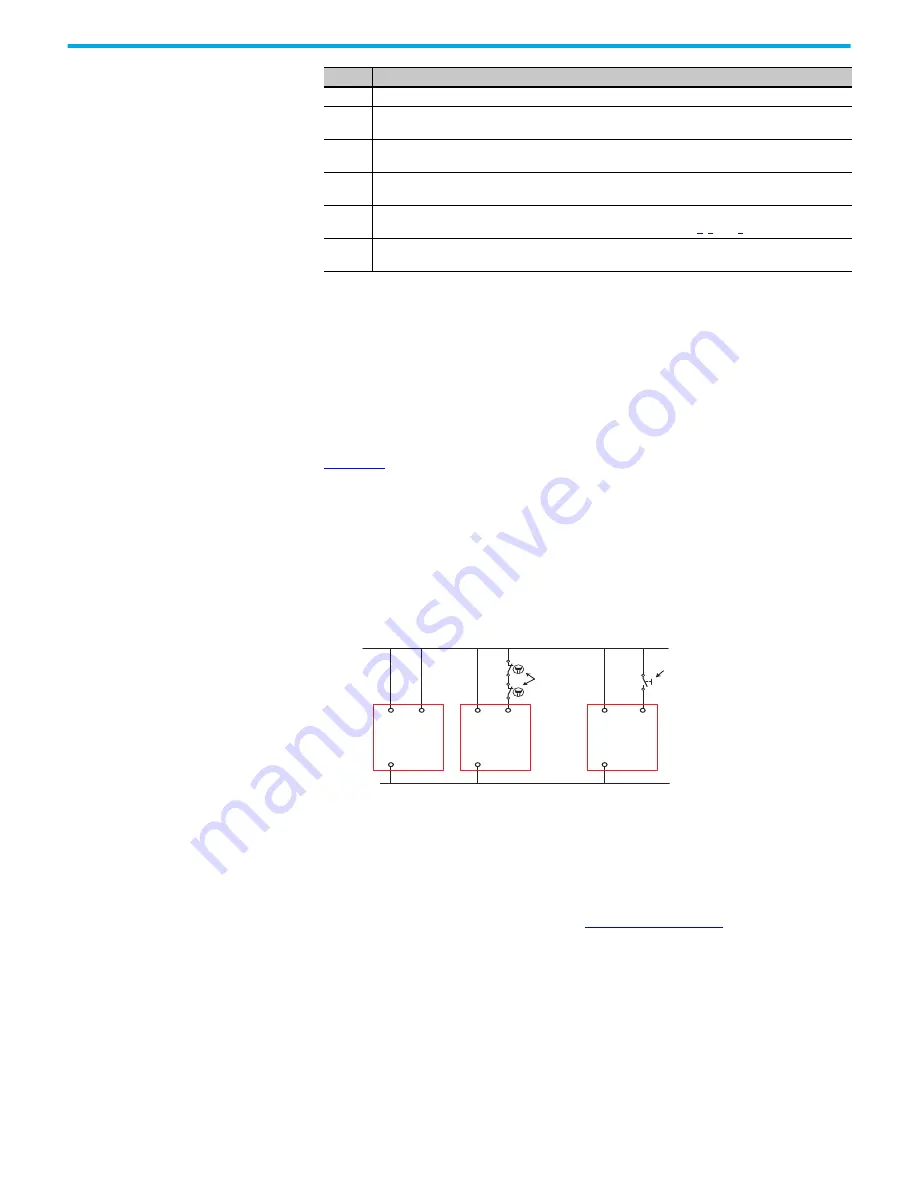
28
Rockwell Automation Publication 440R-UM013F-EN-P - July 2021
Chapter 3 Power, Ground, and Wire
Automatic/Manual Reset
Use automatic reset when the risk assessment does not require additional
manual intervention to reset the safety system. Automatic reset is often used
with partial body access or where an additional control is implemented in the
machine control system to start the hazardous portion of the machine after the
safety inputs are closed.
When automatic reset is desired, the S34 input must be connected to 24V DC.
shows three possibilities:
a. A direct connection
b. A connection through some monitoring contacts
c. A connection through a normally open push button.
You can combine the connection through a monitoring contact and push
button. When a push button is used, the reset occurs when the circuit is closed
(not when it is released).
Figure 21 - Automatic/Manual Reset Connections
Monitored Reset
Monitored reset requires a specific signal to turn on the safety outputs. The
safety inputs and single wire safety input (if used) must be closed before the
reset. The reset signal must cycle from 0V to 24V and back to 0V within a
duration of 250…3000 ms, as shown in
on the trailing edge. If the reset signal is too short or too long, the reset
function is not executed and can be tried again.
Monitored reset must be used in applications that have full-body access to the
hazard. Monitored reset can also be used in applications that require partial
body access.
Circuit
Description
1
In automatic/manual reset, a direct connection can be made to 24V DC.
2
Output devices are monitored with their normally closed contacts. This circuit can only be used in
automatic/manual reset.
3
A normally open push button is used. The relay can be configured for automatic/manual reset or
monitored manual reset.
4
Output devices are monitored along with a normally open push button. The relay can be configured for
automatic/manual reset or monitored manual reset.
5
An EM or EMD expansion safety relay is used to supply the voltage to terminal S34. This circuit can also
contain feedback contacts and a reset push button, similar to circuits
, and
.
6
A PLC is used to generate the reset signal. The GSR safety relay can be configured for either automatic/
manual or monitored manual reset.
+24V DC
24V DC Com
S34
A1
A2
(a)
(b)
(c)
S34
A1
A2
S34
A1
A2
CI, DI, DIS, or SI
CI, DI, DIS, or SI
CI, DI, DIS, or SI
Contactor
Monitoring
Momentary Push
Button (N.O.)
Содержание 440R-D22R2
Страница 12: ...12 Rockwell Automation Publication 440R UM013F EN P July 2021 Chapter 1 Overview Notes...
Страница 16: ...16 Rockwell Automation Publication 440R UM013F EN P July 2021 Chapter 2 Installation Notes...
Страница 81: ...Rockwell Automation Publication 440R UM013F EN P July 2021 81 Appendix A Specifications Notes...
Страница 82: ...82 Rockwell Automation Publication 440R UM013F EN P July 2021 Appendix A Specifications...
Страница 89: ...Rockwell Automation Publication 440R UM013F EN P July 2021 89 Guardmaster Safety Relays User Manual...