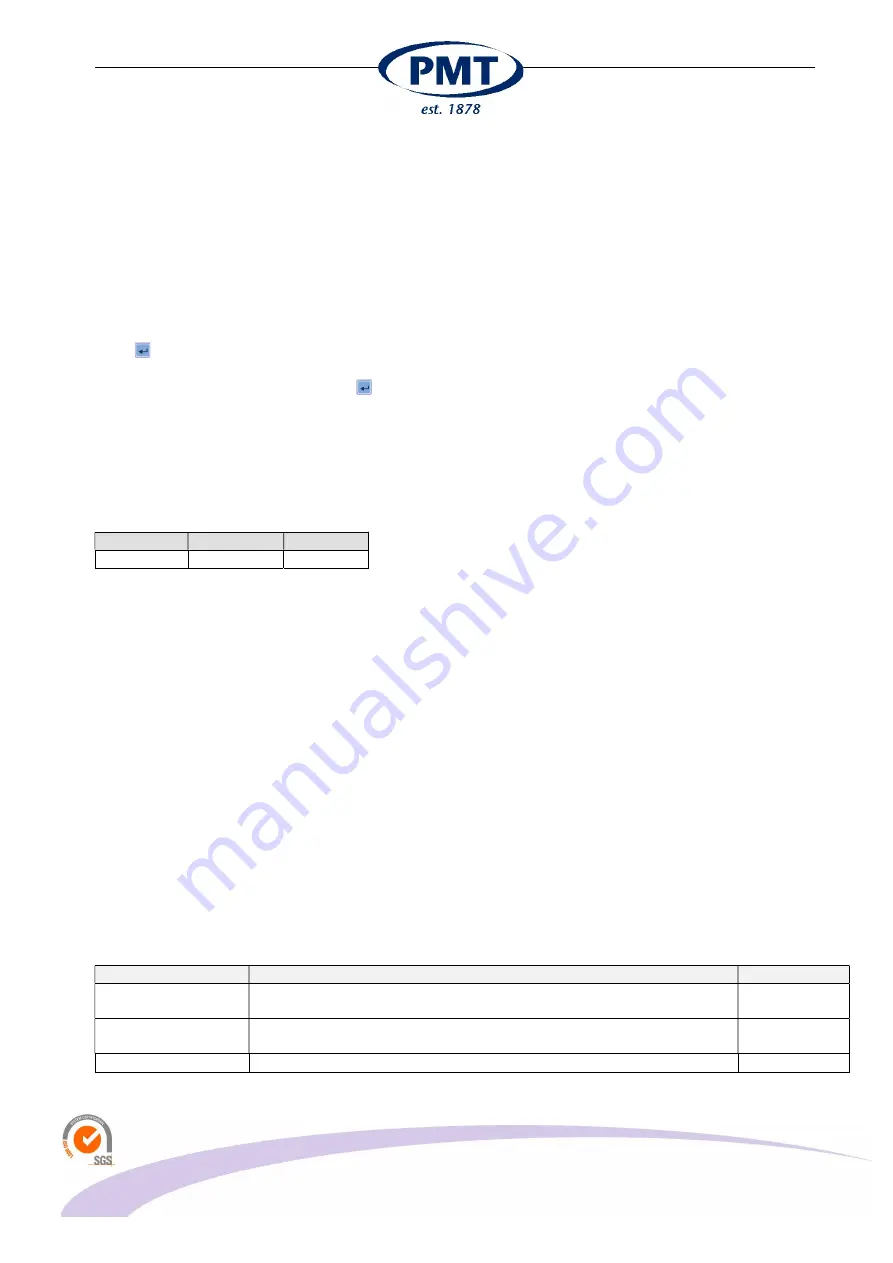
E-mail: [email protected]
Website: www.tamson.com
van 't Hoffstraat 12
2665 JL Bleiswijk, THE NETHERLANDS
T. 31 (0) 10 522 43 73
ttu-tb-tlb-tlc.docx Rev. 1.04 UK 0720
Tamson Instruments B.V.
Page 29/39
VAT: NL 80 66 34 984 B01
Bank account no.:
NL28 INGB 0007 350 370
NL95 RABO 0160100046
Chamber of commerce 27 16 95 41
ISO 9001 : 2015
NL/PRO 238239125
10 USING PID FOR STABLE TEMPERATURE CONTROL
10.1 ADJUST SET POINT
To start operating the bath:
Fill the bath with fluid to flood the cooling coil, However
do not fill the bath fully to the maximum.
Place the power plug, switch the bath on using the mains
switch,
Choose a working temperature (set point):
Press once. Display will indicate "set point". Alter set
point temperature by using up and down key to select the
desired bath temperature. Press to
confirm and
display bath temperature again.
10.2 TUNING THE BATH
Tuning can be done manually. The parameters
mentioned in Table 1 will influence the control of the bath.
The PID parameters are set to
P
I
D
25
16
0
These parameters work fine for following bath contents:
- Water
- Water / Glycol
- Silicone oil, < 10cSt @ 25°C
- Mineral oil, < 10cSt @ 25°C
The temperature control of the bath is based on a digital
PID system. When using different fluids in the bath each
with their own heat capacity, the use of external cooling
and external connected processes (circulation), or
working at different set point temperatures requires new
settings of the PID parameters. These parameters have
to be optimized after changes to the system when optimal
and accurate temperature control of the bath liquid is
required.
Tuning of the bath results in:
Stable temperature control of the bath,
No over- or undershoot of the temperature set point,
Quick response to deviations from the set point caused
by external disturbances.
Parameter
Description
Display
Proportional band
The bandwidth in display-units over which the output power is
proportional between minimum and maximum
Pb
Integration time
Determines the time taken by the controller to remove steady state error
signals
Ti
Derivative time
Determines the time taken by the controller to react on error signals.
Td
Table 2 Parameters influencing the temperature control