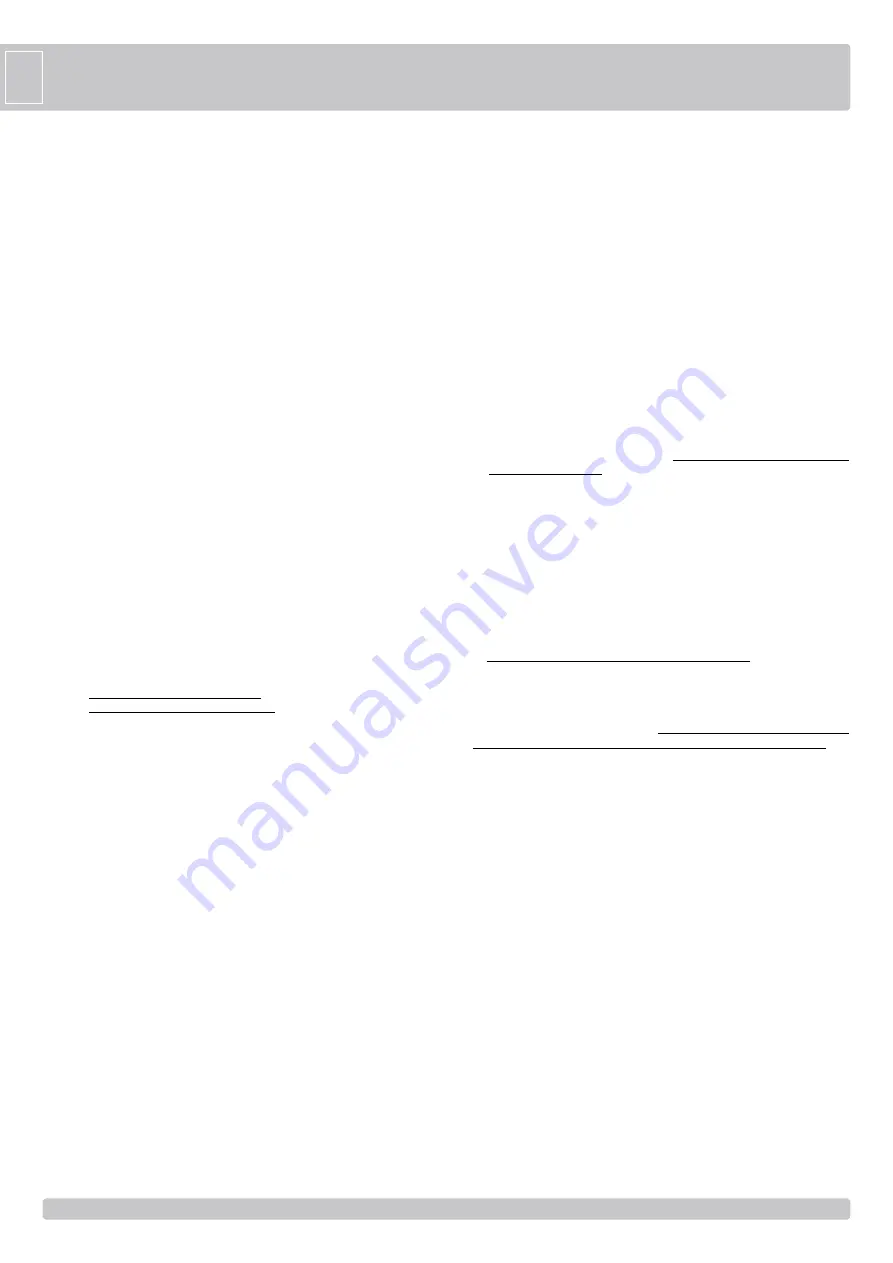
30
30
G
B
POINT B
- sETTINGs
DIP 1
MOTOr rOTATION DIrECTION CHECK (see Point C)
DIP 2
PrOGrAMMING (see Point D)
DIP 2-1 PrOGrAMMING Of PEDEsTrIAN OPENING (see Point E)
DIP 3
ON - Automatic Closing ENABLED
OFF - Automatic Closing DISABLED
DIP 4
ON - Radio receiver STEP BY STEP
OFF - Radio receiver AUTOMATIC
DIP 5
ON - STEP BY STEP
Single pulse contact (K BUTT)
Pedestrian button (PED BUTT)
OFF - AUTOMATIC
Single pulse contact (K BUTT)
Pedestrian button (PED BUTT)
DIP 6
ON - Photocells active only in closing
OFF - Photocells always active
DIP 7
ON - Encoder enabled for PLUS operator
OFF - Encoder disabled
DIP 8
ON - Blinker pre-flashing
OFF - Blinker normal flashing
DIP 9
ON - Low speed in approaching DISABLED
OFF - Low speed in approaching ENABLED
DIP 10
ON - Electronic brake ENABLED (HARD brake, only for FAST operators)
OFF - Electronic brake DISABLED (SOFT brake, only for FAST operators)
DIP 11
ON - Gradual start ENABLED
OFF - Gradual start DISABLED
DIP 12
ON - Safety strip self test ENABLED
OFF - Safety strip self test DISABLED
DIP 13
ON - Motor operation control by external power relays (only for S1/R2 and S1/
R4 control boards). Encoder, low speed in approaching, gradual start
and electronic brake features, low speed and torque regulator will be
automatically disabled regardless their dip-switches and trimmers position.
OFF - Standard motor operation control without power relays
DIP 14
- OFF
DIP 15
- OFF
DIP 16
- ON
DIP 17
ON - close command after the transit through the photocell ENABLED
OFF - close command after the transit through the photocell DISABLED
DIP 18 ON - Working with motors 120V 60Hz
Off - Working with motors 230V 50-60Hz
LED WArNINGs
DL1 - programming activated (red)
DL2 - stop contact NC (red)
DL3 - open limit-switch contact (red)
DL4 - close limit-switch contact (red)
DL5 - photocell contact (NC) (red)
DL6 - gate opening (green)
DL7 - gate closing (red)
DL8 - safety strip contact (NC) (red)
DL9 - Encoder output state
fUsEs
F1 T100mA
Fuse for accessories protection
F2 T5A
Fuse for motor windings protection
rELAYs AND MOTOr CONTrOL
K1 => Opening command
K2 => Closing command
K3 => Flashing light command
Q5 => TRIAC - Motor command in opening and closing
TOrQUE =>Tr2 - Electronic regulator for motor torque
Power can be controlled by rotating the TORQUE trimmer – this changes the output voltage
on motor ends (more power is delivered to the motor by rotating the trimmer clockwise).
Actually, the motor is always turned on at full power regardless the trimmer position (to
guarantee the starting in all the condition) and, then, after 3seconds, the torque control is
activated.
LOW sPEED =>Tr1 - Electronic regulator for low speed on approach
If DIP9 is turned OFF, the low speed on approach can be controlled by rotating the LOW
SPEED trimmer. The low speed is activated when the gate is 0.50-0.60 meters away from
the complete closed or open position.
ELECTrONIC BrAKE
If DIP10 is turned ON, a HARD electronic brake will be active.
If DIP10 is turned OFF, a SOFT electronic brake will be active.
GrADUAL sTArT
If DIP11 is turned ON, a gradual movement will be enabled for 1second upon each starting.
In case of an obstacle is detected by any safety inputs (photocell, safety strip or encoder), the
gradual start is bypassed for the time being to guarantee a more prompt and safe reaction.
POINT C
- MOTOr rOTATION DIrECTION CHECK
This operation is meant to help the installer during the installation and for further future
controls.
1 - Unlock the operator with the Manual Release, slide the leaf open about halfway and lock
the operator again.
2 - Turn
DIP1 to ON
position, LED DL1 starts blinking
3 - Press and hold the
PrOG.Button
, the gate will open or close. Release the button and
the gate will stop. Press and hold again, the gate will move in the opposite direction.
The S1 control board has two movement leds
- DL6 the GREEN led for OPENING
- DL7 the RED led for CLOSING
When you press and hold the PROG.Button, if the gate opens with the green led on then
you may proceed to step 4.
If the gate moves in the wrong direction compared with the movement leds:
- turn OFF the main AC power
- reverse the V and W motor cables position (the blue motor cable must be always in the
U position)
- reverse the limit switch wires marked LSO and LSC
- turn ON the main AC power and check again the motor direction
4 - After 2 seconds motor starting and for the next 6 seconds motor working,
the torque
control
is automatically activated. Set the motor torque by the TORQUE Trimmer which
varies the output voltage to the head of the motor (turn clockwise to increase torque).
5 - After other 6 seconds motor working, the
low speed control
is automatically activated
(DIP9 OFF). Set the motor low speed by the LOW SPEED Trimmer to select the gate
leaf low speed in approaching.
6 - Press and hold the PROG.Button to close completely the gate. Turn DIP1 to OFF, the
RED led DL1 will stop blinking.
During Point C procedure, safety devices (photocells and safety strip), stop button
and encoder input are not active.
(#) In Point D and Point E procedures, all of them will be active, so they must be properly
installed and connected to the control board. Any changing of the safety devices input state,
will stop the Point D and Point E procedure that must be repeated from the beginning.
POINT D
- PrOGrAMMING (#)
1 - The gate must be fully closed.
2 - Turn
DIP2 to ON
position, LED DL1 starts blinking
3 -
Press PrOG.Button
, motor opens.
4 - Once reached the open position, the open limit switch will cut out motor and the gate
travelling will be stored. The gap of time between now (stop of motor) and the next
pressing of the PROG.Button (see step 5 below) will be then stored as waiting time for
Automatic Closing feature.
5 -
Press PrOG.Button
, gate closes and the Automatic Closing time is stored (see DIP3
function to enable or disable the Automatic Closing feature).
6 - The LED DL1 will turn OFF, signalling exit from the Point D procedure.
Closing of the gate will be carried out at normal speed and only on approaching total
closing at low speed (depending on the adjustment of LOW SPEED trimmer).
7 - When the gate leaf reaches the close limit switch plate, the motor stops.
8 -
Turn DIP2 to Off
position.
IN CASE OF PLUS OPERATORS EQUIPPED WITH ENCODER, THE DIP7 MUST BE
TURNED ON DURING THE PROGRAMMING PROCEDURES.
POINT E
- PrOGrAMMING Of PEDEsTrIAN OPENING (#)
1 - The gate must be fully closed.
2 - Turn
DIP2 to ON
position, the LED DL1 starts blinking quickly
3 - Immediately, turn also
DIP1 to ON
position, the LED DL1 starts blinking slowly
4 - Press the pedestrian pushbutton
PED.Button
, the gate opens
5 - When the gate leaf is opened enough for the pedestrian crossing, press the pedestrian
pushbutton
PED.Button
to stop the travel (thus defining the opening stroke of the motor).
The gap of time between now (stop of the motor) and the next pressing of the PROG.
Button (see step 6 below) will be stored as waiting time for Pedestrian Automatic Closing
feature.