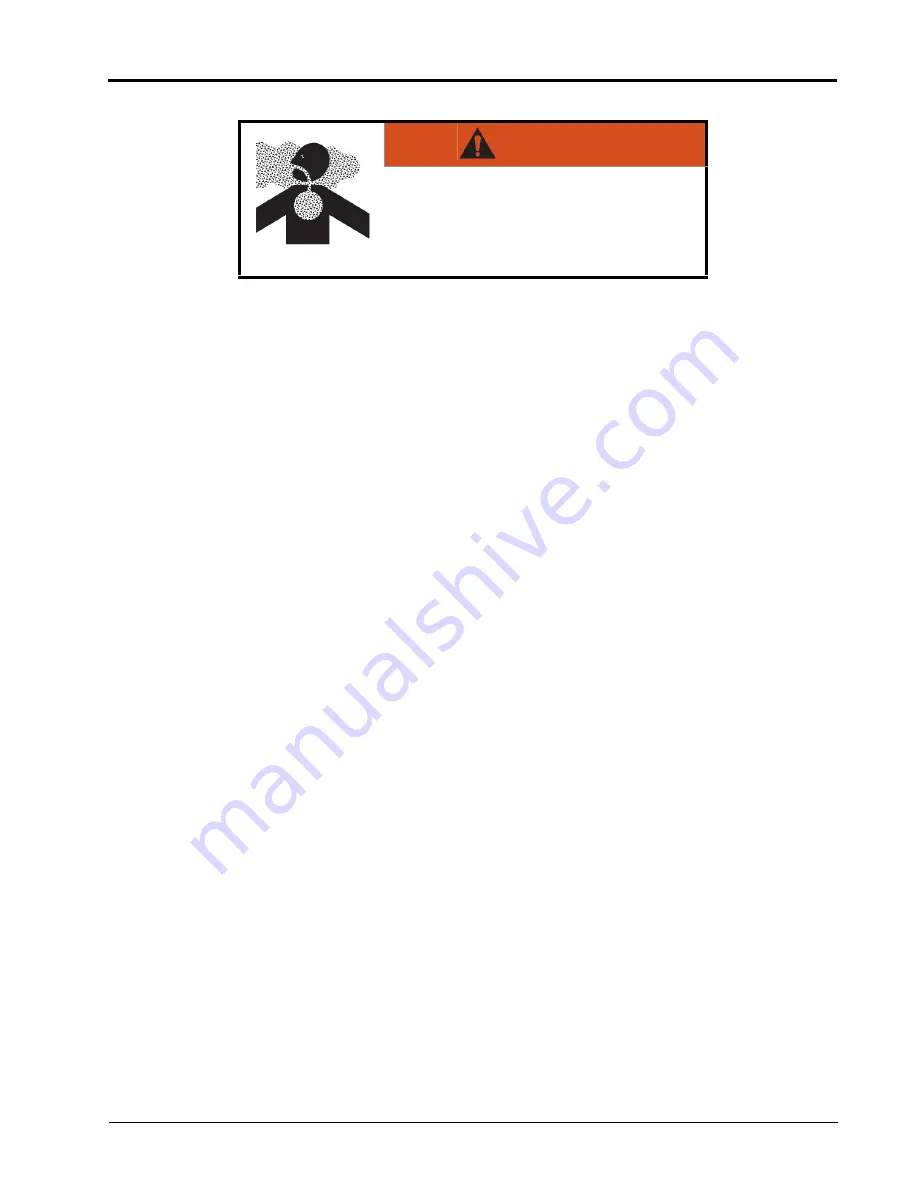
System Calibration: Functional Inspection
17
SYSTEM CALIBRATION
6. Toggle all section switches and the master switch.
7. While maintaining a safe distance away from any spray drift, visually check that all nozzle control valves are
pulsing with a uniform pattern. Adjacent nozzle control valves should alternate pulsing. If adjacent spray tips
are pulsing at the same time, refer to Chapter 8, Troubleshooting, for additional assistance.
8. On the UT, set nozzle PWM to 0% and Pump PWM to about 30% to close the nozzle control valves and
maintain a safe pressure in the boom.
9. Visually check that none of the nozzles are spraying or dripping. Refer to Testing for Leaks section on page 99
for additional assistance and troubleshooting if leaks are observed.
TURN COMPENSATION FEATURE
To verify the Turn Compensation feature is enabled and operating:
NOTE:
Complete the procedure outlined in the Nozzle Control Valve Function section on page 16 to validate
the nozzle control valve function prior to performing the following procedure.
Turn Compensation is automatically calibrated during the calibration wizard. If the feature is not
operating as described below, refer to the “Turn Compensation Calibration” section on page 26 for
assistance with calibrating the turn compensation feature if necessary.
1. Move the implement to an open area where the equipment may be driven in quick, tight turns.
2. Verify that the turn compensation feature is enabled.
3. Set the system to automatic mode and toggle the section and master switches to the on positions. Refer to
Chapter 5, Operation for additional assistance with operation of the nozzle control system.
4. For fertilizer applicators, keep the toolbar raised so it is easier to observe the stream from each nozzle.While
driving at a speed between 5 and 10 mph [8 and 16 km/h] and maintaining a safe working distance, observe
the inner-most and outer-most spray tips while the implement is turning sharply.
NOTE:
The nozzle PWM percent value may also be used to monitor the operation of nozzle control valves
across the spray boom. Refer to Chapter 7, Hawkeye Nozzle Control Valve Diagnostics, for additional
assistance with on-screen nozzle control valve diagnostics.
While turning, the nozzle control valves toward the outside of the corner should begin to output a
higher flow rate (higher PWM percent), while valves toward the inside of the corner should begin to
output a reduced flow rate (lower PWM percent) or may shut off. NCV diagnostics and performance
can be seen in the Performance Indicator on the PCII home screen or in the individual NCV
diagnostics pages. The difference between inner and outer flow rates will vary depending on machine
speed, turn rate, and implement width. Turn compensation can also be observed on the Diagnostics
Info page. Product Controller II ECU Yaw Rate will be zero while stationary. If turning clockwise, the
Product Controller II ECU Yaw Rate will be positive, if turning counter clockwise, the Product
Controller II ECU Yaw Rate will be negative.
5. If the operator is able to observe a difference in the spray pulsing, or the on-screen PWM percent, the turn
compensation feature is working correctly. If there is no difference between the PWM percent values across the
implement width, recalibrate the turn compensation feature and repeat the test.
WARNING
Equipment will begin spraying. Avoid inhaling
spray particulate and avoid direct contact with
any agricultural chemicals. Seek immediate
medical attention if symptoms of illness occur
during, or soon after, use of agricultural
chemicals, products, or equipment.
Содержание Hawkeye
Страница 1: ...ISO Product Controller II and Hawkeye Operation Manual P N 016 0171 584 H 01 19 E32470 Copyright 2019 ...
Страница 10: ...CHAPTER 1 viii ISO Product Controller II and Hawkeye Operation Manual ...
Страница 16: ...CHAPTER 1 6 ISO Product Controller II and Hawkeye Operation Manual ...
Страница 22: ...CHAPTER 2 12 ISO Product Controller II and Hawkeye Operation Manual ...
Страница 50: ...CHAPTER 4 40 ISO Product Controller II and Hawkeye Operation Manual ...
Страница 92: ...APPENDIX A 82 ISO Product Controller II and Hawkeye Operation Manual ...
Страница 95: ...P N 016 0171 584 H 85 FIGURE 3 Generic Cabling for Self Propelled Sprayer ...
Страница 97: ...P N 016 0171 584 H 87 FIGURE 5 Generic Cabling for Pull Type Sprayer with Existing Raven CAN ...
Страница 99: ...P N 016 0171 584 H 89 FIGURE 7 20 Spacing Generic Cabling ...
Страница 111: ...P N 016 0171 584 H 101 ...
Страница 112: ...APPENDIX D 102 ISO Product Controller II and Hawkeye Operation Manual ...
Страница 116: ...APPENDIX E 106 ISO Product Controller II and Hawkeye Operation Manual ...
Страница 120: ...APPENDIX F 110 ISO Product Controller II and Hawkeye Operation Manual ...
Страница 122: ...APPENDIX G 112 ISO Product Controller II and Hawkeye Operation Manual FIGURE 1 Hawkeye Screen Flow Tools Menu Softkey ...
Страница 125: ...P N 016 0171 584 H 115 FIGURE 4 Hawkeye Screen Flow Tally Registers and Diagnostics Menu Softkeys ...
Страница 127: ...P N 016 0171 584 H 117 FIGURE 6 Hawkeye Injection Screen Flow Product Setup Alarms and System Information ...
Страница 128: ...APPENDIX G 118 ISO Product Controller II and Hawkeye Operation Manual ...
Страница 134: ...APPENDIX H 124 ISO Product Controller II and Hawkeye Operation Manual ...