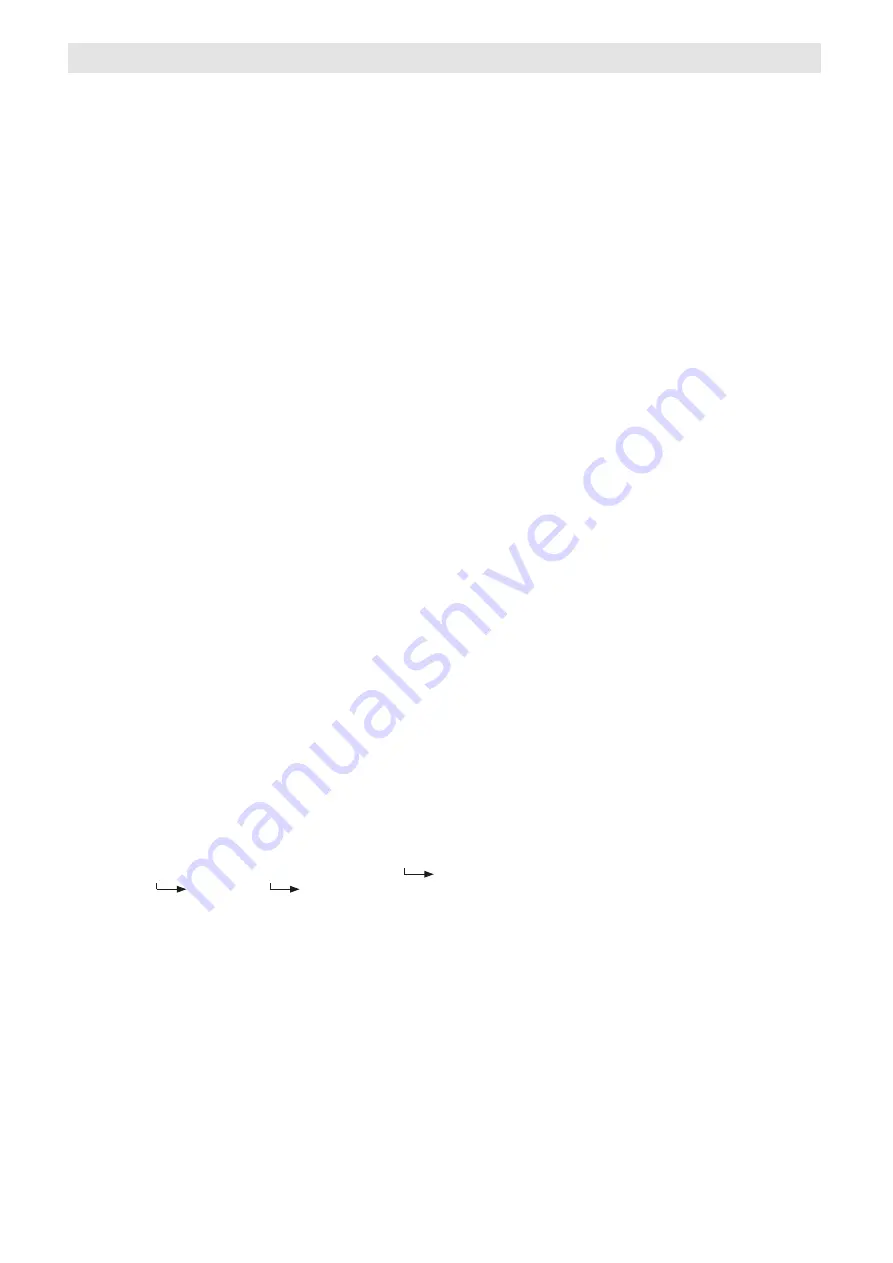
42
GENERAL
Once the appliance has been serviced, the benchmark Service
Record must be completed.
For UK only
It is important that the Benchmark Service Record is correctly
completed and handed to the user. Failure to install and
commission the appliance to the manufacturers instructions
will invalidate the warranty.
To ensure the continued safe and efficient operation of the
appliance, it is recommended that it is checked and serviced
at regular intervals. To ensure correct and safe operation of the
appliance, it is essential that any worn or failed component be
replaced only with a
genuine Vokèra spare part
. It should be
remembered that although certain generic components may
look similar, they will be specific to an individual appliance
or product range. Use of non-genuine Vokèra spare parts
could invalidate your warranty and may pose a potential
safety hazard. The frequency of servicing will depend upon
the particular installation conditions, but in general, once per
year should be sufficient. It is the law that any servicing work
is carried out by competent person such as a Vokèra engineer,
an approved service agent, British Gas, GAS SAFE registered
personnel or other suitably qualified personnel. The following
instructions apply to the appliance and its controls, but it should
be remembered that the central heating and the domestic hot
water systems would also require attention from time to time.
ROUTINE ANNUAL MAINTENANCE
The appliance incorporates many ‘state-of-the-art’
components that are either ‘solid-state’ or are regarded as
‘non-serviceable’ items. As a consequence, the requirements
for routine annual maintenance are focussed upon:
1. ensuring that the appliance and flue system are in a safe
condition
2. ensuring that the appliance is operating safely
3. ensuring that the appliance is performing to its design
specification.
When the appliance has been installed to within the minimum
stated clearances; the appliance layout is such that it enables
routine annual maintenance to be carried out entirely from the
front of the appliance.
NOTE
Any noticeable defect or deterioration on or within the
appliance and flue system that impacts or affects the above
requirements; will warrant further diagnosis and repair, which
may result in the replacement of components.
Specific advice and instruction on the removal and replacement
of component parts of the appliance can be found online using
the adjacent QR code or by visiting our website.
ROUTINE ANNUAL MAINTENANCE REQUIREMENTS
1. Check the operation of the appliance in both the heating
and hot water modes and ensure the performance is in line
with the appliance specification.
2. Using the UI menu, navigate to the alarms history and check
for any recent alarm events (menu string is: MENU
SETTINGS
TECHNICAL
ERROR HISTORY).
Refer to the alarm/fault codes description chart for further
information.
3. Remove the front cover (see section 6.12) and visually
inspect the internal components and electrical wiring for
any defect or deterioration.
4. Visually check for any dirt or debris within the condensate
trap (the trap is translucent and can be checked visually).
5. Replace the front cover as detailed in section 6.12 taking
notice of the importance of ensuring that the effectiveness
of the – front cover – seals are not compromised.
6. Carry out a combustion analysis as detailed in section
6.12.
7. Visually check the entire flue system for any damage, defect,
or deterioration.
NOTE
In order to access the ‘alarms history’ it is necessary to access
the password protected settings. Refer to section 8 for further
details.
7. SECTION - SERVICING INSTRUCTIONS
UNSCHEDULED MAINTENANCE
The appliance incorporates software that monitors the
operating conditions of the appliance, and will record any
‘unusual usage conditions’ that will affect the requirement to
remove and clean the burner/heat exchanger assembly. When
the ‘unusual usage’ hours reach a pre-determined threshold,
the appliance will signal – via alarm code E091 – that the heat
exchanger requires to be cleaned.
REPLACEMENT OF COMPONENTS
Although it is anticipated that this appliance will provide years of
trouble-free service and outstanding performance; the lifespan of
any component will be determined by factors such as operating
conditions and usage levels. Should the appliance develop a
fault, the fault-finding section of this manual will greatly assist
in determining the cause; however further advice can be sought
from the Vokera Technical Help-line. Remember always to use
only genuine Vokera spare parts.
COMPONENT REMOVAL PROCEDURE
To remove/replace a component, access to the interior of the
appliance is usually essential.
Always
isolate the appliance from the electrical supply – and
if necessary remove the fuse.
• Close all service valves if any hydraulic and/or gas carrying
item is to be removed.
• Remove the front cover – and where necessary or
convenient – the side panels of the appliance as detailed in
5.7.1.
• If required, drain the primary circuit via the drain valve
(located adjacent to the diverter valve) using the tubing
supplied with the appliance.
• If required, drain the secondary circuit via the available DHW
outlets.
NOTE
When removing a hydraulic component, ensure that some
water absorbent cloths are available to catch any residual
water that may drip from the appliance and/or the removed
component.
When the appliance has been installed to within the stated
minimum clearances; it may be necessary to remove
adjacent components in order to facilitate access to a specific
component.
Carry out the relevant elements of the commissioning
procedure (section 8) after replacing a component.
ALWAYS TEST FOR GAS TIGHTNESS IF ANY GAS
CARRYING COMPONENT HAS BEEN DISTURBED,
REMOVED, OR REPLACED.
WHEN REPLACING THE SIDE PANELS AND/OR THE
FRONT COVER, ENSURE THE ROOM SEALED INTEGRITY
OF THE APPLIANCE HAS NOT BEEN COMPROMISED –
REFER TO 5.7.1.
To obtain detailed specific information and instructions on how
to remove and replace specific components, please access
our online resources by logging on to our website.
www.vokera.co.uk
www.vokera.ie