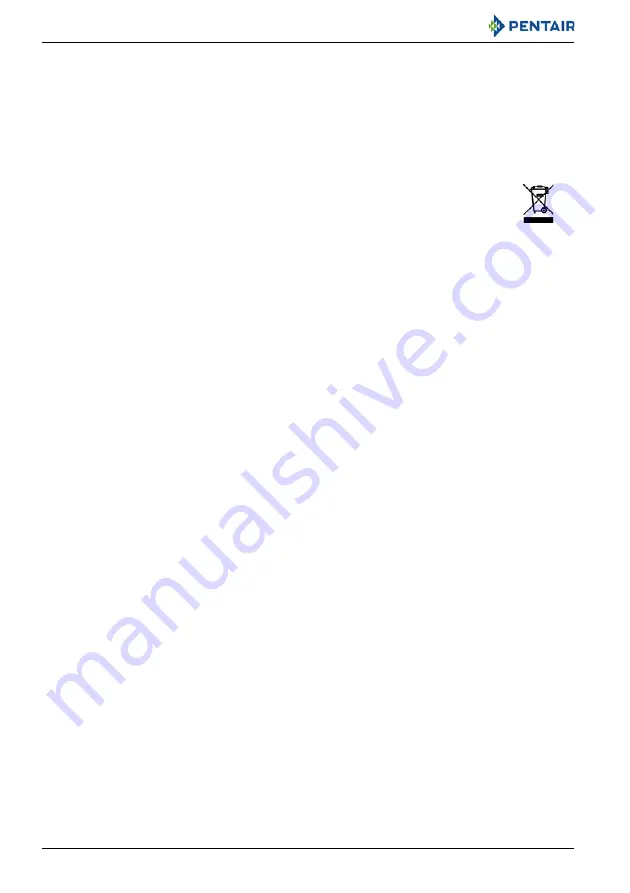
Installer Manual Fleck 4600 - MECH - Disposal
86 / 88
Ref. MKT-IM-027 / B - 01.06.2018
12.
Disposal
The device must be scrapped in accordance with directive 2012/19/EU or the environmental standards
in force in the country of installation. The components included in the system must be separated and
recycled in a waste recycling center that conforms with the legislation in force in the country of
installation. This will help to reduce the impact on the environment, health, safety and help to promote
recycling. Pentair does not collect used product for recycling. Contact your local recycling center for
more information.
Содержание Fleck 4600-MECH
Страница 1: ...FLECK 4600 MECH INSTALLER MANUAL WATER PURIFICATION ...
Страница 16: ...Installer Manual Fleck 4600 MECH Description 16 88 Ref MKT IM 027 B 01 06 2018 3 2 Outline drawing ...
Страница 59: ...Installer Manual Fleck 4600 MECH Maintenance Ref MKT IM 027 B 01 06 2018 59 88 ...
Страница 61: ...Installer Manual Fleck 4600 MECH Maintenance Ref MKT IM 027 B 01 06 2018 61 88 ...
Страница 74: ...Installer Manual Fleck 4600 MECH Spare parts 74 88 Ref MKT IM 027 B 01 06 2018 11 3 Valve parts list ...
Страница 76: ...Installer Manual Fleck 4600 MECH Spare parts 76 88 Ref MKT IM 027 B 01 06 2018 11 4 Meters parts list ...
Страница 87: ...Installer Manual Fleck 4600 MECH Disposal Ref MKT IM 027 B 01 06 2018 87 88 PAGE INTENTIONALLY LEFT BLANK ...
Страница 88: ...www pentairaquaeurope com ...