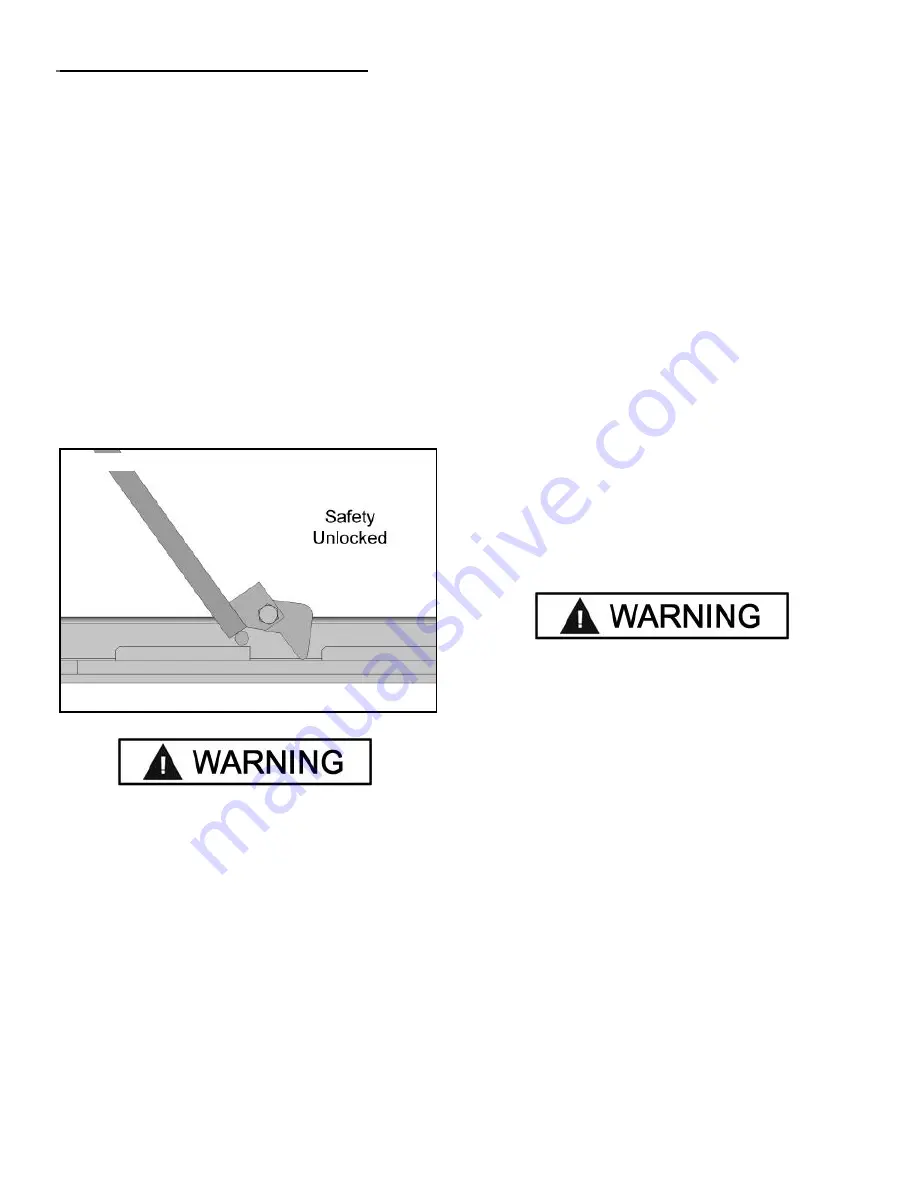
Lower the lift onto the nearest safety lock.
ALWAYS INSURE SAFETY LOCKS ARE ENGAGED
before entering work area.
Check to make sure safeties are engaged on the
SAME
safety lock position
BEFORE ENTERING
work
area.
To Lower Lift;
Clear area of personnel and tools above and below
before lowering lift.
Raise the lift until at least two inches to provide
adequate clearance for the saftey to operate.
Visually confirm that the safety bar has been raised
up off the safety locks. ( See Fig. 11.2 )
When lowering the lift PAY CAREFUL ATTENTION that
all personnel and objects are kept clear. ALWAYS keep
a visual line of site on the lift AT ALL TIMES. ALWAYS
make sure that all LOCKS are disengaged. If one of the
locks inadvertently locks on descent, the lift and/or vehi-
cle may disrupt causing personal injury or death.
Push the LOWERING handle until the lift starts to
descend. Stay clear of lift area. Ensure that both safeties
are not engaged.
Fully lower the lift and remove all lifting adapters
before driving vehicle away.
WEEKLY MAINTENANCE
Lubricate all rollers with general purpose oil or
WD-40.
Check all cable connections, bolts and pins to insure
proper
mounting.
Lubricate safety lock pivot points with general
purpose oil or WD-40.
MONTHLY MAINTENANCE
Check safety locks to insure they are in good
operating
condition.
Make a visual inspection of ALL MOVING PARTS
and check for excessive signs of wear
Replace ALL FAULTY PARTS before lift is put back
into
operation.
NEVER EXCEED THE RATED CAPACITY
of lift.
DO NOT USE LIFT
if any component is found to be
defective or worn.
NEVER OPERATE LIFT
with any person or
equipment
below.
ALWAYS STAND CLEAR
of lift when lowering or
raising.
ALWAYS INSURE SAFETY LOCKS ARE
ENGAGED
before entering work area.
NEVER LEAVE LIFT IN ELEVATED CONDITION
unless all safety locks are engaged.
19
Fig. 11.2
Содержание BendPak P-6
Страница 9: ...9 P 6 P 6F Main Assembly Views...
Страница 22: ...22...
Страница 23: ...23...
Страница 29: ...29...
Страница 30: ...Main Parts View 30...
Страница 31: ...31 Air Valve Parts List...