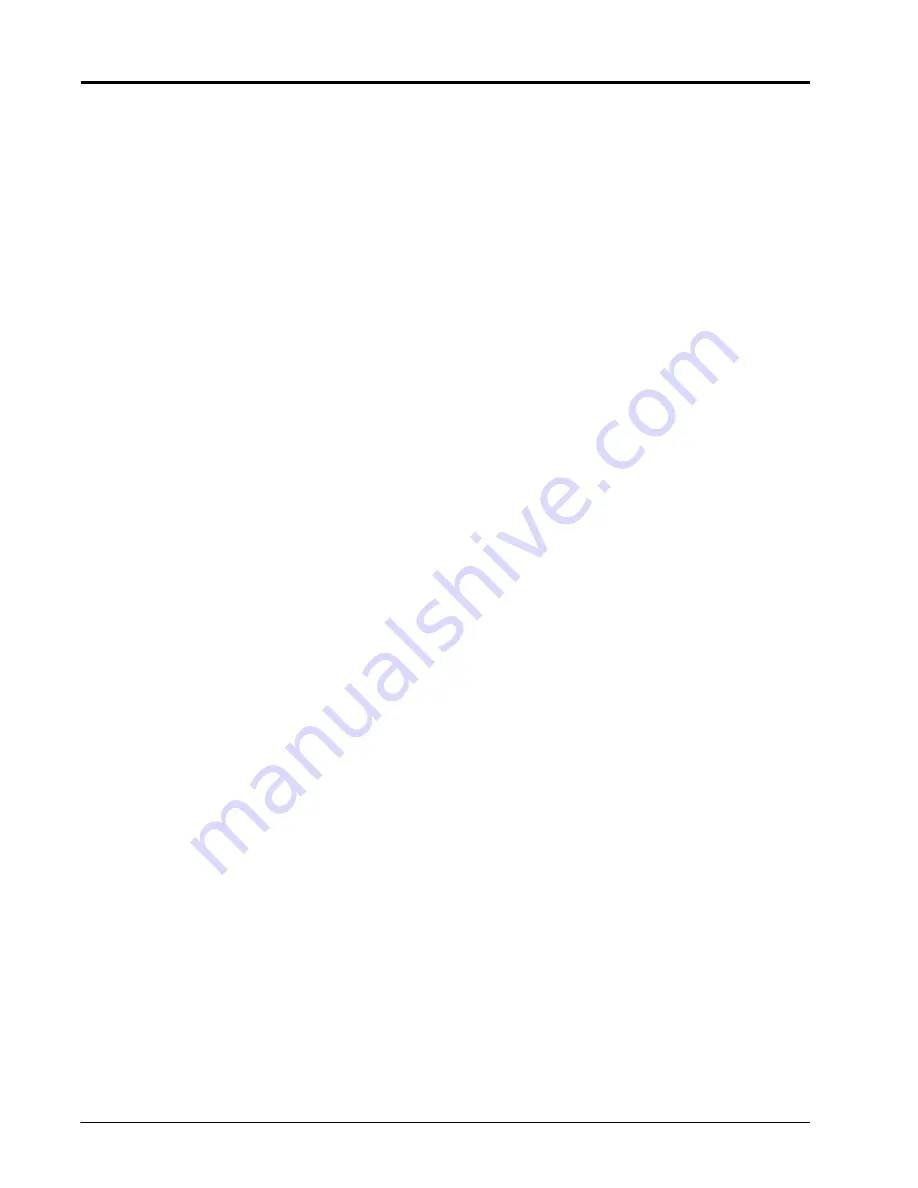
C
HAPTER
1
4
ISO Product Controller II and Hawkeye Operation Manual
• Sheared or flame cut edges
• Edges of machined surfaces
• Fastener threads or cap screw heads
• Ends of adjustable hose clamps
Routing should not allow hoses to:
• Hang below the unit
• Have the potential to become damaged due to exposure to the exterior environment. (i.e. tree limbs, debris,
attachments)
• Be placed in areas of or in contact with machine components which develop temperatures higher than the
temperature rating of hose components
• Hoses should be protected or shielded if it needs to route near hot temperatures beyond hose component
specifications
Hoses should not have sharp bends
Allow sufficient clearance from machine component operational zones such as:
• Drive shafts, universal joints and hitches (i.e. 3-point hitch)
• Pulleys, gears, sprockets
• Deflection and backlash of belts and chains
• Adjustment zones of adjustable brackets
• Changes of position in steering and suspension systems
• Moving linkages, cylinders, articulation joints, attachments
• Ground engaging components
For hose sections that move during machine operation:
• Allow sufficient length for free movement without interference to prevent: pulling, pinching, catching or
rubbing, especially in articulation and pivot points
• Clamp hoses securely to force controlled movement to occur in the desired hose section
• Avoid sharp twisting or flexing of hoses in short distances
Protect hoses from:
• Foreign objects such as rocks that may fall or be thrown by the unit
• Buildup of dirt, mud, snow, ice, submersion in water and oil
• Tree limbs, brush and debris
• Damage where service personnel or operators might step or use as a grab bar
• Damage when passing through metal structures
• High pressure wash
IMPORTANT:
Avoid directly spraying electrical components and connections with high pressure water. High pressure water
sprays can penetrate seals and cause electrical components to corrode or otherwise become damaged. When
performing maintenance:
•
Inspect all electrical components and connections for damage or corrosion. Repair or replace
components, connections, or cable as necessary.
•
Ensure connections are clean, dry, and not damaged. Repair or replace components, connections,
or cable as necessary.
Содержание Hawkeye
Страница 1: ...ISO Product Controller II and Hawkeye Operation Manual P N 016 0171 584 H 01 19 E32470 Copyright 2019 ...
Страница 10: ...CHAPTER 1 viii ISO Product Controller II and Hawkeye Operation Manual ...
Страница 16: ...CHAPTER 1 6 ISO Product Controller II and Hawkeye Operation Manual ...
Страница 22: ...CHAPTER 2 12 ISO Product Controller II and Hawkeye Operation Manual ...
Страница 50: ...CHAPTER 4 40 ISO Product Controller II and Hawkeye Operation Manual ...
Страница 92: ...APPENDIX A 82 ISO Product Controller II and Hawkeye Operation Manual ...
Страница 95: ...P N 016 0171 584 H 85 FIGURE 3 Generic Cabling for Self Propelled Sprayer ...
Страница 97: ...P N 016 0171 584 H 87 FIGURE 5 Generic Cabling for Pull Type Sprayer with Existing Raven CAN ...
Страница 99: ...P N 016 0171 584 H 89 FIGURE 7 20 Spacing Generic Cabling ...
Страница 111: ...P N 016 0171 584 H 101 ...
Страница 112: ...APPENDIX D 102 ISO Product Controller II and Hawkeye Operation Manual ...
Страница 116: ...APPENDIX E 106 ISO Product Controller II and Hawkeye Operation Manual ...
Страница 120: ...APPENDIX F 110 ISO Product Controller II and Hawkeye Operation Manual ...
Страница 122: ...APPENDIX G 112 ISO Product Controller II and Hawkeye Operation Manual FIGURE 1 Hawkeye Screen Flow Tools Menu Softkey ...
Страница 125: ...P N 016 0171 584 H 115 FIGURE 4 Hawkeye Screen Flow Tally Registers and Diagnostics Menu Softkeys ...
Страница 127: ...P N 016 0171 584 H 117 FIGURE 6 Hawkeye Injection Screen Flow Product Setup Alarms and System Information ...
Страница 128: ...APPENDIX G 118 ISO Product Controller II and Hawkeye Operation Manual ...
Страница 134: ...APPENDIX H 124 ISO Product Controller II and Hawkeye Operation Manual ...