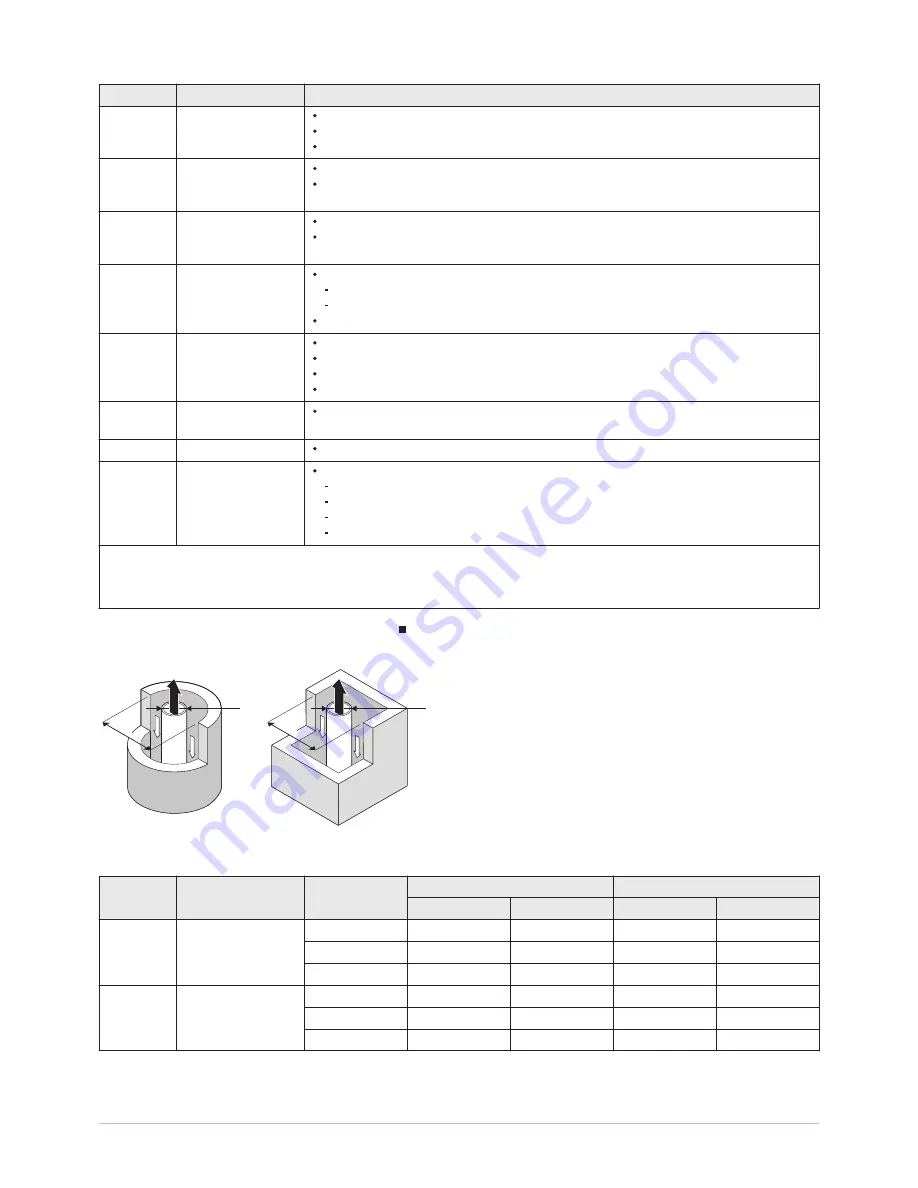
Type
Version
Description
B33
Open
Without down-draught diverter.
Joint flue gas discharge via the roof.
Flue gas discharge rinsed with air, air from the installation area (special construction).
C13
Closed
Discharge in the outside wall.
Inlet opening for the air supply is in the same pressure zone as the discharge (e.g. a
combined outside wall feed-through).
C33
Closed
Flue gas discharge via the roof.
Inlet opening for the air supply is in the same pressure zone as the discharge (e.g. a
concentric roof feed-through).
C43
(2)
Closed/cascade
Joint air supply and flue gas discharge duct (CLV system):
Concentric.
Eccentric: air supply from the shaft.
Cascade overpressure
C53
Closed
Closed unit.
Separate air supply duct.
Separate flue gas discharge duct.
Discharging into various pressure areas.
C63
Closed
This type of unit is supplied by the manufacturer without a supply and discharge sys
tem.
C83
(3)
Closed
The appliance can be connected to a semi-CLV system (with common flue gas outlet).
C93
(4)
Closed
Air supply and flue gas discharge duct in shaft or ducted:
Concentric.
Eccentric: air supply from the shaft.
Flue gas discharge via the roof.
Inlet opening for the air supply is in the same pressure zone as the discharge.
(1) Also pressure class P1
(2) EN 15502-2-1: 0.5 mbar suction due to depression
(3) 4 mbar depression can occur
(4) See table for minimum dimensions of shaft or duct
Shaft dimensions
Fig.12 Minimum dimensions of shaft or duct
AD-3000330-01
□
D
Ø
D
Tab.10 Minimum dimensions of shaft or duct
Type
Version
Diameter (D)
Without air supply
With air supply
Ø duct
□ duct
Ø duct
□ duct
C93
Rigid
60 mm
110 mm
110 x 110 mm
120 mm
110 x 110 mm
80 mm
130 mm
130 x 130 mm
140 mm
130 x 130 mm
100 mm
160 mm
160 x 160 mm
170 mm
160 x 160 mm
C93
Flexible
60 mm
110 mm
110 x 110 mm
120 mm
110 x 110 mm
80 mm
130 mm
130 x 130 mm
145 mm
130 x 130 mm
100 mm
160 mm
160 x 160 mm
170 mm
160 x 160 mm
6 Installation
24
123157 - v.06 - 24022015