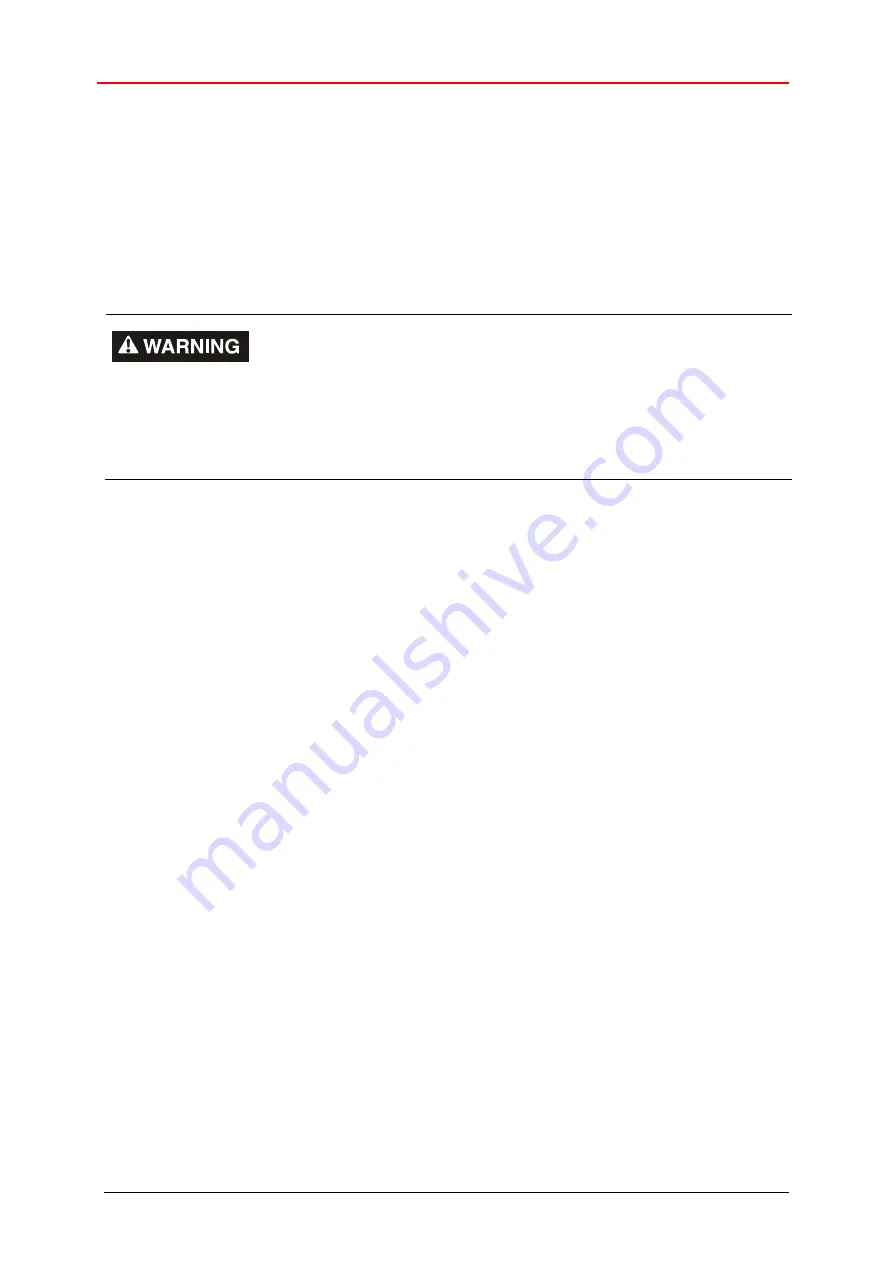
Integration of the measuring system into the safety program
TR-Electronic GmbH 2012, All Rights Reserved
Printed in the Federal Republic of Germany
Page 46 of 56
TR - ECE - BA - GB - 0095 - 19
05/30/2018
7 Integration of the measuring system into the safety program
This chapter describes the necessary steps for the integration of the measuring
system into the safety program and is not related to a certain control unit. The exact
process is control specific and must be taken from the system documentation of the
control unit manufacturer.
7.1 Prerequisites
Danger of deactivation of the fail-safe function through incorrect
configuration of the safety program!
The safety program must be created in conjunction with the system
documentation provided by the control unit manufacturer.
It is essential to observe and comply with the information and
instructions provided in the system documentation, particularly the
safety instructions and warnings.
7.2 Hardware configuration
Create a new project
Perform the general hardware configuration (CPU, Voltage supply)
Provide a digital input module, in order to be able to carry out the operator
acknowledgment
Install the GSDML file belonging to the measuring system
Defining the properties of the hardware configuration
- Access protection via password allocation
- Ethernet (IP-Address, Subnet mask, Device Name, Synchronization)
- I/O modules (Operating mode, F-Parameter, Diagnosis, Arrangements for the
operator acknowledgment)
7.3 Parameterization
Parameterize device specific
iParameter
in the non-safety module,
also see starting from page 43 and 45
Define PROFIsafe specific
F-Parameter
in the safety module,
also see starting from page 41 and 45
Save and if necessary compile hardware configuration