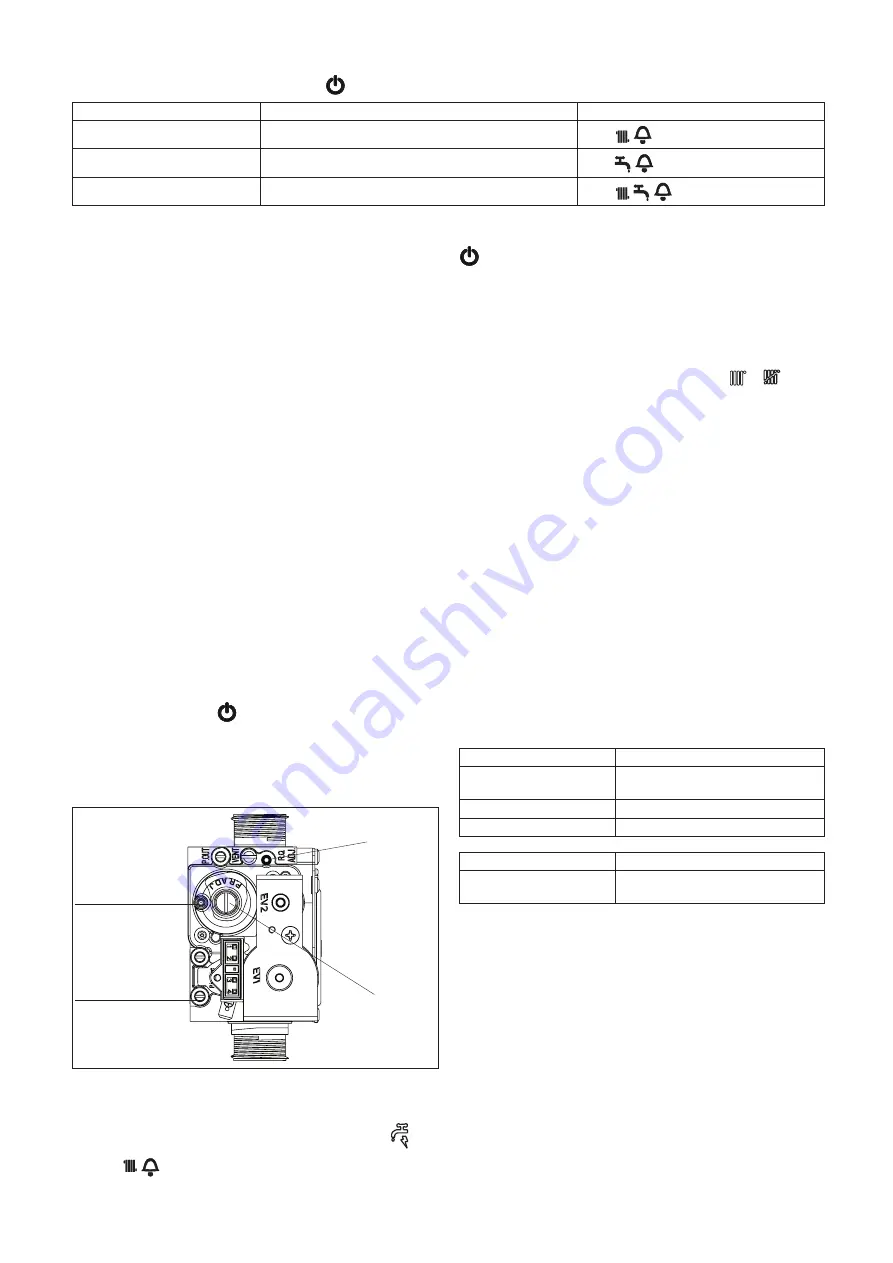
25
7.3.1 CO
2
FUNCTION SETTINGS
Locate the CO
button (see 7.3).
Select the main selector switch in position
.
CO
2
FUNCTIONS
ACTION ON THE BUTTON
LED STATUS
combustion analysis mode
press once = burner running at maximum heating
ACO
gas valve maximun setting
press twice = burner running at maximum DHW
ACO
gas valve minimum setting
press three time = burner running at minimum
ACO
NOTE
1 - Any additional pressing of CO
button after the third time the burner switched between maximum DHW and minimum.
2 - To restart the CO
function it is necessary to pass throught the
position with the main selector switch
7.3.2 GAS VALVE MAXIMUM SETTING
Set the CO
button at maximum (see 7.3.1), once the maximum is
obtained check that it corresponds with the appropriate CO
2
value
(Maximum) for the respective appliance (see 2.11). If the CO
2
reading is correct, proceed to gas valve minimum setting (7.3.3).
However, if the CO
2
reading is incorrect, the maximum gas
pressure must be adjusted as follows:
•
using a 2.5mm Allen key, very slowly turn the maximum
adjustment screw (see fig. 45) – clockwise to decrease, counter
clockwise to increase – until the correct value is displayed on
the CO
2
analyser (allow time for the analyser to stabilise).
7.3.3 GAS VALVE MINIMUM SETTING
Set the CO
button at minimum (see 7.3.1), once the minimum
is obtained check that it corresponds with the appropriate CO
2
value (Minimum) for the respective appliance (see 2.11). If the
CO
2
reading is correct, proceed to completion (7.3.4).
However, if the CO
2
reading is incorrect, the minimum gas
pressure must be adjusted as follows:
•
locate the minimum adjustment screw (fig. 45), using a suit-
able screwdriver remove the protection plug
•
using a 4mm Allen key, very slowly turn the minimum adjust-
ment screw (see fig. 45) - clockwise to increase, counter
clockwise to decrease - until the correct value is displayed
on the CO
2
analyser (allow time for the analyser to stabilise).
7.3.4 COMPLETION
On completion of the combustion analysis check and/or any
gas valve adjustment, refit the plug (fig. 44
L2)
and move the
mode selector throught
position. Remove the test probe
from the test point and refit the sealing screw/s and/or cap.
IMPORTANT
A GAS TIGHTNESS CHECK MUST BE CARRIED OUT IF ANY
GAS CARRYING COMPONENTS HAVE BEEN REMOVED,
REPLACED OR DISTURBED.
fig. 45
Minimum
screw
Inlet gas pressure
connection
Compensation pipe
connection
Maximum
screw
7.4 COMBUSTION ANALYSIS TEST
To carry out the combustion analysis, proceed as follows:
•
Turn the function selector in OFF position
•
Turn the hot water temperature selector in position
•
Wait for burner ignition (about 6 seconds). The display shows
“ACO
” and the boiler operates at maximum heating
•
Insert the flue gas analyser probe into the flue gas test point
(see fig. 41).
•
Operate the boiler in combustion analysis mode (see 7.3.1)
and compare the values with those shown in section 2 (Nat.
Gas) or section 9 (LPG). If different adjust the gas valve
according to 7.3.1, 7.3.2, & 7.3.3.
•
The combustion analysis function remains active for 15
minutes, it is possible to interrupt in advance moving the
mode selector switch in desired position (
-
), bring
the domestic hot water temperature adjustment knob back
to the required position.
• Note:
If a measured CO/CO
2
ratio of 0.004/1 or less AND a
CO reading of less than 350ppm cannot be achieved, please
contact Vokera technical for advice.
Note:
When checking the air inlet test point, insert the probe
no more than 25mm into the test point.
7.5 CHECKING THE EXPANSION VESSEL
Carry out the component removal procedure as described in
6.4. You must ensure that the boiler is completely drained of
water. Using a suitable pressure gauge, remove dust cap on
expansion vessel and check the charge pressure. The correct
charge pressure should be 1.0 bar ± 0.1 bar. If the charge
pressure is less, use a suitable pump to increase the charge.
NOTE
You must ensure the drain valve is in the open position whilst
re-charging takes place. Replace the dust cap and carry out
the relevant commissioning procedure (section 5).
7.6 EXTERNAL FAULTS
Before carrying out any faultfinding or component replacement,
ensure the fault is not attributable to any aspect of the installation.
7.6.1 INSTALLATION FAULTS
Symptom
Possible cause
No ignition
Check wiring/check electrical
supply
No hot water
Check pipe-work
No heating
Check external controls
Fault
Possible cause
Fault code
Check gas supply, check flue
system, check polarity
7.7 ELECTRICAL CHECKS
Any electrical checks must be carried out by a suitably quali-
fied person.
7.7.1 EARTH CONTINUITY TEST
Isolate the appliance from the electrical supply, and using a
suitable multi-meter carry out a resistance test. Connect test
leads between an appliance earth point and the earth wire of
the appliance supply cable. The resistance should be less than
1 OHM. If the resistance is greater than 1 OHM check all earth
wires and connectors for continuity and integrity.
7.7.2 SHORT CIRCUIT CHECK
Isolate the appliance from the electrical supply, and using a
suitable multi-meter, carry out a short circuit test between the
Live & Neutral connections at the appliance terminal strip.
Repeat above test on the Live & Earth connections at the ap-
pliance terminal strip.
NOTE
Should it be found that the fuse has failed but no fault is indi-
cated, a detailed continuity check will be required to trace the
fault. A visual inspection of components may also assist in
locating the fault.