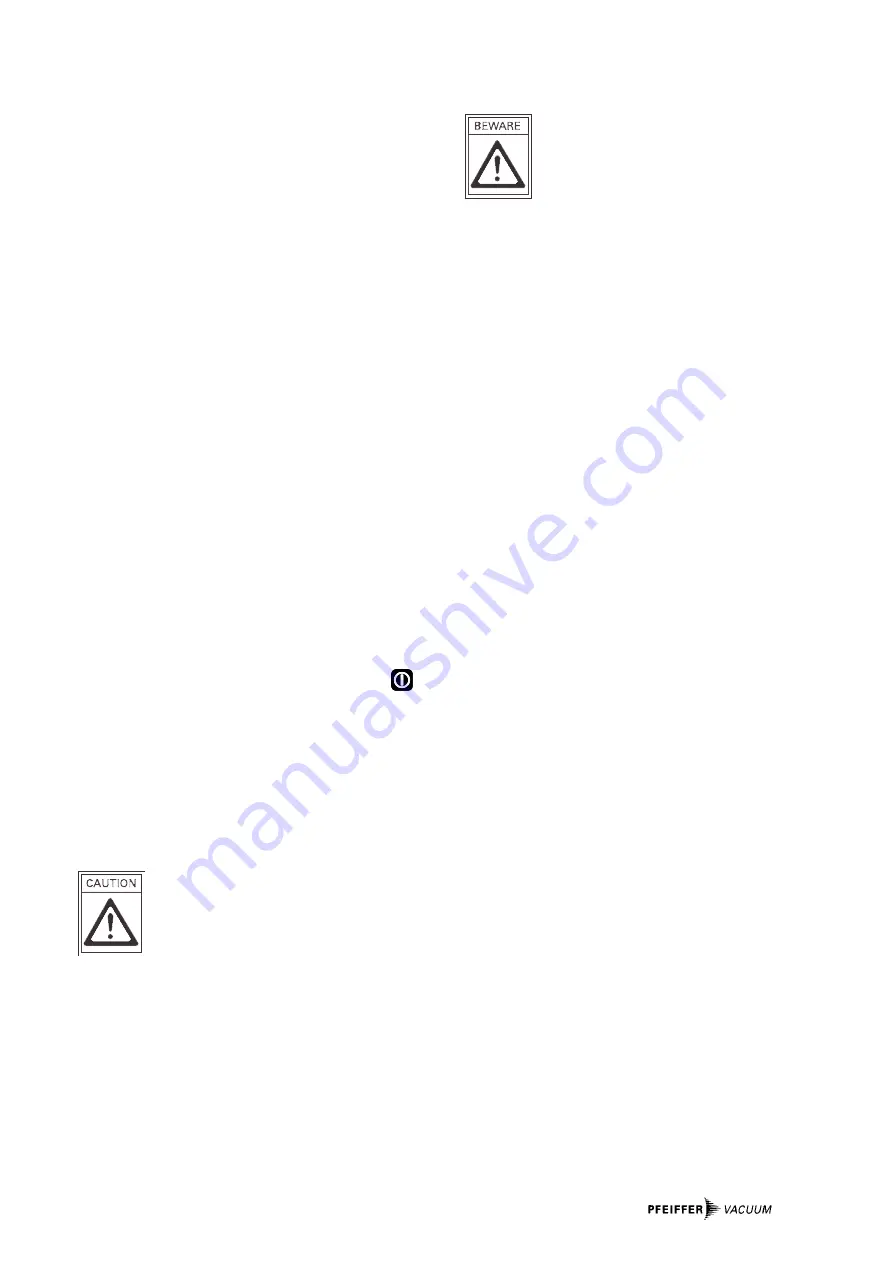
11
4.7. Safety Bearings
Where heavy, external vibration or improper operating is
involved, the rotor is supported by an additional, dry-running
safety bearing; a clearly audible sound is produced when this
happens. The various causes are evaluated as follows:
– Power failure; Display Warning F 007;
only low level strain on the safety bearing and, with a new
safety bearing set, possible 100 times.
– Uncontrolled venting or vibration;
Malfunction Display E 089;
medium level strain on the safety bearing, and, with a new
safety bearing set, possible 50 times.
– Cable disconnected between the electronics and the
pump; Malfunction Display E 082;
high level strain on the safety bearing, and, with a new
safety bearing set, possible 5 times.
If there is a mix of the events referred to above, the criteria
for the actual wear of the safety bearing is the sum of the par-
tial wear arising from the individual events.
Please get in touch with your local PFEIFFER Service when a
safety bearing replacement is required.
4.8. Switching OFF And Venting
When switching off and venting the turbopump please take
account of the fact that various venting modes are available
(please refer to the operating instructions for the TCM 1601,
PM 800 478 BN).
➡
Switch off the pumping station with the push button
on the front panel of the TCM 1601.
➡
Close the fore-vacuum safety valve (if available). Where
Pumping Station Control Unit TCS 180 is involved, the valve
closes automatically.
➡
With water cooling: Shut off the water supply.
➡
Shut off the supply of sealing gas if operating with sealing
gas.
➡
Do not switch off the TCM 1601 or disconnect from the
mains until the rotation speed has reached 0 Hz.
When operating the pump with aggressive
gases and their reactive products, the operation
of the backing pump and the sealing gas func-
tion should be continued for at least 15 minutes
in order to protect the bearings and the drive
and to ensure the complete pumping out of this media.
4.9. Shutting Down For Longer Periods
Vacuum pumps are sometimes used to pump
aggressive or hazardous gases. There is a dan-
ger of personal injury resulting from coming into
contact with process gases. Before removing a
turbopump from the system, first:
– Vent the turbopump with a neutral gas or dry air.
– Ensure that there is no residual process gas in the system
nor in the supply lines.
If the turbopump is to be shut down for more than a year:
➡
Remove turbopump from the system.
➡
Close the high vacuum flange and evacuate the turbopump
via the fore-vacuum flange.
➡
Vent turbopump via the venting connection with nitrogen
or dry air.
➡
Close fore-vacuum connection by blank flanging.
➡
Place the pump vertically on its synthetic feet.
➡
In rooms with moist or aggressive atmospheres, the turbo-
pump must be air-sealed in a plastic bag together with a
bag of dessicant, e.g silicagel.