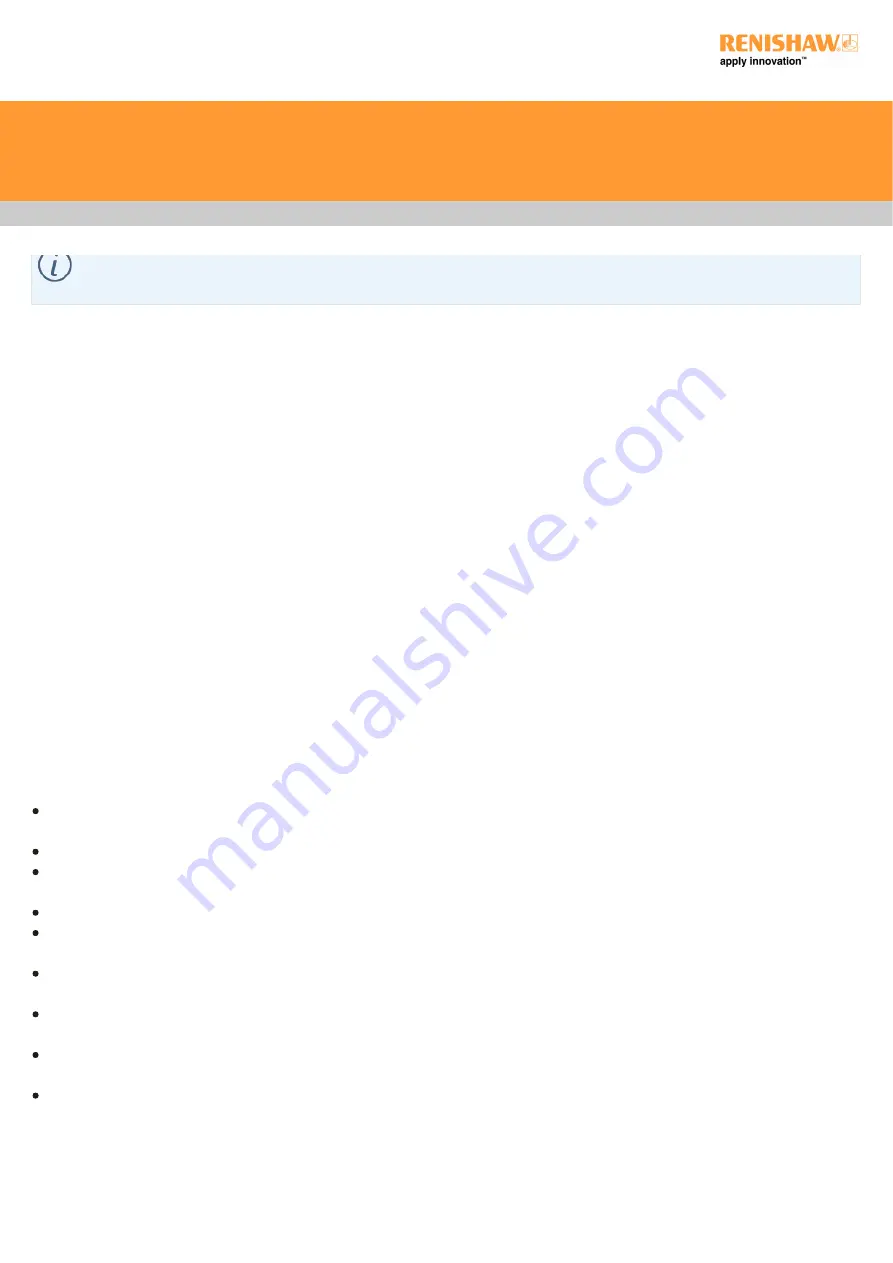
environment. If a scale error occurs, it is now necessary to re-initialise the installation. This is because of the possibility of lost scale
counts and therefore metrology being effected.
Timing out during moves or scans
Symptom
The CMM takes a long time to complete a commanded move. The event should be reported by the application software as a ‘move timeout
fault' or similar wording. ﴾The condition is reported to the application software by the controller's setting of the ‘time‐out during move or
scan‘ flag in a status report﴿.
Possible causes, tests, cures
This is similar to the ‘poor positioning accuracy' fault described earlier in this chapter. In particular, the drive friction level and the positional
tolerance setting are important factors.
Check that the friction levels have not deteriorated since the machine was commissioned.
The positioning tolerance defines the maximum allowed position error at the end of a move. If this is made too small for the CMMs servo
capabilities, it will cause time‐out failures during moves. Adjust it using the ‘Enter positional tolerance‘ command 308.
Cannot start a move
Symptom
The machine does not respond when given a move command. The controller returns either the ‘cannot start move' or the ‘illegal parameter'
status flag with the normal ‘action complete' flag.
Possible causes, tests, cures
The ‘illegal parameter‘ flag indicates that the move command may contain a parameter which is outside its acceptable range or is not
logical. See the definition of the move command.
The servo motors are not engaged, engage the motors, see above.
Physical restraint of the CMM causing an immediate stall condition (e.g. unreported failure of the air supply to air bearings). Check CMM
mobility, rectify as required.
If a joystick unit is attached, the controller must be in DCC mode, not the manual joystick mode.
The controller is not in ‘HOLD' state, e.g. it may be completing a previous command, or it may be in joystick mode and responding to a
joystick deflection. Wait for the action complete flag from the previous command, or send an Abort command to ensure termination.
The probe is open/deflected. Use the joystick “probe disable” switch or the ‘probe open override' ﴾command number 310﴿ to escape from
the deflecting surface - remember to turn the override off afterwards.
The probe is reported as ‘deflected' even when not in contact with a surface. Test/cure: check probe calibration – has the configuration
changed since last qualification, if so correct and null the scanning probe with command number 288.
All inner limit switches must be closed and the machine must be inside all soft limits, if these are enabled. limit switch operation can be
over-ridden by use of command number 311.
The analogue probe signal converter within the UCC2 reports an error. To resolve this problem the system must be rebooted.
Cannot start a scan
Symptom
When a scan command is sent to the controller, it does not begin the search for the part surface. If this process does not start it returns either
UCC2 and UCC2-2 installation guide
www.renishaw.com
Issued 07 2021
57