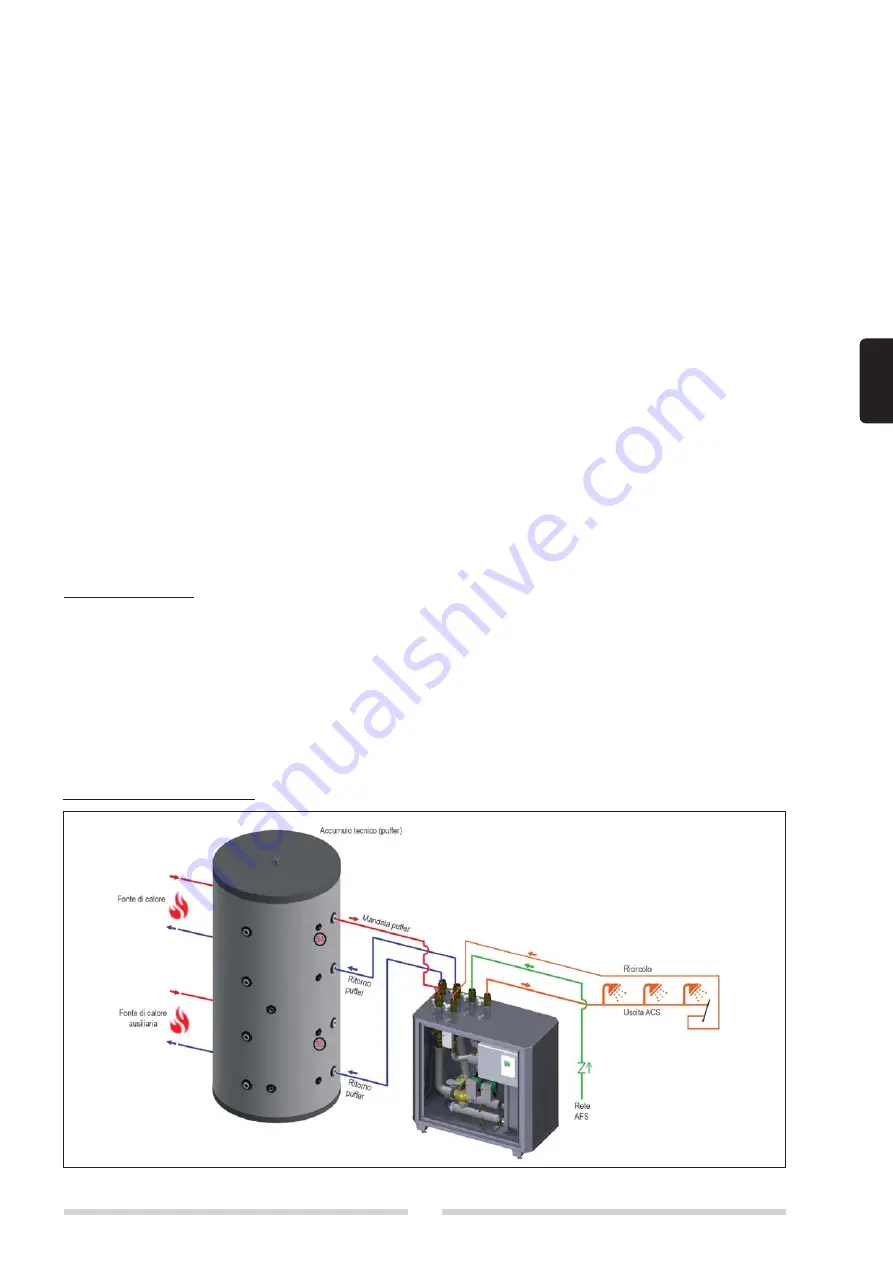
15
ENGLISH
On completion of all transport or handling operations, always check the tightness of the water fitting ring nuts.
Take particular care when connecting the unit to the water supply. When tightening a fitting, always hold the opposite
fitting steady with a second tool to avoid damage.
Connect up the pipes according to the legend on the unit itself and according to the instructions given in this manual. it
is recommended to minimize the length of the connection pipes to the buffer storage.
The following materials are recommended for the construction of the piping system: steel or copper for the primary circuit;
galvanised steel, copper or hot water compatible plastic for the secondary circuit. Galvanised pipes and fittings must only
be used in the secondary (DHW) circuit, and care must be taken to avoid electrochemical corrosion.
a
Do not install the unit in gravity feed hot water systems!
b
Make sure that the installation position provides easy visibility of and access to the safety valves.
b
Connect the safety valves to a drain in conformity to applicable standards.
b
Make sure that no obstacles are present between the safety valve and the unit.
b
The diameter of the drain pipe must not be smaller than that of the safety valve’s drain fitting. The drain pipe should
be no longer than 2 metres and should have no more than two bends in it. If this length has to be exceeded, in-
crease the diameter of the pipe. Never exceed 4 metres and 3 bends.
b
Do not install filters or other restrictions.
b
Make sure that the pipes are watertight before securing them in place.
b
Check that all threaded fittings on the unit are tightened to the correct tightening torque (in case they have worked
loose during transport).
b
Make sure that the unit is disconnected from the mains power supply before opening the casing of the control panel!
SAFETY WARNINGS
b
The unit can become hot enough to cause burns if touched.
b
In the event of a power failure, the motorised control valve could remain in the open position, causing the whole
system to become hot enough to cause burns if touched.
b
Water in the unit can be very hot and under pressure. Therefore, before performing any work, always drain the unit
and close the shut-off valves on the primary and secondary circuits.
b
The unit must be installed and put into service in strict conformity to all laws and standards applicable in the place
of installation, and according to best professional practices.
EXAMPLE OF INSTALLATION
Содержание SC ACS 160
Страница 9: ...9 ENGLISH WIRING DIAGRAM ...
Страница 43: ...43 ENGLISH ...