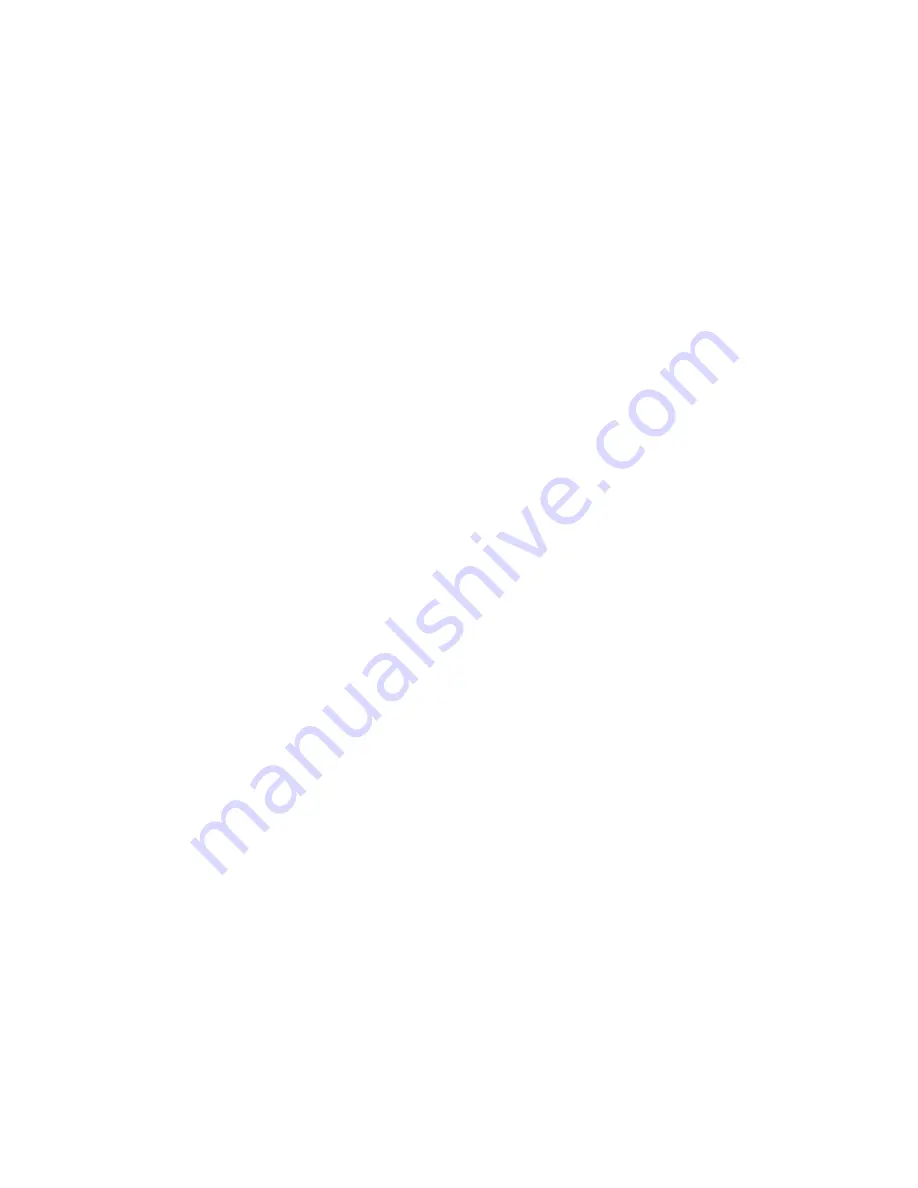
LCD INSTALLATION AND OPERATION INSTRUCTIONS
Page 15
CAUTION: A temperature rise outside of the range
listed in Table 7 indicates that the fl ow rate through
the heat exchanger is incorrect which will damage
the heat exchanger voiding the warranty! The
maximum allowable temperature rise is 35°F,
19.4°C
.
The maximum allowable fl ow rate through a LCD
boiler with copper heat exchanger is 92 GPM,
5.8 L/s
on 225-1200 models and 115 GPM,
7.3 L/s
on 1480 to 2300 models. The cupro-nickel heat
exchanger allows for 100 GPM,
6.3 L/s
on 225 to
1200 models and 125 GPM,
7.9 L/s
on 1480 to 2300
models.
Low Water Cutoff
If a boiler is installed above any radiation elements it
must be fi tted with a low water cutoff device.
Refer to wiring diagram supplied with the boiler/water
heater for proper wiring connections.
Expansion Tank & Air Separator
An expansion tank or other means to control thermal
expansion must be installed in the heating system. An
expansion tank must be installed close to the boiler on
the suction side of the pump. An air scoop and
automatic air vent must also be installed to eliminate air
trapped in the system.
Primary/Secondary Piping
Boilers connected to heating systems using zone valves,
zone pumps, or systems that have excessive fl ow rates
or return water temperatures less than
125°F
,
52°C
must be isolated from these systems to protect the boiler.
Variable Water Flows
Figure 11 shows a typical primary/secondary piping
system. A dedicated pump is used to maintain a
constant water flow through the boiler. This boiler
pump is sized to overcome the head loss of the boiler
a n d n e a r p i p i n g w h i l e s u p p l y i n g t h e f l ow ra t e
required to maintain the desired temperature rise
across the boiler heat exchanger. The system pump is
sized to provide the required fl ow to the heating system.
The boiler piping connections to the heating system
piping must not be more than
12 in
,
305 mm
apart to
ensure zero pressure drop. See Figure 11.
Low Return Water Temperatures
To prevent the problems associated with condensation
of the products of combustion due to low return water
temperatures a primary/secondary piping system with
a bypass and bypass valve must be installed, see Figure
12. The bypass and bypass valve must be sized the
same as the boiler piping. A balancing valve must
also be installed in the supply side of the boiler piping
downstream of the bypass. The balancing valve
should be adjusted to divert some of the heated
discharge water into the return water until the required
inlet water temperature is achieved. The primary and
secondary pumps should be sized to provide the
required fl ow through each system. The boiler piping
connections to the heating system piping must not be
more than
12 in
,
305 mm
apart to ensure zero pressure
drop. See Figure 12.
Multiple Boiler Systems
Systems using multiple boilers can also be installed
using a primary/secondary manifold system, Figure 13.
Piping For Use With Cooling Units
The boiler, when used in connection with a refrigeration
system, must be installed so the chilled medium is piped
in parallel with the boiler. Appropriate valves must be
used to prevent the chilled water from entering the
boiler.
When a boiler is connected to a heating coil that may
be exposed to refrigerated air from an air handling
device, the piping system must be equipped with fl ow-
control valves or some other automatic means of
preventing gravity circulation of the boiler water during
the cooling cycle.