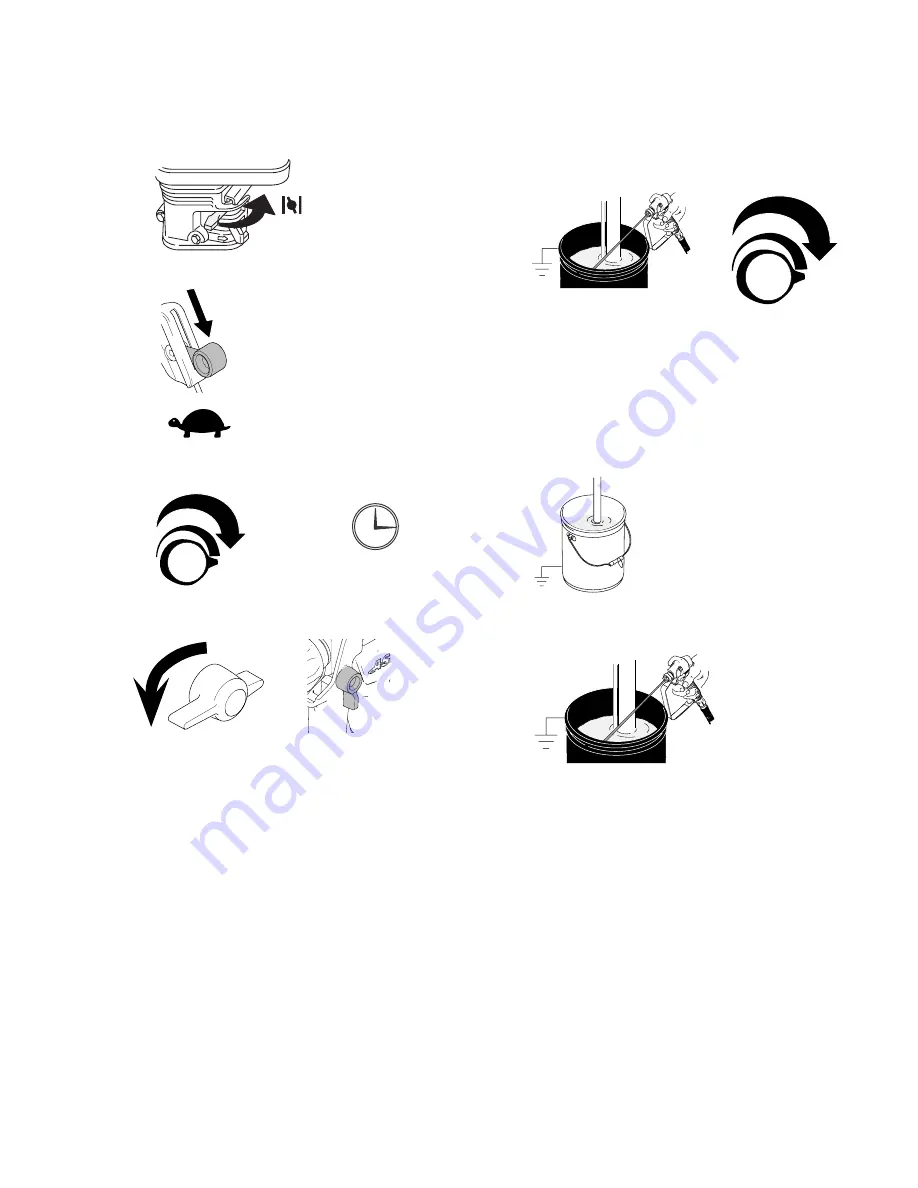
Operation
3A0441A
9
f.
After engine starts, move choke to open.
g.
Set throttle to desired setting.
3.
Increase pressure enough to start pump. Allow fluid
to circulate for 15 seconds.
4.
Turn pressure down, close prime valve. Disengage
gun trigger safety.
5.
Hold gun against grounded metal flushing pail. Trig-
ger gun and increase fluid pressure slowly until
pump runs smoothly.
Inspect fittings for leaks. Do not stop leaks with your
hand or a rag! If leaks occur, turn striper OFF immedi-
ately. Perform Pressure Relief (page 8). Tighten leaky
fittings. Repeat Startup, steps 1-2. If no leaks, continue
to trigger gun until system is thoroughly flushed.
Proceed to step 3.
6.
Place siphon tube in paint pail.
7.
Trigger gun again into flushing fluid pail until paint
appears. Assemble Uni-Tip and Uni-Tip Guard.
ti3317a
ti15280a
15 SEC.
ti15273a
ti15265a
ti10353a
FLUSH
ti15267a
ti15273a
PAINT
ti3316a
FLUSH
ti15267a
Содержание Brite Stripper 3000SP
Страница 46: ...Notes 46 3A0441A Notes ...
Страница 47: ...Notes 3A0441A 47 Notes ...