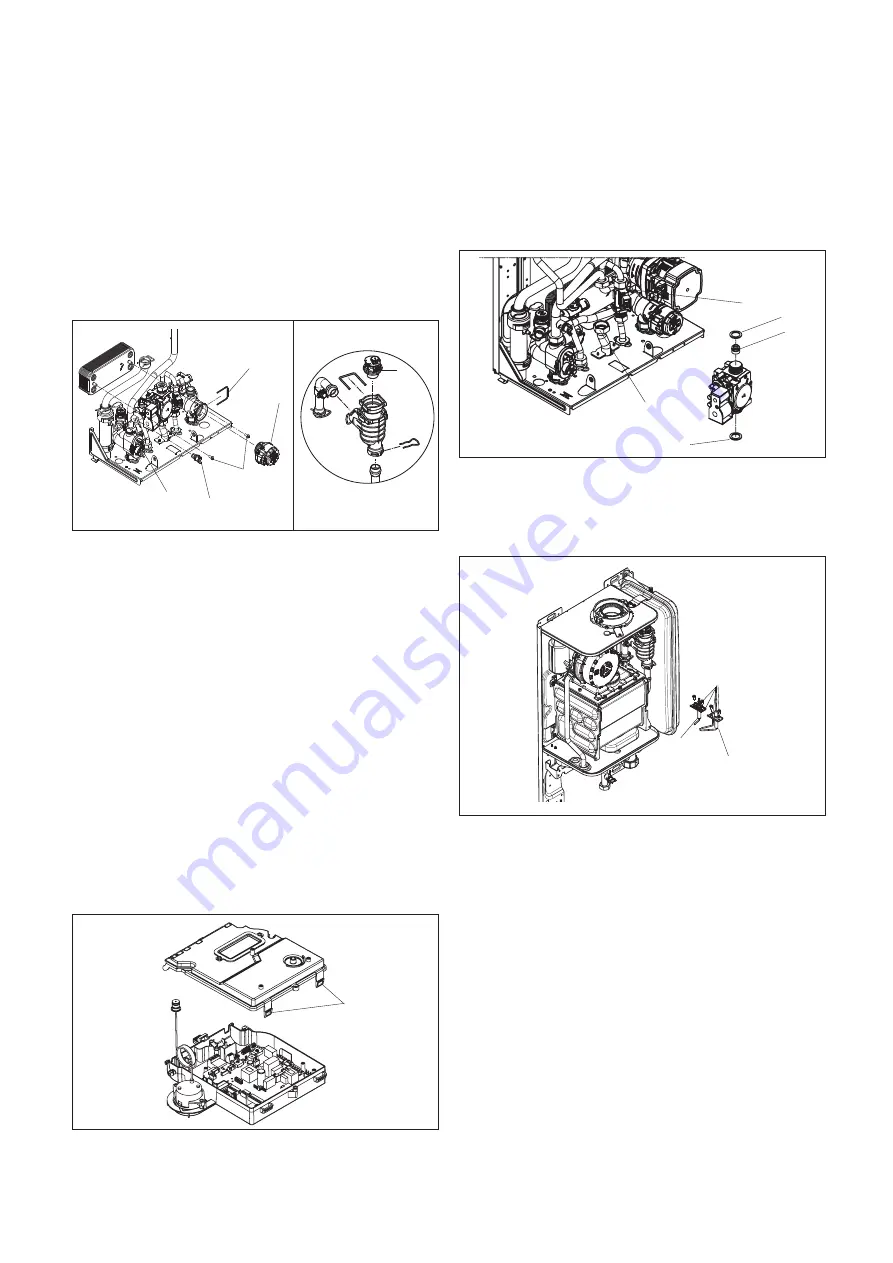
21
6.8 LOWER AUTOMATIC AIR RELEASE VALVE
(fig. 29)
Carry out component removal procedure as described in 6.4.
Remove the expansion pipe locking pin (
B
) from the pump as-
sembly and remove the expansion pipe. Locate and remove
the AAV locking pin (
I
) from the pump assembly and remove
the AAV assembly (
J
). Replace in the reverse order.
6.8.1 TOP AUTOMATIC AIR RELEASE VALVE (fig. 31)
Carry out component removal procedure as described in 6.4.
Unclip and remove the air chamber front cover. Remove the
AAV locking pin (
K
) from the deaerator assembly and remove
the AAV assembly (
L
). Replace in the reverse order.
6.9 WATER PRESSURE SWITCH (fig. 30)
Carry out component removal procedure as described in 6.4.
Locate and remove the locking pin (
M
) from the water pressure
switch (
N
). Remove the wiring. Carefully withdraw the switch.
Replace in the reverse order.
Fig. 30
Fig. 31
M
N
Y3
G2
H2
K
L
6.10 FLOW THERMISTOR (fig. 5 - pos. 18)
Carry out component removal procedure as described in 6.4.
Unclip and remove the air chamber front cover. Unclip the flow
thermistor from the flow outlet pipe. Disconnect thermistor
electrical plug. Replace in the reverse order.
6.11 RETURN THERMISTOR (fig. 5 - pos. 20)
Carry out component removal procedure as described in 6.4.
Unclip the return thermistor from the return inlet pipe. Discon-
nect thermistor electrical plug. Replace in the reverse order.
6.12 PRINTED CIRCUIT BOARD (fig. 33)
Carry out component removal procedure as described in 6.4.
Pull the control fascia forward and lower it. Push the clips (
O
)
which secure the PCB cover, remove cover, after carefully tak-
ing note of all wiring connections and jumper tag configuration.
Disconnect all wiring from the PCB, locate and remove the
PCB securing screws, remove the required PCB. Replace in
the reverse order ensuring that the position of the 2 control
knobs are correctly aligned with the respective potentiometers
on the PCB.
Ensure that the correct jumper tag configuration has been
respected. It will be necessary to check the functioning of the
PCB is set for the correct boiler output, type and application.
Details on setting fan speeds can be found in section 7.10.
Fig. 33
O
6.13 GAS VALVE (fig. 34)
Carry out component removal procedure as described in 6.4.
The gas valve must be changed as complete unit. Disconnect
the electrical plug and leads from the gas valve, slacken and
unscrew gas valve inlet
and outlet connections.
Please note,
the sealing washers (
Q
) must be discarded and
replaced with new sealing washers.
Unscrew gas pipe connections (
S-T
), the gas valve can now
be removed. Replace in the reverse order. Check and adjust
burner pressure settings.
WARNING, A GAS TIGHTNESS CHECK MUST BE CAR-
RIED OUT.
6.13.1 INJECTOR (fig. 34)
Carry out component removal procedure as described in 6.4.
Unscrew and remove gas pipe connections (
S-T
). Locate and
remove the injector (
U
) inside the valve. Replace in the reverse
order. Check and adjust burner pressure settings.
WARNING, A GAS TIGHTNESS CHECK MUST BE CAR-
RIED OUT.
Fig. 34
Q
Q
U
S
T
6.14 ELECTRODES (fig. 35)
Carry out component removal procedure as described in 6.4.
Remove the air chamber front cover. Disconnect the electrode
leads and ancillary wiring from their respective connectors. Re-
move the retaining screws (
V
) for electrode. Remove the spark
ignition electrode (
W
). Remove the flame sensor electrod (
Y
).
Fig. 35
V
W
Y
6.15 FLUE FAN+MIXER (fig. 36-37)
Carry out component removal procedure as described in 6.4.
Remove the air chamber front cover. Locate and remove the
gas pipe locking pin (
A1
) and swing/rotate the gas pipe away
from the fan assembly (
B1
), (if necessary unscrew the gas
pipe from the gas valve
G1
). Locate and slacken the silencer
(
H1
). Locate and remove the sense electrode. To remove the
fan (
E1
), disconnect the electrical connections attached to the
fan, locate and remove the four screws (
F1
). Gently ease the
fan from its location. Replace in the reverse order. Ensure all
seals are in good condition, taking care to ensure they are
replaced correctly.
6.16 BURNER (fig. 36)
Carry out component removal procedure as described in 6.4.
Remove the air chamber front cover. Locate and remove the
gas pipe locking pin (
A1
) and swing/rotate the gas pipe away
from the fan assembly (
B1
), (if necessary unscrew the gas
pipe from the gas valve
G1
). Locate and slacken the silencer
(
H1
), disconnect the electrical connections attached to the
fan. Disconnect the electrode leads and ancillary wiring from
their respective connectors. Locate and remove the screws
(
I1
) which secure the burner assembly in position to the heat
exchanger (
J1
). Gently ease the fan assembly out of its location.
Once the assembly has been removed, the burner (
K1
) can
be withdrawn from the heat engine. Ensure the seals (
L1
) is in
good condition, taking care to ensure it is replaced correctly.
Replace in the reverse order.