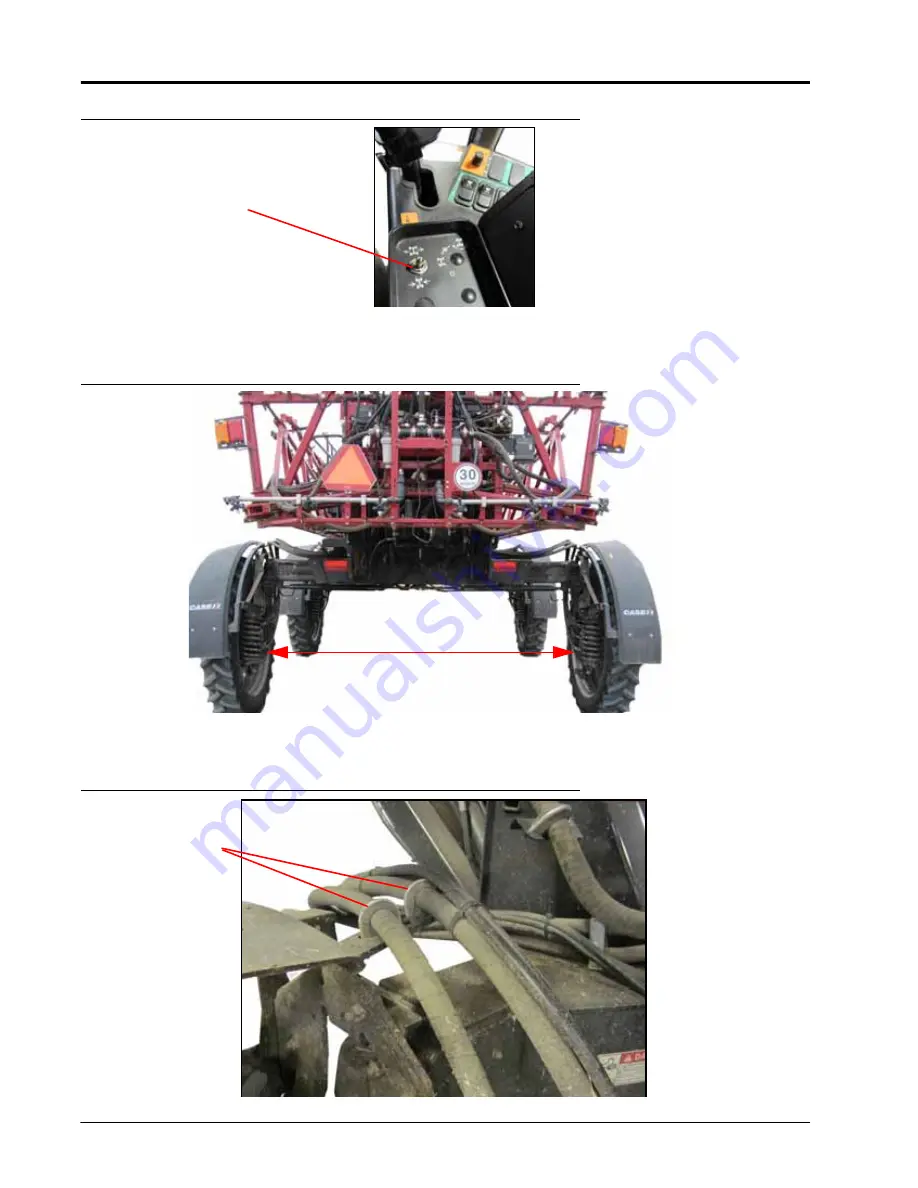
C
HAPTER
3
16
CAN Sidekick Pro Injection for Case IH 3/4XXX Installation and Operation Manual
FIGURE 11. Axle Extension Toggle Switch
7. Extend the axles to the outer most position (typically 152”-160”).
FIGURE 12. Fully Extended Axles
8. At the rear mud shields, loosen hydraulic hose fastener clamps for rear wheel drive motor hoses.
FIGURE 13. Drive Motor Hose Clamps
Axle Extension Switch
Fully Extended
Hose Clamps
Содержание Sidekick Pro
Страница 12: ...CHAPTER 2 10 CAN Sidekick Pro Injection for Case IH 3 4XXX Installation and Operation Manual ...
Страница 84: ...CHAPTER 7 82 CAN Sidekick Pro Injection for Case IH 3 4XXX Installation and Operation Manual ...
Страница 88: ...CHAPTER 8 86 CAN Sidekick Pro Injection for Case IH 3 4XXX Installation and Operation Manual ...
Страница 89: ...CHAPTER 9 System Diagrams Electrical 87 CHAPTER9SYSTEM DIAGRAMS ELECTRICAL Drawings start on next page ...
Страница 91: ...System Diagrams Electrical 89 SYSTEM DIAGRAMS FIGURE 2 Single Pump System Diagram ...
Страница 93: ...System Diagrams Electrical 91 SYSTEM DIAGRAMS PLUMBING FIGURE 4 Dual Pump Injection Plumbing ...
Страница 96: ...Index 94 CAN Sidekick Pro Injection for Case IH 3 4XXX Installation and Operation Manual ...