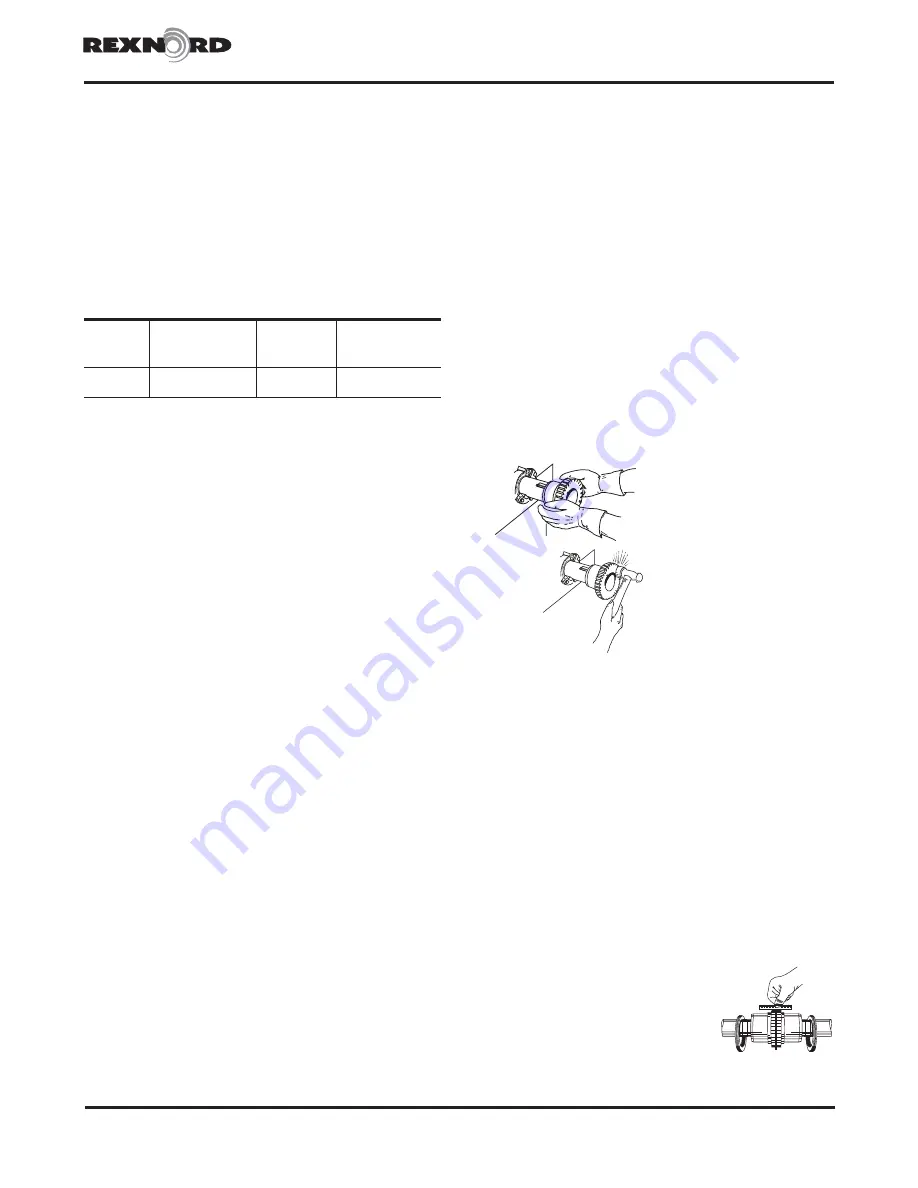
Falk
™
Drive One
®
Enclosed Gear Drives
•
Owners Manual
Type D Series
•
Sizes M1130 thru M1210
(Page 5 of 27)
Rexnord Industries, LLC, 3001 W. Canal St., Milwaukee, WI 53208-4200
168-050
Telephone: 414-342-3131 Fax: 414-937-4359
January 2019
e-mail: [email protected] web: www.rexnord.com
Supersedes 04-11
(PN 2124650)
thrust plate retaining ring and thrust plate, install backing
bolt, and reinstall thrust plate with retaining ring. Remove
bushing nut retaining ring. Install removal bolt in thrust
plate and tighten against backing bolt to release drive
from driven shaft (insert screwdriver in thrust plate key
slot to engage hollow shaft keyway to prevent thrust plate
rotation while tightening removal bolt).
7. Prepare drive for lifting by disconnecting the torque arm.
8. Slide the drive from the bushing. The bushing can be
left in place or removed as required. If bushing will not
slide off the shaft, insert a small prybar into the split of
the bushing and pry the split open slightly to loosen the
bushing and remove from the shaft.
Bushing
Size
Removal Bolt Size &
Minimum Length
Max Tightening
Torque
Nm (lb-ft)
Backing Bolt Size
& Max Length
190-200 mm
M30 x 3.5 x 200 mm
1355 (1000)
M24 x 3 x 45 mm
7.50-8.00 inch 1.500-6UNC x 7.50 inch
1125 (830)
1.250-7UNC x 3.00 inch
Taper Bushing – Sizes M1200 & M1210
Driven shafts are retained on M1200 & M1210 drives with
a thrust plate and three cap screw arrangement. With
the driven shaft keyway at the 12 o’clock position, slide
bushing onto the driven shaft, flange end first, and position
the keyway slot over the shaft keyway. The bushing may
have to be opened slightly to assist in installation. Insert a
screwdriver into the slot in the bushing and very lightly pry
open until the bushing slides onto the shaft. Insert the drive
key furnished with the bushing into the shaft keyway.
Installation of Shaft-Mounted Drives
Sizes M1200 M1210
1. Before lifting the drive into position, rotate the high-
speed shaft until the hollow shaft keyway will be in
position to line-up with the driven shaft key.
2. Lift the drive into position and slide onto the drive shaft
taking care that the driven shaft key seats into the hollow
shaft keyway. DO NOT hammer or use excessive force.
3. Align three holes in hollow shaft thrust plate with tapped
holes in end of driven shaft. Insert fasteners through
thrust plate and engage tapped holes in driven shaft
one to two turns by hand to ensure that fasteners are
not cross-threaded.
4. Tighten fasteners to the torque vales (± 10%) listed below:
M24 x 3 – 640 Nm (470 lb-ft) for metric-based bushing
bores.
1.250-7UNC – 1400 Nm (1060 lb-ft) for inch-based
bushing bores.
5. Re-install low-speed shaft cover.
Removal of Shaft-Mounted Drives
Sizes M1200 & M1210
1. Remove low-speed shaft cover.
2. Remove three thrust plate fasteners, retaining ring and
thrust plate from the hollow shaft.
3. Select the backing bolts from the table above and install
them into the three threaded holes in the end of the
driven shaft. The head of the backing bolts provides a
working surface for the removal bolts.
4. Re-insert the thrust plate and retaining ring into the hollow
shaft and select the removal bolts from the table above.
5. Thread three removal bolts into the thrust plate until they
contact the backing bolt heads.
6. Tighten the removal bolts equally in stages to the torque
indicated in the table above. After torquing the bolts, as
instructed, strike the bolts sharpy with a hammer and re-
torque the bolts if separation of the drive from the driven
shaft did not occur. Repeat this procedure, re-torquing
the bolts after each blow, until separation occurs.
7. Prepare drive for lifting by disconnecting the torque arm.
8. Slide the drive from the bushing. The bushing can be
left in place or removed as required. If bushing will not
slide off the shaft, insert a small prybar into the split of
the bushing and pry the split open slightly to loosen the
bushing and remove from the shaft.
Shaft Connections
WARNING
: Provide suitable guards in accordance with
local and national standards.
COUPLING CONNECTIONS
— The performance and
life of any coupling depends largely upon how well the
coupling is installed and serviced. Refer to the coupling
manufacturer’s manual for specific instructions.
CORRECT METHOD
Heat interference-fitted hubs,
pinions, sprockets or pulleys to
a maximum of 135°C (275°F)
and slide onto gear drive shaft.
INCORRECT METHOD
DO NOT drive coupling hub,
pinion, sprocket or pulley onto
the shaft. An endwise blow
on the shaft/coupling may
damage gears and bearings.
FALK COUPLINGS
— (Except fluid type) Detailed
installation manuals are available from the Factory, your
local Rexnord representative or distributor — just provide
size and type designations stamped on the coupling.
For lubricant requirements and a list of typical lubricants
meeting Rexnord specifications, refer to appropriate
coupling service manual.
FALK FLANGED TYPE RIGID COUPLINGS
— These are
typically used on drives with vertical output shafts. The
low-speed shaft extension ends of the solid vertical shaft
drives are drilled and tapped to accommodate coupling
keeper plates. Tightening torques for fastener, including
keeper plate fasteners are listed in Table 4, page 6.
FALK FLUID COUPLINGS
— Refer to the installation
manual furnished with the Falk fluid coupling for installation
and startup instructions. For Alignment-Free drives, refer to
Appendix D.
GAP AND ANGULAR ALIGNMENT
— If possible, after
mounting coupling hubs, position the driving and driven
equipment so that the distance
between shaft ends is equal to the
coupling gap. Align the shafts by
placing a spacer block, equal in
thickness to required gap, between
hub faces, as shown at right, and
also at 90° intervals around the hub.
Check with feelers.
– CAUTION –
DO NOT HAMMER
Steelflex
®
Illustrated