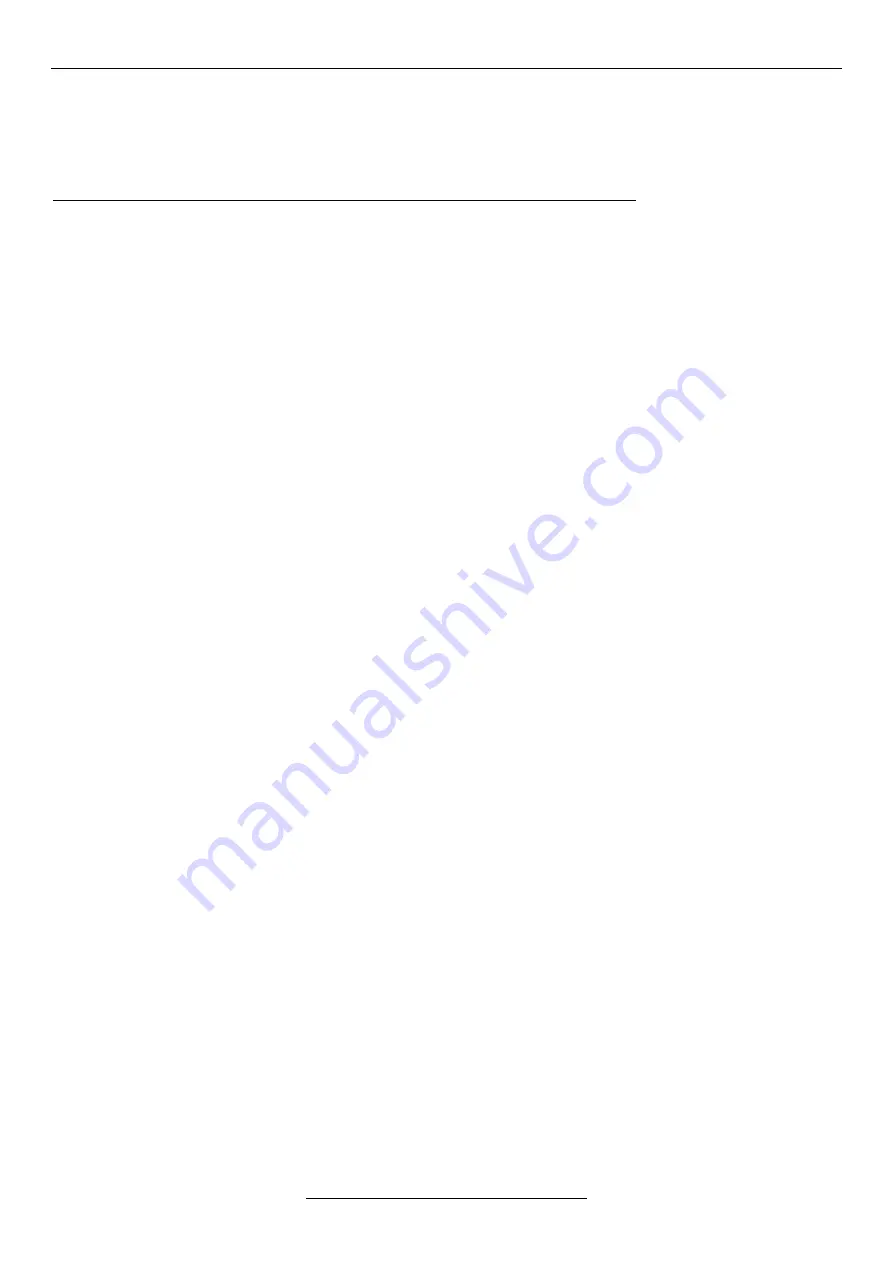
H - I - J
PROGRAMMER’S MANUAL
V8.94.11-
- 13 -
Features and capabilities of the frequency converter and the program
For changing the parameters, the programmer or operator terminal (built in the frequency converter or stand-alone unit)
or the regulator terminal (built in the frequency converter).
For the continuous inspection of all parameter values use of a display may be needed.
Some options for being built in the equipment (differs for the V3D, VLD and VHD types!):
•
PID extension, or adding further relays for further feedbacks,
•
fitting with further digital inputs,
•
analogue output,
•
fitting with IRE reception for rotation speed control or position adjustment,
•
CAN bus connection (e.g. master / slave),
•
a second RS 485 serial line for remote control (MOD bus).
Through the features and capabilities, the manufacturer aims to make the frequency converter proper for the most
possible scopes of application.
The analogue and digital inputs, outputs and relays facilitate solving complex control and regulation tasks
Some programming options (differs for the V3D, VLD and VHD types!):
•
programmability of procedures up to 15 steps (even different in each parameter chart),
•
arbitrary acceleration and deceleration times, frequencies, regulation parameters, durations etc.,
•
a maximum of 3 kinds of digital feedback on the internal state of the frequency converter
(on optocouplers or relays),
•
two free programmable analogue output back indications,
•
two (optionally four) free programmable analogue input signals for regulation or control
(potentiometer, voltage or current),
•
“S”-curve type soft start and stop (for materials handling and passenger transport),
•
timing functions, delayed starts and stops, preset operation periods,
•
counting functions (to be activated with the digital inputs, or program group cycle counter), counting by piece,
or operation depending on the counted value (counting down and stop at zero)
•
multifunction display (optionally selectable parameter displays)
•
modification of the main parameter values from analogue input (e.g. acceleration time, fmax, etc.),
•
several motor control tasks (one controlled and a maximum of three fix switchable),
•
reception of the rotation speed feedback signal from the driven shaft (not necessarily the motor shaft)
(Incremental rotation speed encoder, IRE),
•
rotation speed regulation tasks,
•
position regulation tasks,
•
torque regulation tasks,
•
master/slave operation tasks,
•
synchronised systems, also with acceptance of IRE reference signal,
•
correct motor protection based on the preset motor parameters,
•
automatic error acknowledgement (useful with unattended equipment which can restart in this way!),
•
elimination of resonance frequencies by inhibiting,
•
implementation of optional voltage/frequency characteristics (e.g. for special motors),
•
keeping an error log with error numbers and chronology (256 errors can be stored inspected),
•
Optional computer connection (query, program editing, data processing, etc.),
•
etc.
Содержание V3D Series
Страница 1: ...H I J frequency converters programmer s manual from software version V8 94 11 onwards P Since 1984...
Страница 2: ......
Страница 85: ...H I J PROGRAMMER S MANUAL V8 94 11 85 User settings Submenu Explanation Setting Unit...
Страница 86: ...H I J PROGRAMMER S MANUAL V8 94 11 86 Notes...
Страница 87: ......