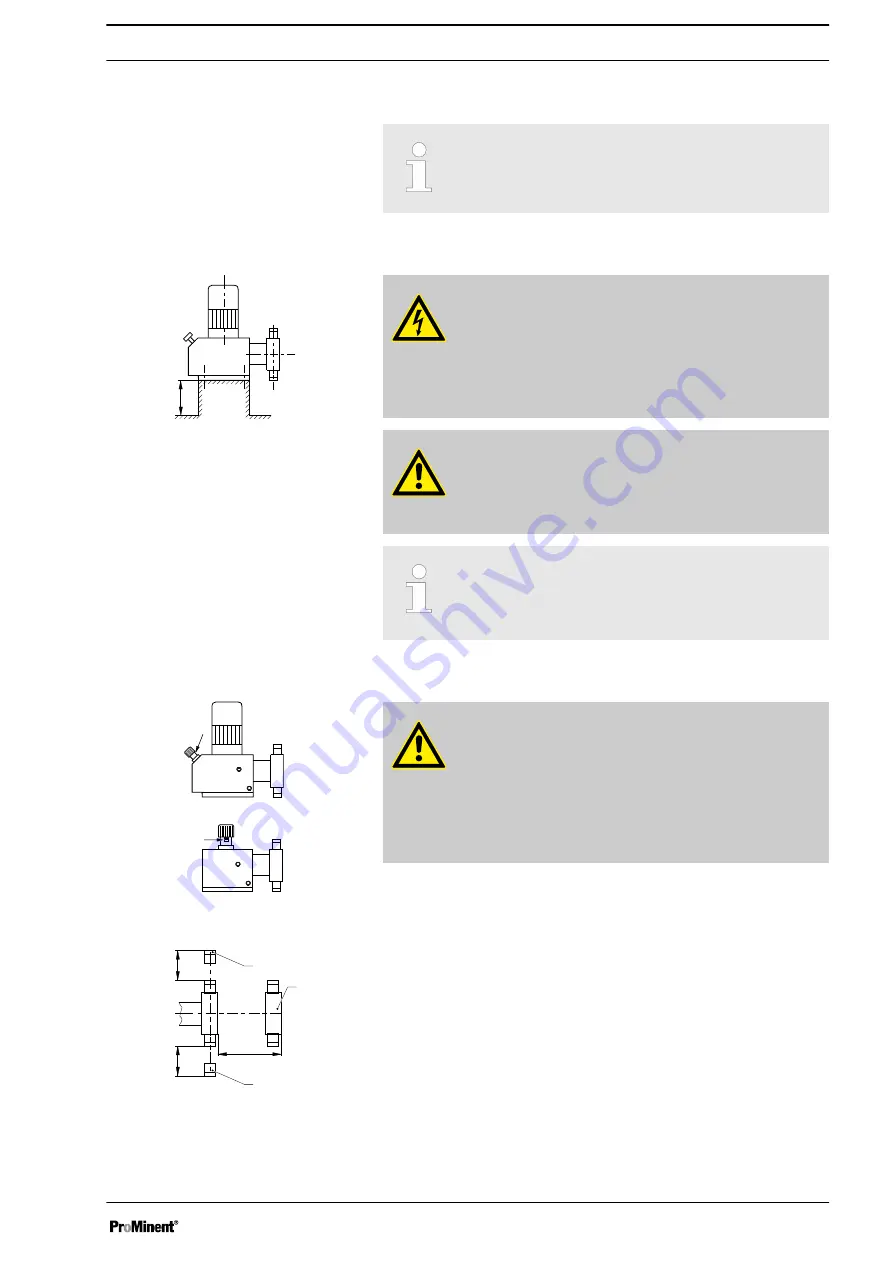
6
Assembly
Compare the dimensions on the dimension sheet and pump.
WARNING!
Danger of electric shock
If water or other electrically conducting liquids penetrate into
the drive housing, in any other manner than via the pump's
suction connection, an electric shock may occur.
–
Position the pump so that it cannot be flooded.
WARNING!
The pump can break through the base or slide off it
–
Ensure that the base is horizontal, smooth and perma‐
nently load-bearing.
Capacity too low
Vibrations can disrupt the liquid end valves.
–
The supporting floor must not vibrate.
CAUTION!
Danger from incorrectly operated or inadequately maintained
pumps
Danger can arise from a poorly accessible pump due to
incorrect operation and poor maintenance.
–
Ensure that the pump is accessible at all times.
–
Adhere to the maintenance intervals.
Position the pump so that control elements such as the stroke length
adjustment knob or the indicating dial A are easily accessible.
1
Discharge valve
2
Dosing head
3
Suction valve
Ensure that there is sufficient free space (f) around the dosing head, as
well as the suction and discharge valve, so that maintenance and repair
work can easily be carried out on these components.
Base
h
P_MOZ_0016_SW
Fig. 8
Space requirement
A
A
P_MOZ_0018_SW
Fig. 9
1
3
2
f
f
f
P_MOZ_0017_SW
Fig. 10
Assembly
15
Содержание Sigma / 2 Basic Type SBKa
Страница 51: ...51 ...