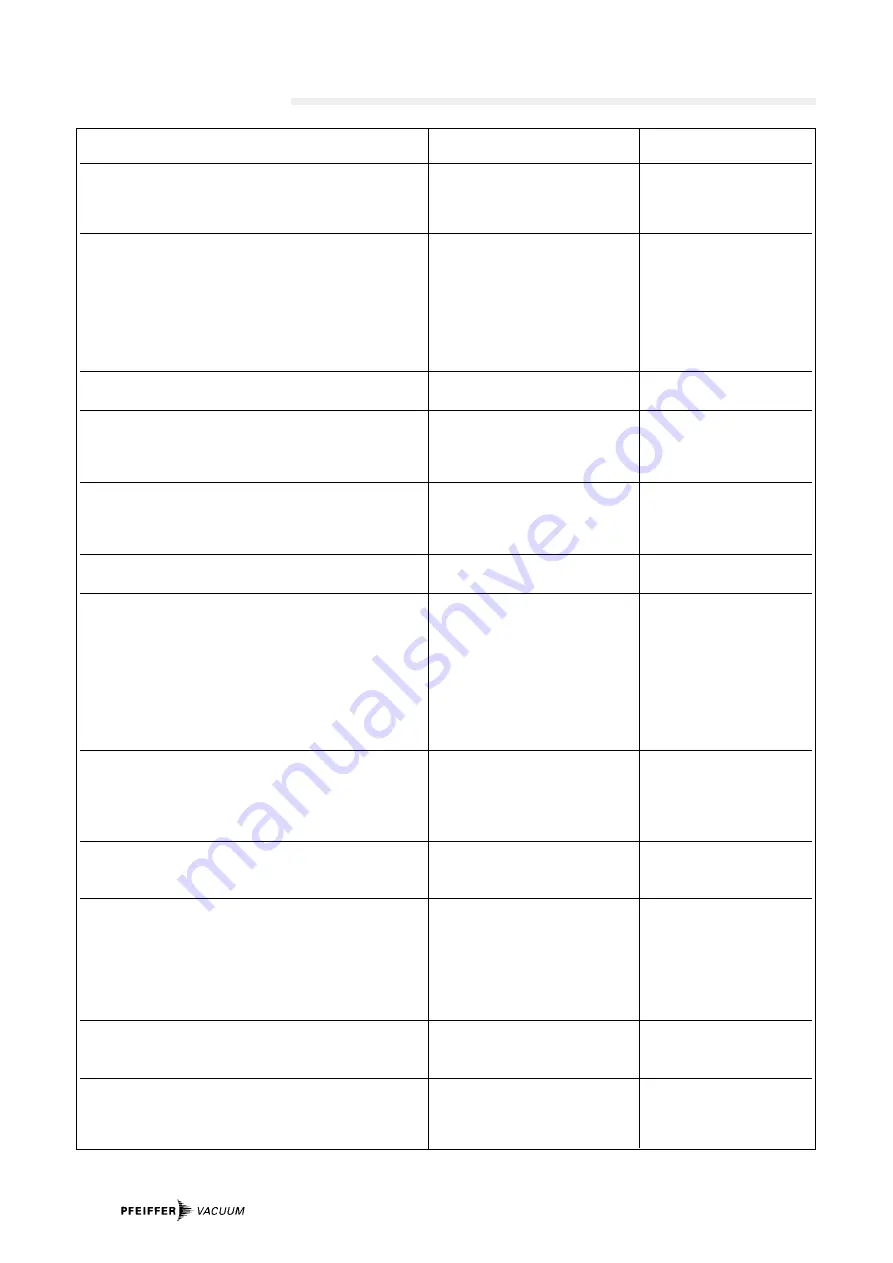
14
8. Technical Data
Feature
Unit
TMH 1600M
TMH 1600M
TMH 1600M H
TMU 1600M
TMU 1600M
Connection nominal diameter:
Inlet
DN 200 ISO-K
DN 250 ISO-K
DN 200 ISO-K
DN 250 ISO-K
DN 200 CF-F
DN 250 CF-F
Outlet
DN 40 ISO-KF
DN 40 ISO-KF
Magnetic bearing controller
TCM 1601
TCM 1601
Nominal rotation speed without TMS
1/min
36 000
36 000
Nominal rotation speed with TMS
1/min
33 000
33 000
Standbyrotation speed
1/min
24 000
24 000
Start-up time (up to 90% of the nominal
rotation speed with TCM 1601)
(bis 90 % Nenndrehzahl mit TCM 1601)
min
6
7
Noise level
dB (A)
55
55
Maximum permissible rotor temperature
°C
120
120
Permissible heat radiation power
W
27
27
Volume flow rate (with oil-sealed rotary vane vacuum pump):
Stickstoff N2
l/s
1000
1400
1000
1400
Helium He
l/s
1100
1180
1100
1230
Wasserstoff H2
l/s
750
780
750
850
Compression ration for:
N2
–
> 1 · 1010
> 1 · 108
He
–
5 . 105
2 . 104
H2
–
1 · 104
2 · 103
Critical backing pressure, max.
N2
Cooling type: water
mbar
9
3
Gas throughput without TMS operation at nominal rotation speed, max.
N2 Cooling type: water
mbar l/s
9
15
Ar Cooling type: water
mbarl/s
4,5
6
Gas throughput with TMS operation at nominal rotation speed, max1)
N2 Cooling type: water
mbarl/s
7
12
Ar Cooling type: water
mbarl/s
3,5
5
Gas throughput at 0,1 mbar intake pressure
N2 Cooling type: water
mbarl/s
16
20
Ar Cooling type: water
mbarl/s
12
14
Vertex power characteristics line2)
A
W / Hz
400
400
B
W / Hz
580
480
C
W / Hz
360
360
D
W / Hz
360
360
Theoretical final pressure
mbar
< 1 · 10-11
< 1 · 10-11
Final pressure 1 (metal seal with backing out)
mbar
< 1 · 10-10
–
Final pressure 2 (viton seal without backing out)
mbar
< 1 · 10-8
< 5 · 10-8
Cooling water consumtion with water at 15 ˚C
without TMS operation
l/h
20
20
with TMS operation and gas load
l/h
100
100
Cooling water temperature
˚C
5 - 25
5 - 25
Permissible ambient temperature with
air cooling
˚C
5 - 30
5 - 30
water cooling
°C
5 - 35
5 - 35
Power consumption of:
casing heating unit
W
170
170
TMS heating
W
1000
1000
Permissible magnetic field
mT
4
4
Protection class
IP 20
IP 20
Weight
kg
61/63
62/64
61
63
Relative humidity
%
5-85 non-condensing
5-85 nicht betauend
1)
Operation with TMS only with water cooling
2)
For gas type characteristics line please refer to Section 4.6.