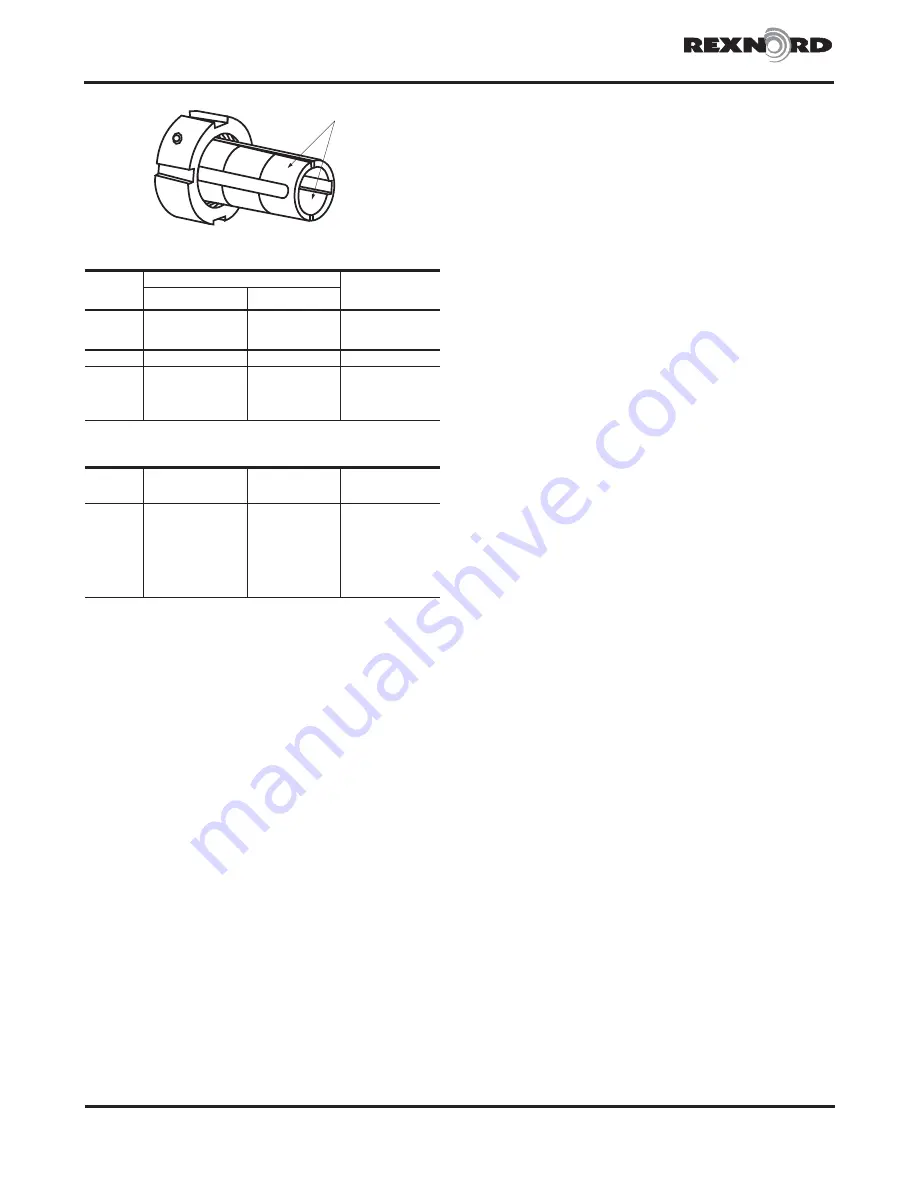
Owners Manual
•
Falk
™
Drive One
®
Enclosed Gear Drives
(Page 4 of 27)
Type D Series
•
Sizes M1130 thru M1210
168-050
Rexnord Industries, LLC, 3001 W. Canal St., Milwaukee, WI 53208-4200
January 2019
Telephone: 414-342-3131 Fax: 414-937-4359
Supersedes 04-11
e-mail: [email protected] web: www.rexnord.com
(PN 2124650)
torque value indicated in Table 3. If the required
torque cannot be measured, an approximation can
be made using Table 3A. The full weight should be
applied to the wrench handle in a horizontal position.
For example, to achieve the required tightening
torque for an M1180 bushing nut a 85 kg person
would have to apply all of his/her weight to a wrench
handle 950 mm from the nut, (a 190 lb. person
would have to apply all his/her weight to a wrench
handle 3 feet from the nut). Apply Loctite
®
243 or
equivalent to threads of the setscrew. Tighten the
setscrew to 10 Nm (90 lb-in). For drives subjected to
vibratory conditions, refer to Step c.
b.
OPTIONAL TA BUSHING NUT TIGHTENING
—
When the required tightening torque of the TA
bushing nut can not be measured at the low-speed
shaft, the torque-multiplying characteristic of the
drive can be utilized. Rotating the high-speed
shaft of the drive while holding the TA bushing nut
stationary will allow a large torque to be reached. Fix
the TA bushing nut by securing a spanner, chain or
pipe wrench to the nut. Allow the wrench to contact
a surface that will hold the force when tightening.
WARNING
: Make sure the wrench will not slip and
cause damage or injury.
Determine the proper rotation of the high-speed
shaft to achieve tightening of the stationary nut. If
the drive is equipped with a backstop, verify that
the backstop will allow the necessary rotation, or
remove the backstop. Find the torque to apply to the
Table 3 — Wrench Type and Bushing Nut
Tightening Torque
Drive
Size
Wrenches
Nut
Tightening Torque
Nm (lb-ft)
GearWrench
Williams
M1130
81858
474B
380 (280)
M1140
81858
474B
450 (332)
M1150
81858
474B
450 (332)
Ridgid Tool
Williams
M1160
92685
«
CT-15
«
520 (384)
M1170
92685
«
CT-15
«
630 (465)
M1180
92685
«
CT-15
«
770 (568)
M1190
92685
«
CT-15
«
900 (664)
★
These are chain wrenches where standard spanner wrenches are not available.
Table 3A — Equivalent Tightening Torque
‡
Drive
Size
Required Torque
Nm (lb-ft)
Person’s Weight
kg (lbs)
Length of Handle
mm (ft)
M1130
380 (280)
80-100 (180-220)
460-610 (1.5-2)
M1140
450 (332)
80-100 (180-220)
610-915 (2-3)
M1150
450 (332)
80-100 (180-220)
610-915 (2-3)
M1160
520 (384)
80-100 (180-220)
610-915 (2-3)
M1170
630 (465)
80-100 (180-220)
915-1220 (3-4)
M1180
770 (568)
80-100 (180-220)
915-1220 (3-4)
M1190
900 (664)
80-100 (180-220)
1220-1525 (4-5)
‡ If a torque wrench is not available, the torque can be approximated by
applying the given weight at the given distance from the nut.
DO NOT apply ANTI-SEIZE
on these areas.
high-speed shaft by dividing the tightening torque
indicated in Table 3 by the drive’s ratio (Torque ÷
Ratio). Apply the calculated torque to the high-
speed shaft or coupling using a spanner, chain or
pipe wrench. Be careful not to damage the usable
length of the high-speed shaft. Remove the fixed
wrench from the TA bushing nut and reassemble the
backstop if necessary.
WARNING
: Never use the prime mover to produce
the required torque. This could result in severe
personal injury or damage.
Apply Loctite 243 or equivalent to threads of
setscrew. Tighten the setscrew to 10 Nm (90 lb-in)
on the bushing nut. For drives subjected to vibratory
conditions refer to Step c.
c.
DRIVES SUBJECTED TO VIBRATORY
CONDITIONS
— Extra precautions should be
taken for drives subjected to vibratory conditions.
With the nut of the TA bushing tightened to the
specified torque, locate the setscrew hole in the
nut of the bushing assembly. Using a 6 mm (15/64
inch) diameter drill, create a dimple in the outside
diameter of the bushing flange by drilling through
the setscrew hole in the nut. Apply Loctite 243 or
equivalent to threads of setscrew and tighten into
bushing nut.
d.
DRIVES USING THRUST PLATE KIT
— Install
thrust plate and thrust plate retaining ring in hollow
shaft. Coat four to five engaging threads of retention
fastener with Loctite 222 or equivalent (low-strength)
thread locking compound and thread into driven
shaft end until snug tight. Reinstall shaft cover.
Removal of Shaft-Mounted Drives
Sizes M1130 - M1190
WARNING
: Lock out power source and remove all external
loads from drive before servicing drive or accessories.
1. Drain the lubricant from the drive.
2. Remove safety guards and belts (if so equipped).
Remove hollow shaft cover if thrust plate kit is used.
3. Remove motor and motor mount (if so equipped).
4. Remove backstop (if so equipped).
WARNING
: Drive must be supported during removal
process. Use a sling and take up the slack before
proceeding.
5. Remove the setscrew(s) on the bushing nut, which
is located at the output end of the hollow shaft. On
drives using the thrust plate kit, remove the driven shaft
retention fastener.
6. Use a spanner, pipe or chain wrench to loosen
the bushing nut. Initially the nut will freely rotate
counterclockwise approximately 180° as the nut moves
from the locked position to the removal position. At this
point, anticipate resistance which indicates unseating
of the bushing. Continue to rotate the nut until it is free
from the hollow shaft. If unable to release the drive from
the driven shaft with the bushing nut, the thrust plate
kit using a backing bolt (threaded into the driven shaft
tapped hole) and removal bolt (threaded into the thrust
plate tapped hole) may be used to release the drive
from the driven shaft. Refer to Appendix G for backing
and removal bolt sizes (user supplied). To use, remove